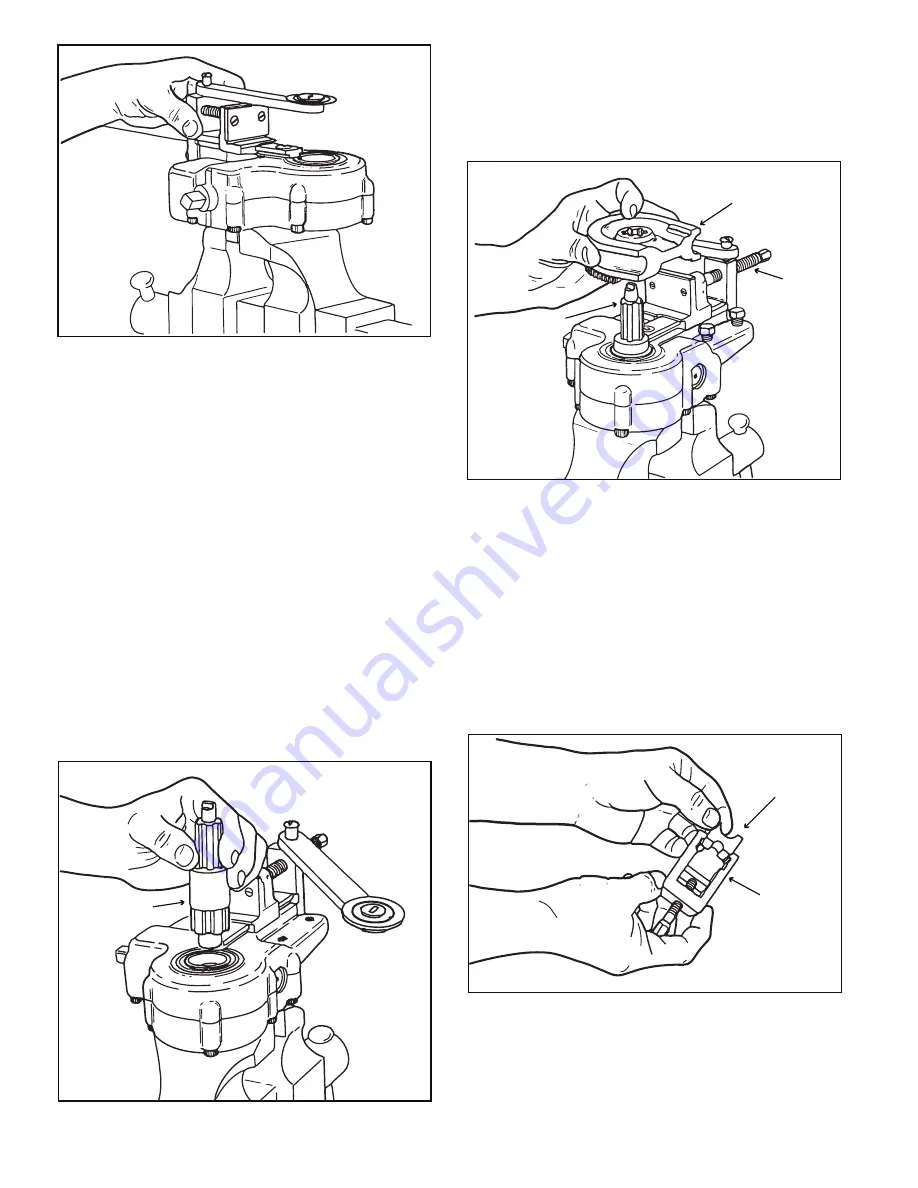
Figure 2. Clamping the Tube Bender Proper in a Vise
11. OPERATION.
12. SETTING UP THE MACHINE. (See Figure 2.)
a. Use a substantial vise with strong, firm-gripping jaws.
Open the jaws wide enough to receive the boss on the
underside of the housing and clamp the tube bender
proper securely between the vise jaws, making certain the
jaws are tight enough to prevent any possibility of the
machine slipping out during actual bending operations.
Considerable force is required on the ratchet handle for
bending 3/4 inch stainless steel tubing, having maximum
wall thickness, and a weak-jawed vise would not hold the
machine.
b. Select the proper size drive shaft to fit the form block
of the required size and insert the drive shaft into the tube
bender proper with the large splines downward. (See
figure 3.) Make certain the drive shaft splines are fully
engaged and that the drive shaft is inserted all the way
into the tube bender so that the lower journal is in the
inner race of the ball bearing.(43, figure 12.)
Figure 3. Installing Drive Shaft in Tube Bender Proper
c. Select the proper size form block and install it on the
drive shaft. (See figure 4.) Rotate the squared countershaft
drive end (37, figure 12) by hand to position the form
block with the starting point of the groove parallel with the
form shoe, when installed.
Figure 4. Placing the Form Block on the
Drive Shaft Spline
NOTE
If the feed screw is turned in too far, the form
shoe slide block will interfere with installation of
the form block.
d. Select the proper size clamp block, turn it so that the
correct groove will be facing outward and slide the clamp
block into the clamp yoke. (See figure 5.)
Figure 5. Installing Clamp Block in Clamp Yoke
e. Place the tube to be bent in the groove of the form
block, at the location of the desired bend, and clamp it
into place with the clamp yoke. (See figure 6.) Make sure
the clamp yoke is in proper position
DRIVE SHAFT
FORM BLOCK
FEED SCREW
DRIVE SHAFT
CLAMP BLOCK
CLAMP YOKE
4