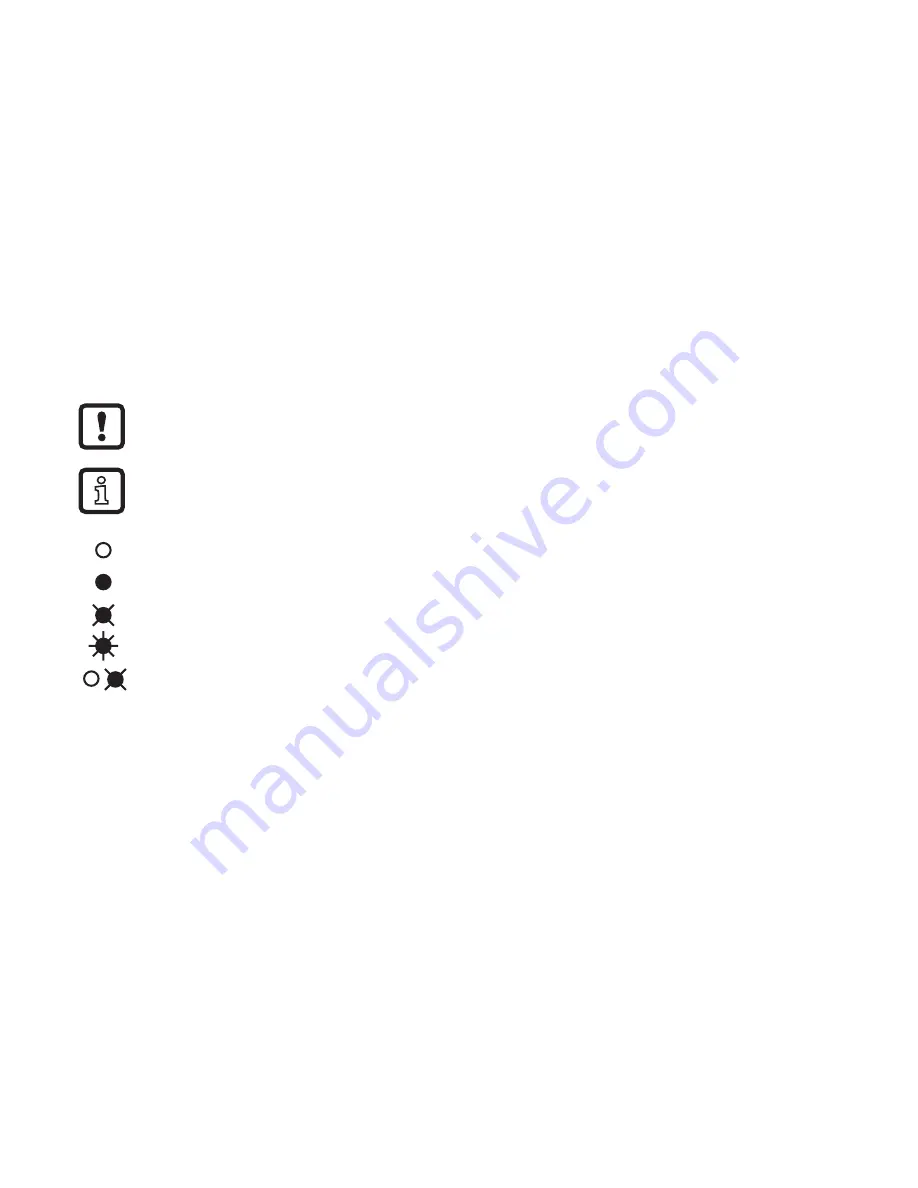
4
1 Preliminary note
The instructions are part of the unit. They are intended for authorised persons
according to the EMC and Low Voltage Directives and safety regulations.
The instructions contain information about the correct handling of the product.
Read the instructions before use to familiarise yourself with operating conditions,
installation and operation.
Follow the safety instructions.
1.1 Symbols used
►
Instructions
>
Reaction, result
→
Cross-reference
Important note
Non-compliance can result in malfunction or interference.
Information
Supplementary note.
LED off
LED on
LED flashes
LED flashes quickly
2 LEDs flash alternately
Содержание DA102S
Страница 13: ...13 UK 6 3 2 Example cam disc 5 x D D D 3 x D Mechanical requirements ...
Страница 21: ...21 UK 11 Technical data ...
Страница 22: ...22 ...