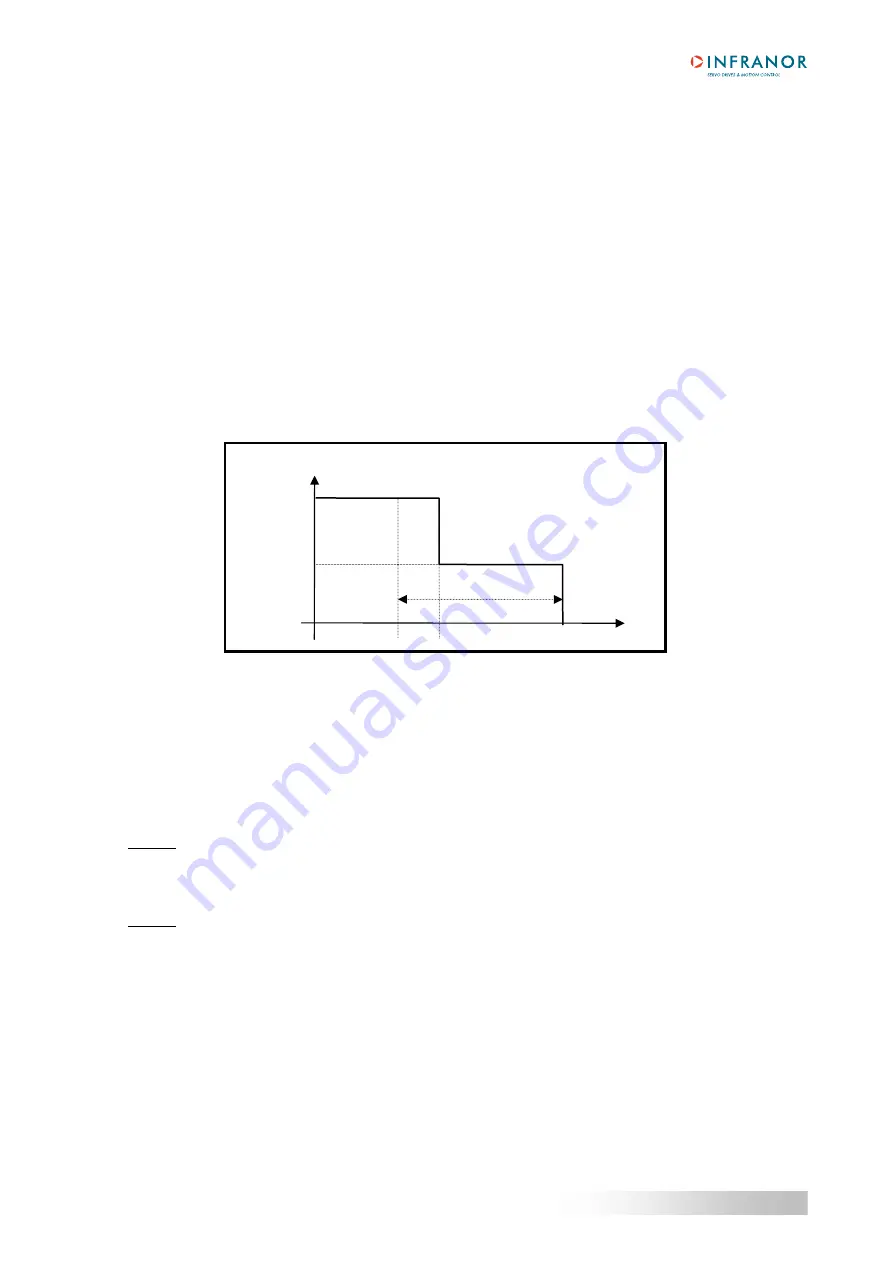
10
CD1-k – User Guide
Chapter 2 - Commissioning
4.2 - I
2
T PROTECTION
2 selection modes are available:
Fusing
or
Limiting
.
It is advisable to use the
Fusing
mode during commissioning phases.
In
Fusing
mode, the amplifier is disabled when the current limitation threshold is reached.
In
Limiting
mode, the motor current is only limited at the value defined by the
Rated current
parameter when the
limitation threshold is reached.
4.2.1 - OPERATION OF THE CURRENT LIMITATION IN "FUSING" MODE
When the amplifier output RMS current (I
2
t) reaches 85 % of the rated current, the
OK
LED is blinking on the
amplifier front panel. If the RMS current (I
2
t) has not dropped below 85 % of the rated current within 1 second, the
I
2
t error is released and the amplifier disabled (otherwise, the blinking is inhibited).
When the amplifier output RMS current (I
2
t) reaches the rated current value, the I
2
t limits the amplifier output
current at this value.
Diagram of the amplifier output current limitation in an extreme case (motor overload or shaft locked):
The maximum current duration before release of the blinking display is depending on the value of the parameters
Rated current
and
Max. current
. This value is calculated as follows:
T
dyn
(second) = t
1
-t
0
= 3,3 x
[
rated current (A) / max. current (A)
]
2
The maximum current duration before limitation at the rated current is also depending on the value of the
Rated
current
and
Maximum current
parameters. This value is calculated as follows:
T
max
(second) = t
2
-t
0
= 4 x
[
rated current (A) / max. current (A)
]
2
NOTE 1
When the "Max. current / Rated current" ratio is close to 1, the Tdyn and Tmax values given by the formula above
are quite below the real values. But this formula remains very precise as long as the "Max. current / Rated current"
ratio is higher than 3/2.
NOTE 2
The amplifier I
2
t signal can be displayed on the digital oscilloscope by selecting the
I
2
t
signal in the
Channel
menu. The threshold values of the I
2
t signal, for the protection mode described above, are calculated as
follows:
Triggering threshold of the Idyn signal (%) =
[
Rated current
(%)
]
2
/ 70
Current limitation threshold (%) =
[
Rated current
(%)
]
2
/ 50
Rated current (%) = 100 x Rated current (A) / amplifier current rating (A)
The corresponding RMS current value of the amplifier can be calculated as follows:
Amplifier RMS current (A) =
[
I
2
t signal value (%) x 50
]
1/2
x
amplifier current rating (A) / 100
Max. current
t0
t3
Rated current
t1
t2
Amplifier output current
1 second
t1 = Blinking
t2 = Current limitation
t3 = I
2
t error
time