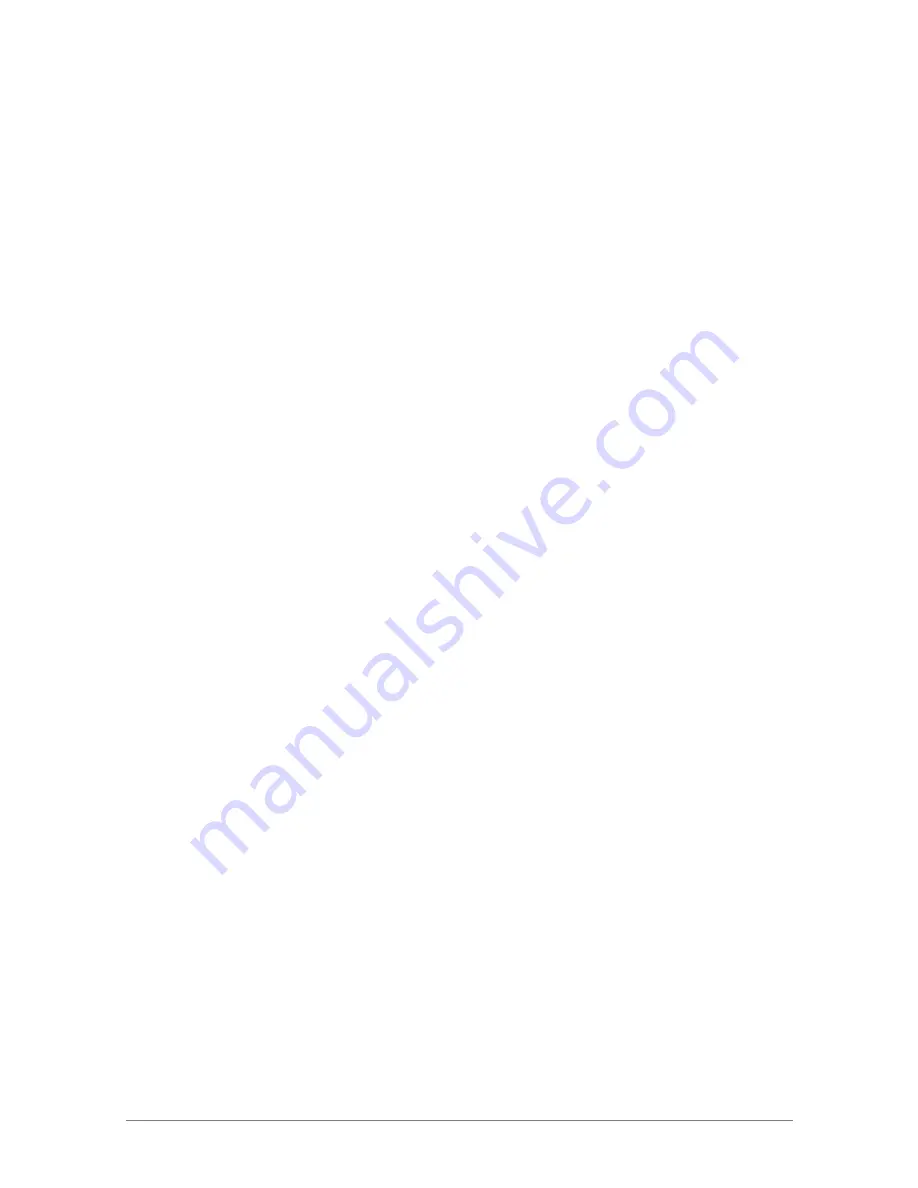
© ICSPI Corp. 2007-2021
nGauge AFM User Manual 2.0
34
value is 500 µs. Increasing to 1000 µs or more may improve the image quality, but the scan will
take longer to complete.
The proportional and integral (PI) gain settings can be reduced for slower scans (high dwell
time) and increased for faster scans (low dwell time). More information on PI gain is available in
5.8.3.
The
Time spent at each point
can be safely changed throughout the scan.
5.8.2.
Setpoint
The
Setpoint
is the tip oscillation amplitude that the controller will try to maintain as the tip
scans over the sample surface. It can be thought of as the amount of force that the tip exerts as
it taps the surface.
The setpoint is set to 50% of the drive amplitude value by default. For example, if the peak of
the amplitude curve on the sweep page is 3 V, the default setpoint will be 1.5 V.
A lower setpoint exerts more force on the sample. A lower setpoint can often give better results
but is also more likely to damage the tip or sample, and when the setpoint gets too low the
imaging performance may suffer. A low setpoint may be 25% of the drive amplitude. For
example, if the drive amplitude is 3 V, setting the setpoint to 0.75 V would be 25% of the drive
amplitude.
A high setpoint exerts less force on the sample. A high setpoint is recommended when scanning
materials that may move around, such as particles that are not strongly affixed to the surface
substrate. A high setpoint may be 75% of the drive amplitude. For example, if the drive
amplitude is 3 V, setting the setpoint to 2.25 V would be 75% of the drive amplitude.
Because the setpoint changes the mechanical interaction between the tip and the sample,
changing the setpoint affects the phase images. Changing the setpoint may lead to more or less
contrast in phase images.
The setpoint can be changed before clicking on ‘Approach’. To change the setpoint after the tip
is engaged, you must click on disengage first.
5.8.3.
Proportional and Integral Control
The
Proportional
and
Integral (PI)
control in the advanced controls section is used to adjust
the response of the controller and can be tuned to give the best sample tracking performance.
The PI controller measures the tip oscillation amplitude and subtracts this value from the
setpoint to give an error term. The error term is multiplied by the Proportional (P) coefficient and
the Integral (I) coefficient to generate a response in the Fine Z. These terms are also known as
the proportional gain and integral gain.
If the P and I gain are too low, the controller response will be slow, and the tip will not track the
sample topography very well. If the P and I coefficients are too high, the controller may oscillate,
and the image will be noisy. The default values are 5 for P and 5000 for I.