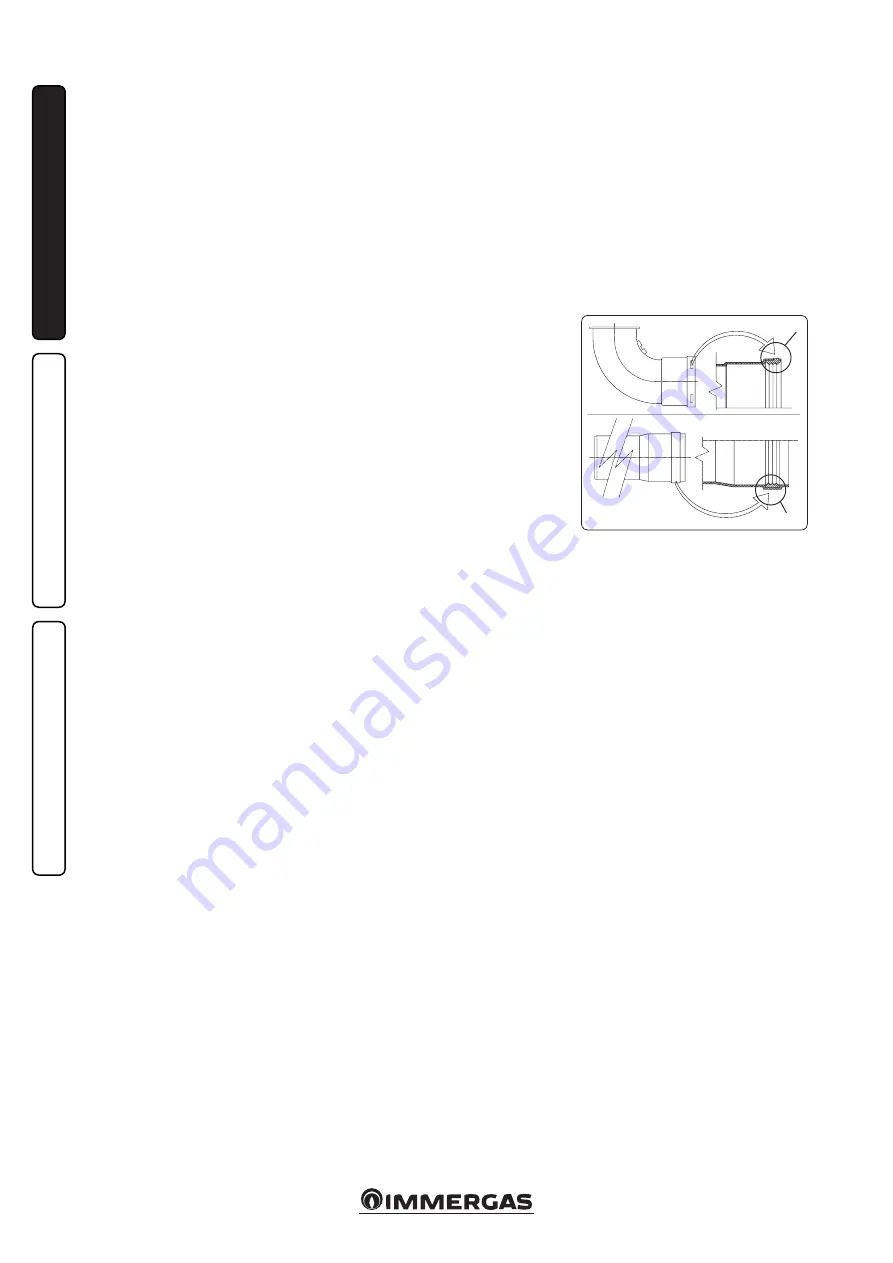
10
(A)
(B)
1-10
INS
TALLER
US
ER
MAINTEN
AN
CE TECHNI
CI
AN
1.12 IMMERGAS FLUE SYSTEMS.
Hunt Heating can supply various solutions for
flueing and air supply.
Attention: the boiler must be installed ex-
clusively with an original Immergas “Green
Range” inspectionable air intake system and
fumes extraction system made of plastic, with
the exception of the C6 configuration, as re-
quired by the regulations in force.
The plastic pipes cannot be installed outdoors,
for lengths longer than 40 cm, without suitable
protection from UV rays and other atmos-
pheric agents.
This system can be identified by an identifi-
cation mark and special distinctive marking
bearing the note: “only for condensing boilers”.
•
Configuration type B, open chamber and fan
assisted.
The boiler leaves the factory with type
“B
23
” configuration.
Air intake takes place directly from the envi-
ronment in which the boiler is installed via
relevant slots made in the back of the boiler
and flue exhaust in the individual flue or to the
outside. Boiler with this type of configuration
are classified as type B
23
(in accordance with
standard EN 297 and relative standards in
force).
With this configuration:
- air intake takes place directly from the room
in which the appliance is installed;
- the flue exhaust must be connected to its own
individual flue or channelled directly into the
external atmosphere.
- Type B open chamber boilers must not be
installed in places where commercial, artisan
or industrial activities take place, which use
products that may develop volatile vapours
or substances (e.g. acid vapours, glues, paints,
solvents, combustibles, etc.), as well as dusts
(e.g. dust deriving from the working of wood,
coal fines, cement, etc.), which may be harm-
ful for the components of the appliance and
jeopardise operation.
•
Type C configuration, sealed chamber and
fan assisted.
The boiler leaves the factory with
"B
23
" configuration, to change the configuration
of the boiler to type "C" (sealed chamber and
fan assisted), disassemble the 80 Ø adapter, the
bracket and the gasket present on the boiler
cover and install the designated flue.
N.B.:
the 80 Ø adapter and gasket will be dis-
carded.
• Coupling extension pipes and concentric
elbows. To install push-fitting extensions with
other elements of the flue, proceed as follows:
Install the concentric pipe or elbow with the
male side (smooth) on the female section
(with lip seal) to the end stop on the previously
installed element in order to ensure sealing
efficiency of the coupling.
Attention:
if the exhaust terminal and/or
concentric extension pipe needs shortening,
consider that the internal duct must always
protrude by 5 mm with respect to the external
duct.
•
N.B.:
for safety purposes, do not obstruct the
boiler intake-exhaust terminal, even temporar-
ily.
•
N.B.:
when installing horizontal pipes, a min-
imum inclination of 3% must be maintained
and a section clamp with pin must be installed
every 1.5 metres.
•
Maximum extension.
Each individual compo-
nent has a resistance corresponding to a certain
length in metres of pipe with the same diameter
(par. 1.13). With installations that involve using
various types of parts, deduct the length of
the added part from the maximum admissible
length of the kit.
Example: if you need to add a 90° bend to
a concentric system 125 Ø you will need to
deduct 1.9 m from the maximum admissible
length.
•
Positioning of the gaskets (black) for “green
range” flue extraction systems.
Position the
gasket correctly (for bends and extensions)
(Fig. 1-10):
- gasket (A) with notches, to use for bends;
- gasket (B) without notches, to use for exten-
sions;
N.B.:
if component lubrication (already carried
out by the manufacturer) is not sufficient, re-
move the residual lubricant using a dry cloth,
then to ease fitting coat the parts with talc.