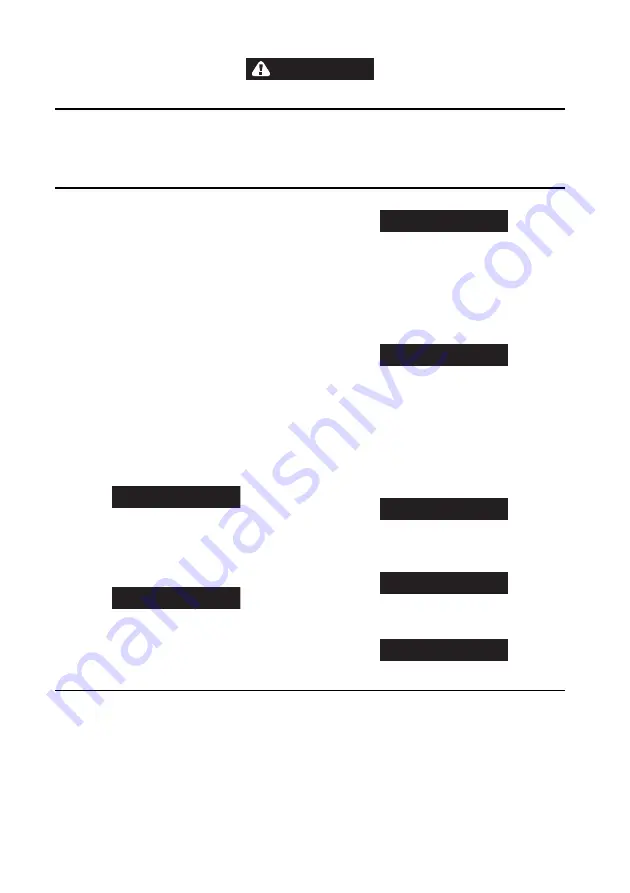
2
Form 04584256-Edition 1
WARNING
Always wear eye protection when operating or performing maintenance on this tool. Always turn off the air supply and disconnect the air supply
hose before installing, removing accessory on this tool, or before performing any maintenance on this tool.
Lubrication
Each time a Series 2908P Air Impact Wrench is disassembled for
maintenance and repair or replacement of parts. lubricate as follows:
1.
Work approximately 6 to 8 cc of
Ingersoll-Rand
Grease No. 105 into
the impact mechanism. Coat Anvil (46) lightly with grease around the
Hammer Case Bushing (41). Inject approximately 1 to 2 cc of grease
into the Grease Fitting (23).
2.
Use
Ingersoll-Rand
Medium Oil No. 10 for lubricating the motor.
Inject approximately 1 to 2 cc of oil into the air inlet before attaching
the air hose. Remove the Oil Chamber Plug (15) and fill the oil
chamber.
Disassembly
General Instructions
1.
Do not disassemble the tool any further than necessary to replace or
repair damaged parts.
2.
Whenever grasping a tool or part in a vise, always use leather-
covered or copper-covered vise jaws to protect the surface of the
part and help prevent distortion. This is particularly true of threaded
members and housings.
3.
Do not remove any part which is a press fit in or on a subassembly
unless the removal of that part is necessary for repairs or
replacement.
4.
Do not disassemble the tool unless you have a complete set of new
gaskets and O-rings for replacement.
Disassembly of the Air Impact Wrench
1.
Clamp handle of Air Impact Wrench in a vise with square driver
upward.
2.
Unscrew and remove the four Hammer Case Cap Screws(45).
3.
While lightly tapping on end Anvil (46) with a plastic hammer, lift off
the Hammer Case (40).
4.
Grasp Hammer Frame (36) and carefully lift off entire impact
mechanism, making certain not to drop the two Hammer Pins (37). If
it is necessary to disassemble the impact mechanism, refer to
Disassembly of the Impact Mechanism
on this Page. If it is
unnecessary to disassemble the impact mechanism, set it aside
intact.
Disassembly of the Impact Mechanism
1.
Set mechanism, driver end up, on a workbench.
NOTICE
Note the twin Hammers within the Hammer Frame. These are
identical but must be placed in the Hammer Frame in a certain
relationship. Using a felt tipped pen, mark the top Hammer “T
y
” and
the bottom Hammer “B
y
” with the arrows pointing upward. Mark
both Hammers on the same end.
2.
With mechanism sitting upright on the workbench, slowly rotate the
Anvil in a clockwise direction until it comes up solid.
NOTICE
If you continue to rotate the Anvil, it will cam the Hammers out of
engagement. Do not allow this to happen; merely rotate the Anvil
until it comes up solid.
3.
Hold the Hammer Frame firmly and, without disturbing the Hammers,
gently lift the Anvil, simultaneously rotating it clockwise about 1/8 of a
turn, from Hammer Frame.
NOTICE
The twin hammers will be free to slide from the Hammer Frame when
the Hammer Pins are removed. Do not drop the Hammers.
4.
With the Anvil removed, lift out the two Hammer Pins.
5.
Remove the Hammers.
Disassembly of the Motor
1.
Lift Rear Hammer Frame Washer (38) and two Motor Clamp
Washers (35) from front of motor.
2.
Grasp splined end of Rotor (28) and pull assembled motor from
Motor Housing (1).
NOTICE
Be careful not to lose the small End Plate Dowel (32)
3.
Lift Front End Plate (33) and Front Rotor Bearing (34) from splined
end of the Rotor (28).
4.
Remove Cylinder and Vanes (29).
5.
Remove Rear Rotor Bearing Retainer (25).
6.
Lift Rear End Plate and Rear Rotor Bearing (26) from Rotor.
7.
Remove Oiler Retaining Ring (12A).
8.
Unscrew and remove Air Strainer (13).
9.
Withdraw Exhaust Deflector (6), Oiler Assembly (10), Throttle Valve
Spring (9) and Throttle Valve (8).
10. Withdraw Trigger Assembly (3).
11. If the Throttle Valve Seat (7) must be replaced, thread a long 3/8‘‘
cap screw into it and withdraw it from the handle.
NOTICE
Do not remove the Throttle Valve Seat unless you have a new
Throttle Valve Seat on hand for installation.
12. Unscrew Reverse Valve Knob Screw (22) and remove Reverse Valve
Knob (21).
NOTICE
This Screw is installed with Loctite
®*
13. While slowly rotating Reverse Valve (18), withdraw it from Reverse
Valve Bushing (16).
NOTICE
Be careful you do not lose the Reverse Valve Detent Ball (19) and
Spring (20) from the hole in the side of the Reverse Valve.
Assembly
General Instructions
1.
Always press on the
inner
ring of a ball–type bearing when installing
the bearing on a shaft.
2.
Always press on the
outer
ring of a ball–type bearing when installing
the bearing in a bearing recess.
3.
Whenever grasping a tool or part in a vise, always use leather–
covered or copper–covered vise jaws to protect the surface of the
part and help prevent distortion. This is particularly true of threaded
members and housings.
* Registered trademark of Loctite Corporation.
4.
Always clean every part and wipe every part with a thin film of oil
before installation.
5.
Apply O-ring lubricant to every O-ring before assembly.
6.
Check every bearing for roughness. If an open bearing must be
cleaned, wash it thoroughly in
clean
solvent and dry it with a clean
cloth.
Sealed or shielded bearings should never be cleaned.
Work grease thoroughly into every open bearing before installation.