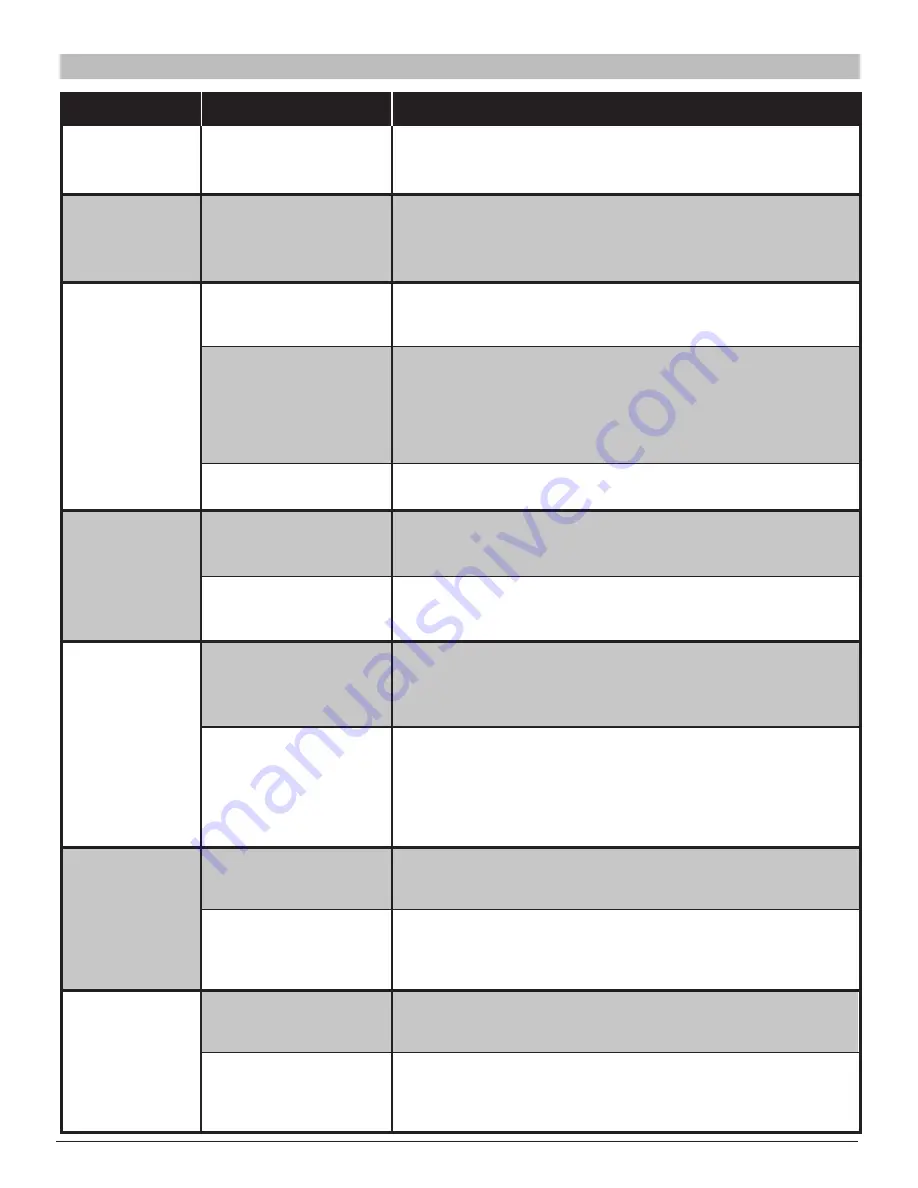
14
All of the components and features of your new Incra Jig
Ultra Lite have been factory set and should require no
further adjustment. If, however, you wish to recalibrate
these components, the following information is provided to
assist in performing the adjustments.
Adjusting the Clamping Pressure
The Ultra Lite carriage clamp was designed to make it
easy for the operator to adjust the clamping pressure to
his/her own individual preference using the supplied clamp
pad shims. Hereʼs how:
Note: The Ultra Lite must be attached to a
3
⁄
4
" plywood
base with all six mounting screws (see Fig. 1, page 2)
before adjusting the clamping pressure.
Unlock the carriage clamp and remove the phillips head
screw and washer that caps either end of the clamp pad
slot. See Fig. 43. Your hardware pack for the Ultra Lite
includes (3) .005" x
7
⁄
8
" x 4" clamp pad shims. If you want
to increase the clamping pressure, add one of the shims,
check the clamping pressure and adjust further as
necessary. The shims should be placed to the left of the
1
⁄
8
" thick clamp pad shown in Fig. 43, so that the clamp
always touches the
1
⁄
8
" thick pad, and not the thin shims.
To decrease the clamping pressure, simply remove one of
the existing thin shims. When you are satisfied with the
clamping pressure, replace the phillips head screw and
washer.
