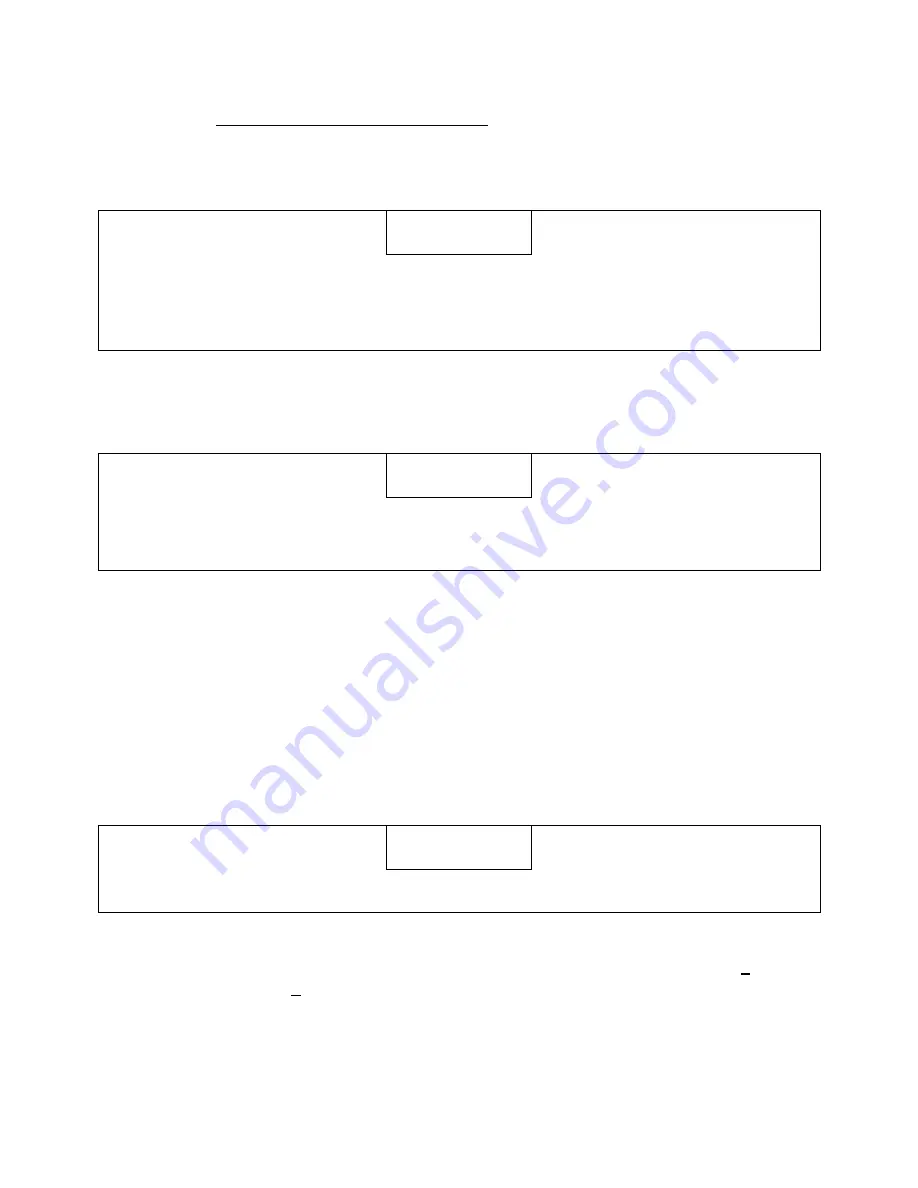
14
Mechanical Seal and Bearing Installation
1. Install O-ring (25) in internal groove of seal sleeve (26)
2. Install rotating assembly (3, Figure 3) onto the sleeve (26), butting the holder (3E, Figure
3) up against the sleeve shoulder.
NOTE
The mechanical seal should be assembled onto the sleeve prior to installing it onto the shaft.
Using a rubber lubricant on O-ring (3B, Figure 3) will aid in the installation. Do not use grease.
Do not tighten mechanical seal setscrews (3F, Figure 3) until the sleeve (26) butts up against the
balance piston (24).
3. Insert stationary seat (1, Figure 3) w/ O-ring (2, Figure 3) into seal seat adapter (63).
Ensure anti-rotation pin in the seal seat adapter is aligned with the slot on the backside
of the stationary seal seat.
NOTE
It is recommended to clean the stationary/rotating seal faces (Fig. 3, 1 and 3A) with alcohol
using a lint-free wipe prior to installing the seal seat adapter. Use caution to avoid damage to
the stationary/rotating seal faces when installing the seal seat adapter onto the shaft sleeve.
4. Install the seal seat adapter (63), along with its associated gasket (65), onto the shaft
sleeve (26).
5. Compress mechanical seal enough to expose spiral ring groove and install spiral ring
(28) in shaft sleeve (26), locking mechanical seal (27) assembly into place.
6. Install assembled shaft sleeve (26) on power rotor (22) shaft until it rests against balance
piston (27). Use caution when installing shaft sleeve (16) to avoid damage to installed O-
ring (25). Tighten setscrews (3F, figure 3).
7. Install inner spacer (29) and outer spacer (30) on power rotor (22) shaft. Align outer
spacer (30) so openings correspond to drain hole and slots in end cover (13).
8. Slide ball bearing (31) on power rotor (22) shaft.
NOTE
Ball bearing (31) can be heated to 200° F for ease of installation on power rotor (22) shaft.
Bearing must be cooled prior to installing the power rotor into the pump.
9. Apply a thin coat of anti-seize to the power rotor threads.
10. Thread nut (32) on power rotor (22) and tighten to a torque specification of 600 + 20 lbs.
ft. (Size 400: 450 + 20 lbs. ft.)To prevent the power rotor from rotating, hold rotor with a
spanner wrench fastened to the rotor’s key slot. An extension bar may be required to
provide sufficient resistance. Remove any burrs from the key slot after nut (32) is
installed.
Содержание CIRCOR GLH8L-400 Series
Страница 11: ...11 Manufactured Tooling Figure 1 Bearing Removal Tool Figure 2 Power Rotor Housing Removal Strongback...
Страница 20: ...20 DRAWINGS...
Страница 21: ...21...