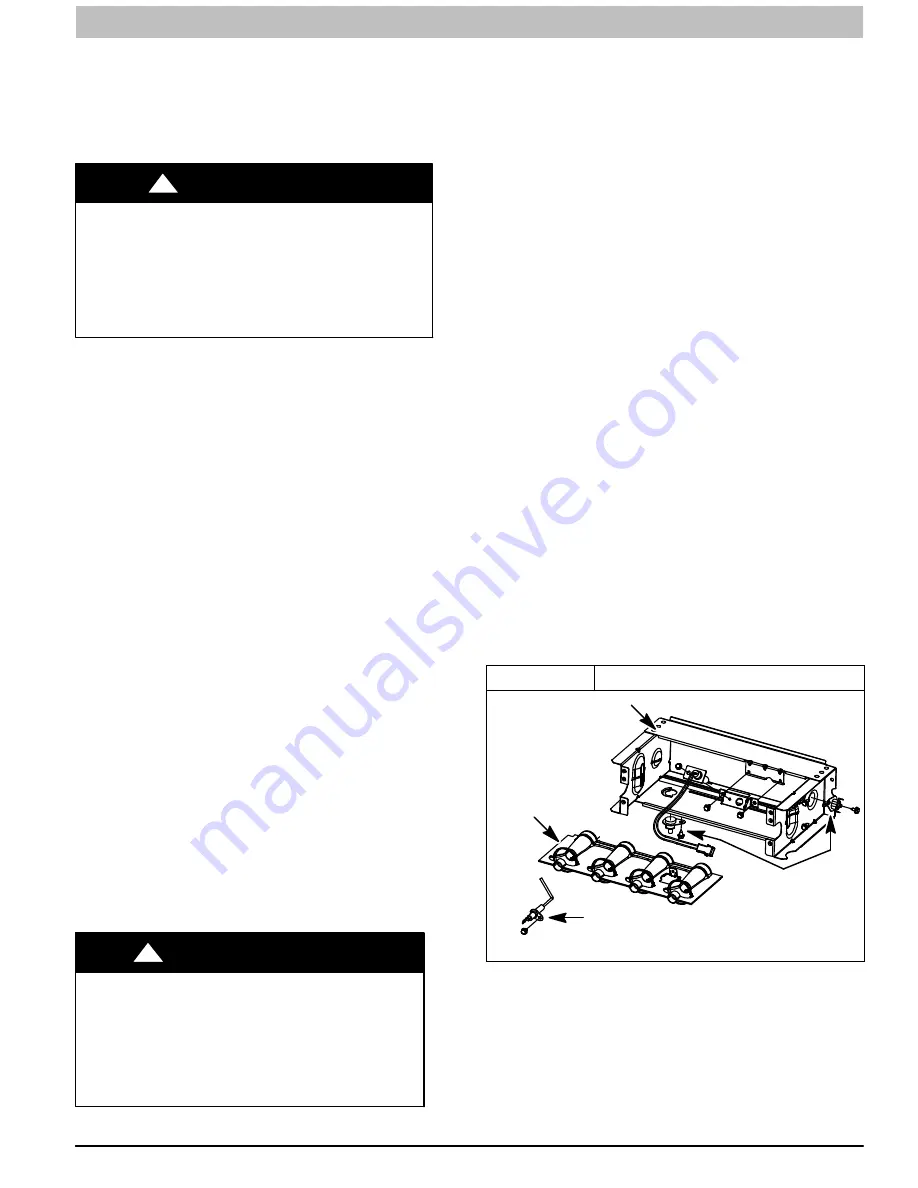
SERVICE AND TECHNICAL SUPPORT MANUAL
Gas Furnace: N9MSE
Specifications subject to change without notice.
440 04 4401 03
17
14. Reinstall 2 screws securing blower assembly to blower
deck.
15. Reconnect blower leads to furnace control. Refer to
furnace wiring diagram, and connect thermostat leads if
previously disconnected.
NOTE
: Be sure to attach ground wire and reconnect blower
harness plugs to blower motor.
ELECTRICAL OPERATION HAZARD
Failure to follow this warning could result in personal
injury or death.
Blower door switch opens 115
−
V power to control. No
component operation can occur unless switch is closed.
