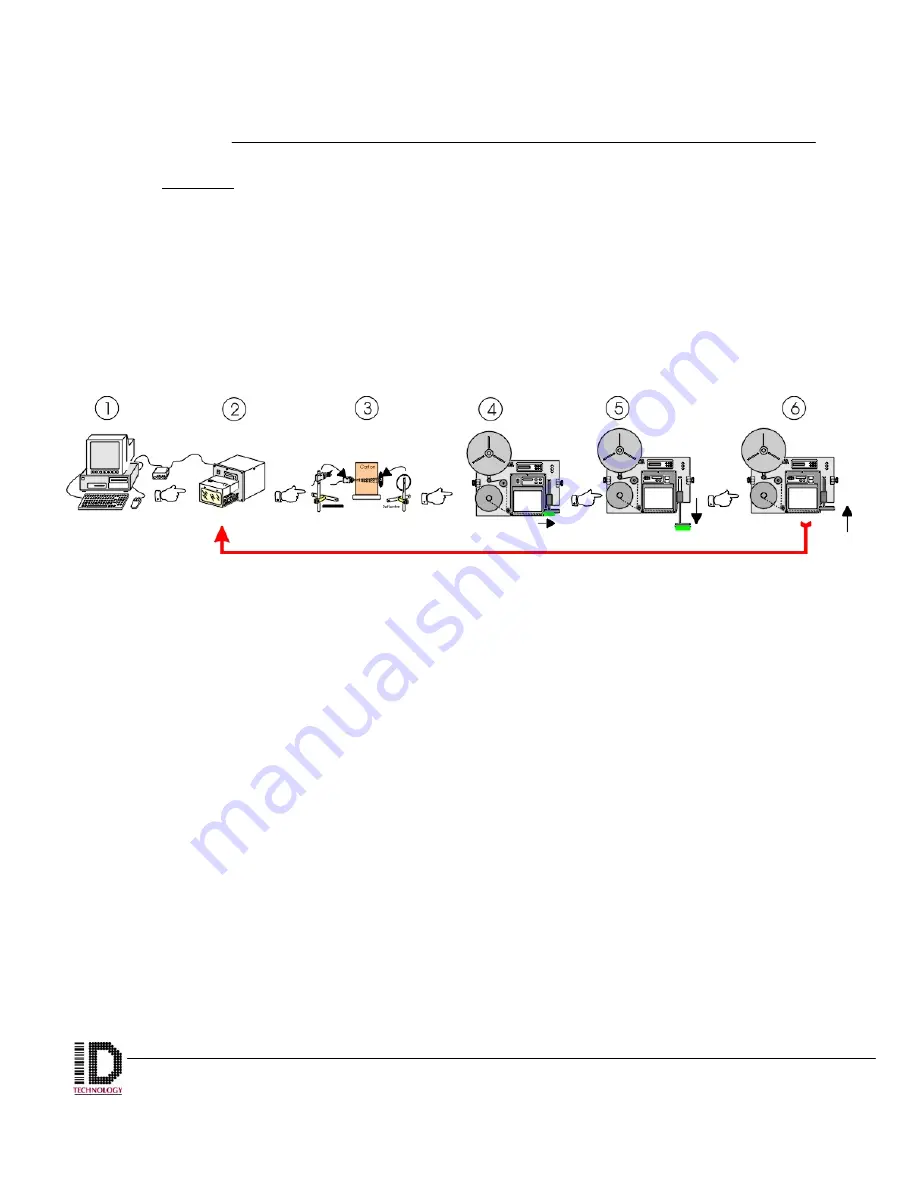
Model 250
Printer Applicator
Operators/Technical Manual Section Five
Section 5 Page 7 of 18
2. Reverse - If you select the Reverse mode under the Print Sequence menu: Data is
downloaded to print engine buffer and resides there until required. When the
product detect photo-eye senses the product, the print engine is triggered and a
label is then printed and dispensed. As soon as the label is completely dispensed
onto the tamp pad or blow on grid the application is accomplished (tamp, blow -on,
etc…) At the end of the application cycle the printer awaits another trigger from the
photocell to start the process over. This continues until the quantity of labels
(designated by the operator) runs out. As the label is dispensed from the print
engine, the air assist will turn on. At the end of the dispense cycle, the air assist
will de-energize. While the dispense cycle is on the rewind cycle is on.
Figure 5-2
Reverse Print Sequence
1. Operator generates label and designates quantity.
2. Operator sends label to print engine’s buffer.
3. Product detector senses product and triggers print engine to print and
dispense a label.
4. Label is printed and dispensed.
5. Cylinder extends (or blow on pneumatics are initiated) and Label is
applied.
6. Cylinder retracts (or blow on pneumatics is de-energized)
7. Engine awaits another trigger from the product detector.
Cycle starts back at Print engine until designated quantity is completed.
Содержание 250
Страница 1: ...250 Print and Apply Operator Technical Manual Model...
Страница 33: ...Model 250 Printer Applicator Operators Technical Manual Section Two Section 2 Page 14 of 14 Operator Notes...
Страница 52: ...Model 250 Printer Applicator Operators Technical Manual Section Three Section 3 Page 19 of 19 Operator Notes...
Страница 69: ...Model 250 Printer Applicator Operators Technical Manual Section 3B Section 3B Page 9 of 9...
Страница 93: ...Model 250 Printer Applicator Operators Technical Manual Section Five Section 5 Page 18 of 18 Operator Notes...
Страница 109: ...Model 250 Printer Applicator Operators Technical Manual Section Six Section 6 Page 16 of 20 Timing Cycles...
Страница 110: ...Model 250 Printer Applicator Operators Technical Manual Section Six Section 6 Page 17 of 20...
Страница 111: ...Model 250 Printer Applicator Operators Technical Manual Section Six Section 6 Page 18 of 20...
Страница 112: ...Model 250 Printer Applicator Operators Technical Manual Section Six Section 6 Page 19 of 20...
Страница 113: ...Model 250 Printer Applicator Operators Technical Manual Section Six Section 6 Page 20 of 20 Operator Notes...
Страница 126: ...ITEM QTY ITEM QTY ITEM QTY ITEM QTY PARTNO DESCRIPTION Accessories 1 1 62280 TAMPJETKITASSEMBLY 1 1 62281 2 WAYD O VALVE...
Страница 127: ...2051 FRANKLIN DR FORT WORTH TX 76106 250 PRECISION TILT...