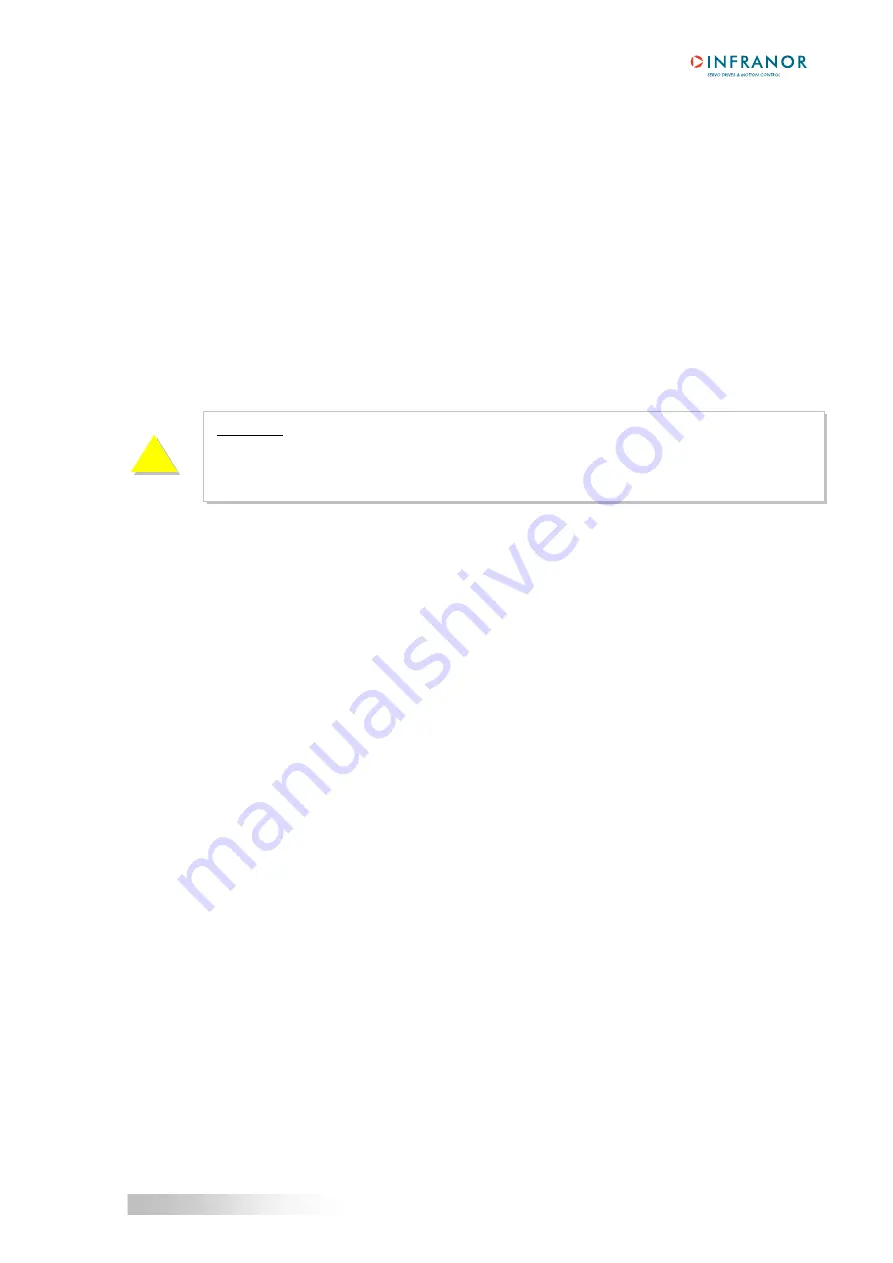
33
Chapter 4 - Connections
CD1-k – Installation Guide
3 - FIRST POWERING OF THE AMPLIFIER
3.1 - VERY IMPORTANT
Check the connections, especially of the 24 VDC and power supplies. There are two different voltage ratings:
230 Vac and 400 Vac. Check that the appropriate sticker actually corresponds to the power connections.
A 400 Vac connection on a 230 V amplifier will destroy it.
The INHIBIT signal (X2 connector, pin 1) must be disabled.
Check for the braking resistor sizing:
- dp 100/100 for 230 VAC,
- dp 200/100 for 400 VAC and current ratings 1.8 to 7.2,
- dp 50/200 for 14 A current rating,
- dp 33/280 for 30 and 45 A current ratings,
- EF 400 for 70 and 90 A current ratings.
Check for the correct groundings as well as the 360° shield connections.
3.2 - SWITCHING ON THE 24 Vdc SUPPLY
The green "OK" LED on the front panel must be flashing ("Undervolt." error displayed).
The AOK relay (pins 9 and 10 of X2) is closed. It is then possible to control the power relay (Rpu) according to the
instruction of
Connection according to X8 sticker.
3.3 – SWITCHING ON THE POWER SUPPLY (230 Vac or 400 Vac according to the amplifier type)
The green "OK" LED on the front panel must be continuously lit.
3.4 - COMMISSIONING
For further details regarding the amplifier commissioning, please see manual
CD1-k – User Guide
.
4 - REQUIREMENTS FOR THE COMPLIANCE WITH THE UL STANDARDS
The UL listing requires the following conditions to be fulfilled by the installer of the amplifiers.
4.1 - CONNECTION BY MEANS OF A FASTON SOCKET
The installer of the amplifiers must use a UL Listed Quick connect for ground connection (0.250 inches or 6.35
mm wide nominal) on all amplifiers equipped with FASTON sockets.
On amplifiers equipped with a screwed ground connector, the connection must be made via UL listed sockets.
4.2 - 24 V SUPPLY
The end user has to provide a 24 VDC isolated power supply (i.e. with an isolation transformer) for the auxiliary
supply input, protected by a 4 A UL listed fuse.
!
WARNING !
During the machine adjustments, amplifier connection or parameter setting errors may involve
dangerous axis movements. It is the user's responsibility to take all necessary steps in order to
reduce the risk due to uncontrolled axis movements during the operator's presence in the concerned
area.