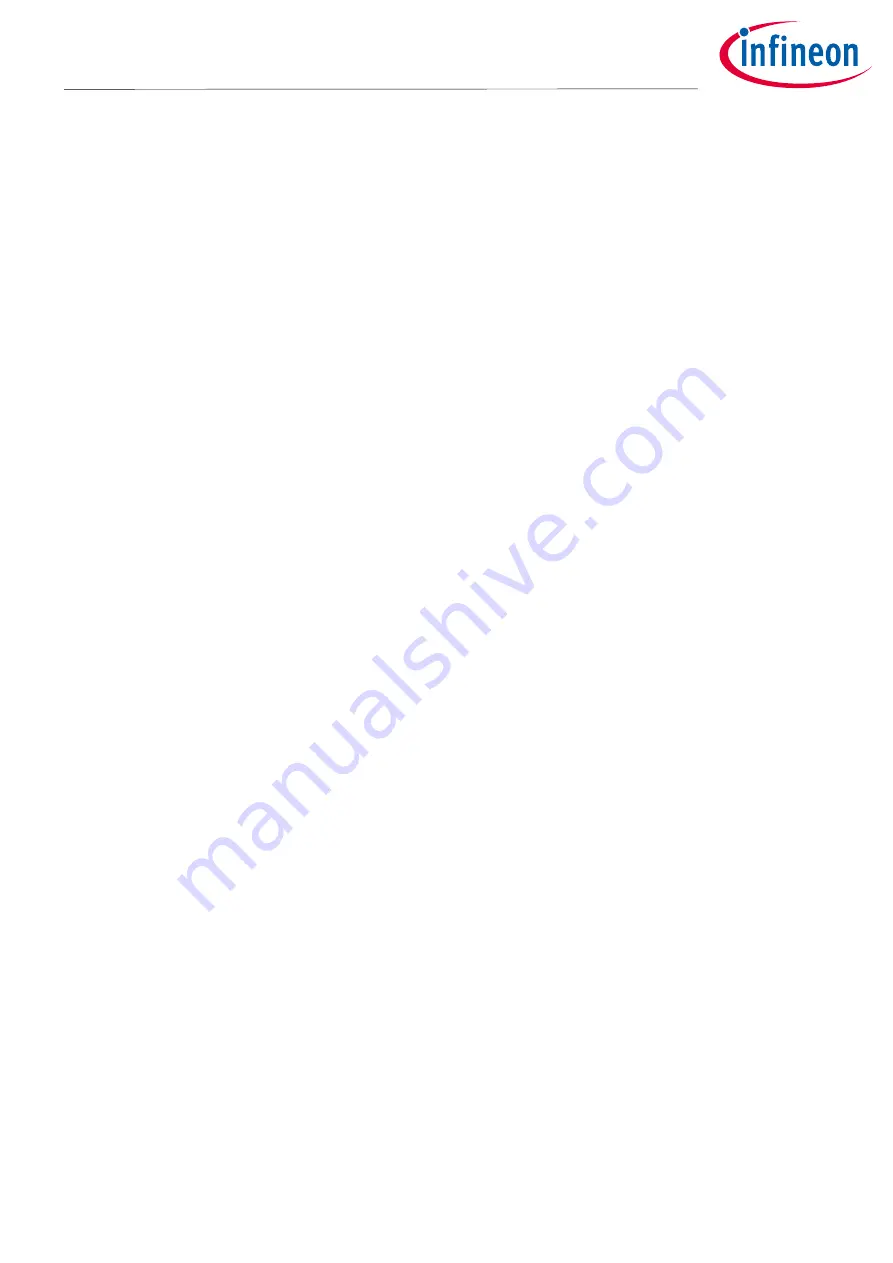
Application Note
14
Revision 1.0
2017-11-15
1200V HighSpeed 3 IGBT in TO-247PLUS Evaluation Board
User Manual
Usage
8. If required, connect a power supply to the HEAT+/HEAT- terminals and set the voltage level
according to 3.1.4. Monitor the temperature using an ohmmeter connected to SENSE+/SENSE-.
9. Connect a high voltage source to VIN and PGND and short VIN and VOUT.
10. Slowly increase the voltage and monitor the current and voltage waveforms on the oscilloscope.
3.2.3
Efficiency or temperature measurements
Testing a particular semiconductor device inside a switching cell is essential for understanding its
switching behavior. However, it requires some calculation or simulation effort to translate the acquired
switching loss data into quantities that are more relevant for an application, such as the efficiency of the
converter, the temperature of the devices or the required cooling effort. By operating the evaluation
board in a continuous manner these values can be determined in a purely experimental and thus
straightforward way. The remainder of this section explains how to configure and run the board as a
buck converter as sketched in configuration (3) of Table 3.
Prior to running the evaluation board as a buck converter, some preparations are required:
1. Short circuit the shunt resistor R201 in order to avoid unnecessary power dissipation.
2. Disable the LEDs that indicate the presence of the DC link voltage by removing R134, R138 and
R142. Otherwise consider the power dissipation of this block: 1.6W at 800V.
3. Replace the heat sink
a) Unfasten the M3 screws that fix the heat sink to the board.
b) Pull the heat sink away from the board so that the spring clips fall off.
c) Unsolder the power resistor E200 and the NTC B200.
d) Remove the probe adapter Id2 from the board.
e) If necessary, solder the film capacitors C203 and C204 to the other side of the board.
f) Mount a reasonable heat sink. If possible put an insulation sheet between heat sink and board.
4. Replace the filter inductor
a) Disconnect the daughter card containing the inductor by unfastening the M4 screws.
b) Connect a custom inductor between the VMID and the VOUT potential.
After the preparation steps, the efficiency measurements can be performed.
1. Assemble the devices under test S
1
and S
2
as described in section 3.1.1.
2. Connect the driver to the proper emitter pin according to section 3.1.2.
a) Solder 0
Ω resistors to R214/R224 when using three pin packages
b) Solder 0
Ω resistors to R213/R223 when using four pin packages
3. Adjust the driving circuitry for S
1
and, if necessary, also for S
2
according to section 3.1.3.
a) Set the jumper X111/X121 to ADJ.
b) Use the jumper X112/X122 to set the turn-off voltage to 0V or -5V.
c) Adjust the turn-on and turn-off gate resistors R211/R221 and R212/R222, respectively.
4. Connect isolated voltage probes to measure the gate as well as the collector-emitter voltage of S
1
and use a current probe to measure the inductor current.
5. Connect an auxiliary power supply to the 12V/SGND terminals of the board and provide a supply
voltage of 12V.
6. Connect a signal generator to X210 and provide a PWM signal with 5V amplitude. Please note that
this signal is referenced to SGND.
7. Check the gate voltage signal on the oscilloscope and adjust the turn-on voltage level to +15V using
the potentiometer R110.
8. Connect a high voltage source to VIN and PGND.
9. Connect an Ohmic load to VOUT and PGND.
10. If possible, measure the input and output power using a power meter and the device temperatures
using an infrared camera.
11. Slowly increase the input voltage while monitoring the waveforms and device temperatures.