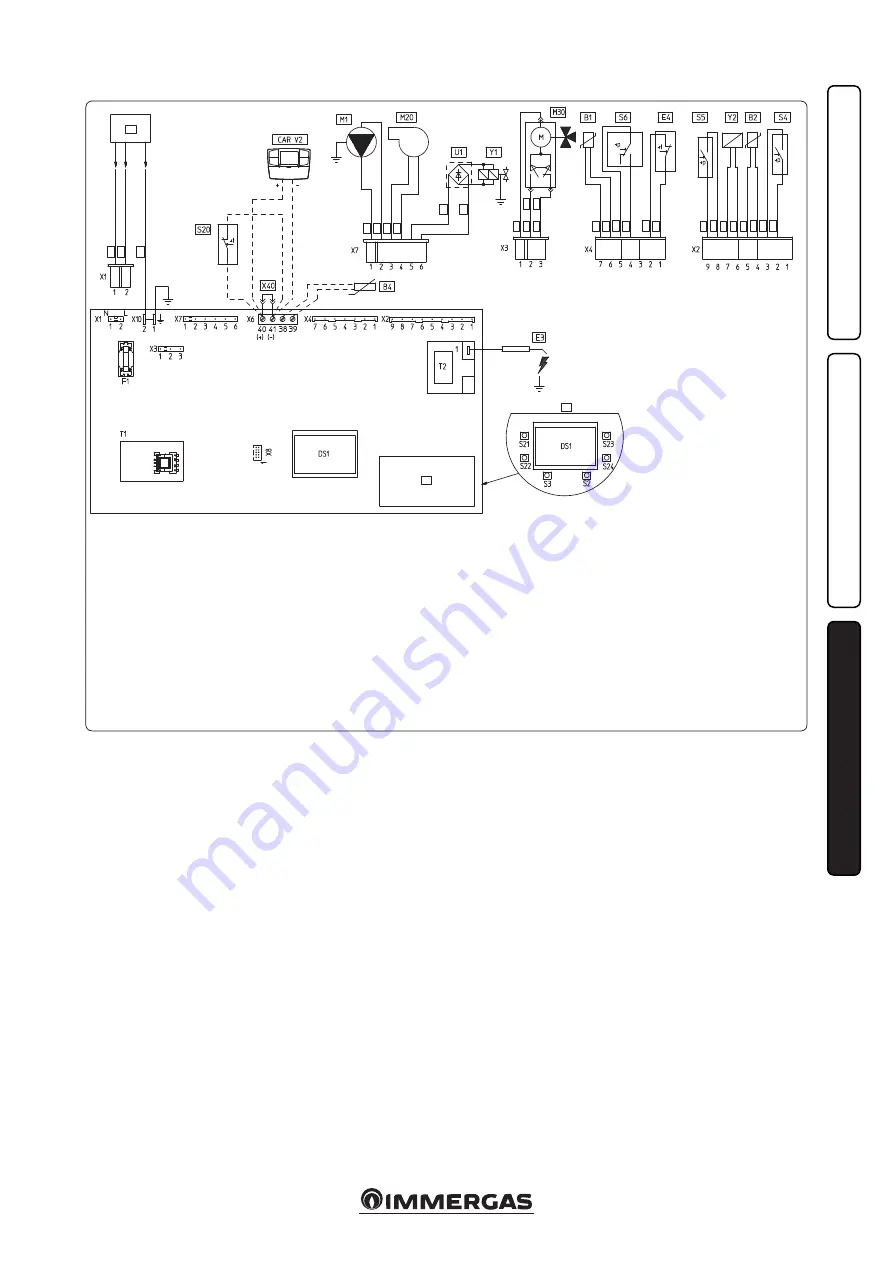
23
5
1
2
6
5
4
3
4
4
5
11
7
7
7
12
12
7
13
13
11
4
5
5
7
4
10
10
10 10
9
8
3-2
INS
TALLER
US
ER
MAINTEN
AN
CE TECHNI
CI
AN
3.2 WIRING DIAGRAM.
Key:
B1 - Flow probe
B2 - Domestic hot water probe
B4 - External probe
CAR
V2
- Comando Amico Remoto remote control Version
2 (optional)
DS1 - Display
E3 - Ignition and detection electrodes
E4 - Safety thermostat
F1 - Phase fuse
M1 - Boiler pump
M20 - Fan
M30 - Three-way valve
S2 - Selector switch functioning
S3 - Reset block key
S4 - Domestic hot water flow switch
S5 - System pressure switch
S6 - Flue pressure switch
S20 - Room thermostat (optional)
S21 - Key to increase
DHW temperature
S22 - Key to decrease
DHW temperature
S23 - Key to increase
central heating temperature
S24 - Key to decrease
central heating temperature
T1 - Low voltage feeder
T2 - Ignition transformer
U1 - Rectifier inside the gas valve
connector (Only available on
Honeywell gas valves)
X40 - Room thermostat jumper
Y1 - Gas valve
Y2 - Gas valve modulator
1 - User interface
2 - N.B.: The user interface is on
the welding side of the boiler
board
3 - 230 Vac 50Hz power supply
4 - Blue
5 - Brown
6 - Yellow/Green
7 - Black
8 - Domestic hot water
9 - Central heating
10 - Grey
11 - White
12 - Red
13 - Green
The boiler is designed for application of a room
thermostat (S20), an On/Off room chrono-
thermostat, a program timer or a Comando
Amico Remoto remote control
V2
(CAR
V2
).
Connect to clamps 40 - 41 eliminating the jumper
X40, paying attention not to invert the polarity if
the CAR
V2
is installed.
The connector X8 is used for the connection
of the Virgilio Palmtop in the microprocessor
software updating operation.
3.3 TROUBLESHOOTING
N.B.:
maintenance interventions must be carried
out by a qualified technician (e.g. Immergas
After-Sales Technical Assistance Service).