Caution: If you have decreased clamping pressure by
removing a shim, make certain that adequate pressure
remains to hold the carriage rigidly in place when clamped
in the fully extended position.
Realigning the Carriage Racks
Unlock the carriage clamp and slide the carriage so you
can access the two phillips head screws that hold the rear
Incra rack to the black mounting track. Tighten the two
screws. Next, slide the carriage forward for access and
loosen the two screws that hold the front Incra rack. The
two racks should be spaced about 2" apart. Adjust the
spacing by sliding the loose rack as necessary. Now
position the carriage in the base so that when the carriage
clamp is pulled up into the locked position the short blue
clamping rack in the base bridges the gap between the
two racks on the carriage. See Fig. 44. Tighten the one
rack mounting screw that you have access to. Finally,
unclamp the carriage clamp and slide the carriage forward
to allow access to the remaining screw and tighten.
ADJUSTMENTS
FIG. 43
Adjusting the clamping pressure
First: Unlock carriage clamp
Second: Remove phillips
head screw and washer
Third: Add or remove shims to
the left of
1
⁄
8
" clamp pad
Shim
FIG. 44
Realigning carriage racks
First: Slide carriage
for access and
tighten screws on
rear rack
Second: Slide carriage for access
and loosen screws on front rack
Third: Position carriage so that short clamping rack
will clamp the ends of both of the longer racks and
lock carriage clamp in place
Fourth: Tighten front screw
Fifth: Slide carriage forward
and tighten remaining screw
2" approx.
1
⁄
8
" clamp pad
15
TROUBLE SHOOTING GUIDE
Symptom
Carriage clamping
pressure is too tight
or too loose.
LEXAN™ scale or
template is difficult
to slide in scale slot.
Racks do not mesh
properly when
engaging the
carriage clamp.
When the jig is
moved to a new
position the carriage
does not glide
easily.
Fence is not square
to the table surface
at all jig positions.
Micro adjusting
knob will not rotate
or is difficult to
rotate.
Micro adjusting
knob rotates but no
movement of the
carriage or fence.
Probable Cause
Carriage clamp not adjusted
properly.
Dirty scale slot.
Sawdust on racks.
Scale mark is not aligned
directly under the hairline
cursor.
Carriage racks are
improperly aligned.
Fence is improperly mounted
to the carriage.
Router table surface not flat.
Fence is improperly mounted
to the carriage.
There are several possible
causes: Jig mounting board
is not flat, table is not flat,
debris between table and
mounting board or between
mounting board and jig.
Carriage clamp is not
“unlocked”.
Jig is micro adjusted to the
end of the forward travel
range.
Jig not in micro adjusting
mode.
Jig micro adjusted beyond
end of backward travel
range.
Solution
Adjust clamping pressure. See page 14.
Remove the scale and clean with paste wax or preferably, Top-Cote
(available from your Incra dealer). CAUTION: DO NOT allow wet
Top-Cote to come into contact with LEXAN scale or templates, or any
other plastic material.
Remove all debris from the racksʼ teeth with a stiff brush, such as a tooth
brush. DO NOT attempt to clean the racks with solvents of any kind as this
may damage them.
After zeroing to a cutter, or after centering when joint making, make sure
the carriage clamp is pulled into the locked position before sliding the
scale or template into place and that the 0" or center cut mark is
positioned directly under the hairline cursor. When you begin your series
of cuts thereafter, always make sure the scale or template mark is aligned
directly under the hairline cursor BEFORE locking the carriage clamp.
Realign the carriage racks as described on page 14.
If the fence is mounted too high or too low on the carriage, it can cause
resistance when moving from one position to another. If this is the case
loosen the screws holding the fence and realign. See Step 3 page 2.
Bumps or dips on the table surface can force the carriage into non-parallel
alignment with the base. Check the table for flatness and correct as
necessary.
If the fence is mounted too high or too low on the carriage, it can change
the angle of the fence relative to the table when it is moved from one
position to another. If this is the case, loosen the screws holding the fence
and realign. See Step 3 page 2.
If you identify any of these, take steps to correct the problem. You can
also use shims to bring the fence into perfect square as described in
Step 5 on page 3.
Carriage clamp must be unlocked, then the clamp handle must be pushed
down and held to place the jig in the micro adjust mode. See Steps 1-4
page 4.
Micro adjust back to mid-range position as indicated by the micro adjust
range scale. Turn knob counter clockwise until “0” on the scale is aligned
with the end of the black bar on the far side of the carriage. See Fig. 8
page 4.
After unlocking the carriage clamp, the clamp handle must be pushed
down and held to place the jig in the micro adjust mode. See Steps 1-4
page 4.
Micro adjust jig forward to mid-range as indicated by the micro adjust range
scale. Turn knob clockwise until the “0” on the scale is aligned with the end
of the black bar on the far side of the carriage, see Fig. 8 page 4.