Caution must be taken when manually closing this
switch for service purposes.
!
WARNING
16. Downflow or horizontal furnaces with vent pipe through
furnace only:
a. Install and connect short piece of vent pipe inside
furnace to existing vent.
b. Connect vent connector to vent elbow.
17. Turn on electrical supply. Manually close blower door
switch. Use a piece of tape to hold switch closed. Check
for proper rotation and speed changes between heating
and cooling by jumpering R to G and R to Y on furnace
control thermostat terminals. If outdoor temperature is
below 70
_
F (21
_
C), turn off circuit breaker to outdoor unit
before running furnace in the cooling cycle. Turn outdoor
circuit breaker on after completing cooling cycle. (See
Figure 4
)
NOTE
: If R
−
W/W1 thermostat terminals are jumpered at the
time blower door switch is closed, blower will run for 90 sec
before beginning a heating cycle.
a. Perform component self
−
test as shown at the bottom
of the SERVICE label, located on the blower door.
b. Verify blower is rotating in the correct direction
18. If furnace is operating properly, RELEASE BLOWER
DOOR SWITCH. Remove any jumpers or reconnect any
disconnected thermostat leads. Replace blower door.
19. Turn on gas supply and cycle furnace through one
complete heating cycle. Verify the furnace temperature
rise as shown in Adjustments Section. Adjust
temperature rise as shown in Adjustments Section.
Cleaning Burners and Flame Sensor
The following items must be performed by a qualified service
technician. If the burners develop an accumulation of light dirt
or dust, they may be cleaned by using the following procedure:
NOTE
: Use a back-up wrench on the gas valve to prevent the
valve from rotating on the manifold or damaging the mounting
to the burner assembly.
ELECTRICAL SHOCK AND FIRE HAZARD
Failure to follow this warning could result in personal
injury, death, and/or property damage.
Turn off the gas and electrical supplies to the furnace
and install lockout tag before performing any
maintenance or service. Follow the operating
instructions on the label attached to the furnace.
!
WARNING
Refer to
Figure 9
.
1. Disconnect power at external disconnect, fuse or circuit
breaker.
2. Turn off gas at external shut-off or gas meter.
3. Remove control door and set aside.
4. Turn electric switch on gas valve to OFF.
5. Disconnect the gas pipe from gas valve and remove pipe
from the furnace casing.
6. Remove individual wires from terminals on gas valve.
7. Disconnect Hot Surface Igniter (HSI) wires from HSI.
8. Disconnect Flame Sensor wire from Flame Sensor.
9. Support the manifold and remove the 4 screws that
secure the manifold assembly to the burner assembly
and set aside. Note the location of the green/yellow wire
and ground terminal.
10. Inspect the orifices in the manifold assembly for
blockages or obstructions. Remove orifice and clean or
replace orifice.
11. Remove the four screws that attach the top plate of the
casing to the furnace.
12. Raise top plate up slightly and prop it up with a small
piece of wood or folded cardboard.
13. Support the burner assembly and remove the screws
that attach the burner assembly to the heat exchanger
cell panel.
14. Remove wires from both rollout switches.
15. Slide one
−
piece burner out of slots on sides of burner
assembly.
16. Remove the flame sensor from the burner assembly.
17. (Optional) Remove the Hot Surface Igniter (HSI) and
bracket from the burner assembly.
18. Check igniter resistance. Nominal resistance is 40 to 70
ohms at room temperature and is stable over the life of
the igniter.
19. Clean burner with a brush and a vacuum.
20. Clean the flame sensor with fine steel wool (0000 grade).
Do not use sand paper or emery cloth.
Figure 9
Burner Assembly
B
URNER
A
SSY
F
LAME
S
ENSOR
(
B
ELOW
B
URNER)
F
LAME
R
OLL
−
OUT
S
WITCH
B
URNER
S
UPT.
A
SSY
L11F064
Representative drawing only, some models may vary in appearance.
To reinstall burner assembly:
1. Install the Hot Surface Igniter (HSI) and bracket in burner
assembly.
2. Install flame sensor on burner.
3. Align the edges of the one-piece burner with the slots in
the burner assembly and slide the burners forward until
they are fully seated in the burner assembly.
4. Align the orifices in the manifold assembly with the
support rings on the end of the burner.