- Smell of gas. Caused by leakage from gas circuit
pipelines. Check sealing efficiency of gas intake
circuit.
- The fan works but ignition discharge does not
occur on the burner ramp. The fan may start
but the safety air pressure switch does not
switch the contact over. Make sure:
1) the intake-exhaust duct is not too long (over
allowed length).
2) the intake-exhaust pipe is not partially
blocked (on the exhaust or intake side).
3) the diaphragm of the fume exhaust is
adequate for the length of the intake-exhaust
duct.
4) that the sealed chamber is kept in good
conditions.
5) the fan power supply voltage is not less than
196 V.
- Irregular combustion (red or yellow flame).
Can be caused by: dirty burner, incorrect
combustion parameters, intake - exhaust
terminal not correctly installed. Clean
the above components and ensure correct
installation of the terminal.
- Frequent activation of the temperature
overload thermostat. It can depend on reduced
water pressure in the boiler, little circulation
in the heating system, the blocked pump or
an anomaly of the boiler P.C.B. Check on the
manometer that the system pressure is within
established limits. Check that radiator valves
are not all closed.
- Presence of air in the system. Check opening of
the special air vent valve cap (Fig. 1-30). Make
sure the system pressure and expansion vessel
factory-set pressure values are within the set
limits; the factory-set value for the expansion
vessel must be 1.0 bar, and system pressure
between 1 and 1.2 bar.
- Ignition block see par. 2.5 and 1.4 (electric
connection).
Содержание Mini Eolo 24 3 E
Страница 1: ...MINI EOLO 24 3E Instruction and warning book IE 1 038773ENG ...
Страница 2: ......
Страница 28: ...28 3 5 4 4 5 6 6 d d c INSTALLER USER MAINTENANCE TECHNICIAN ...
Страница 33: ......
Страница 34: ......
Страница 35: ......