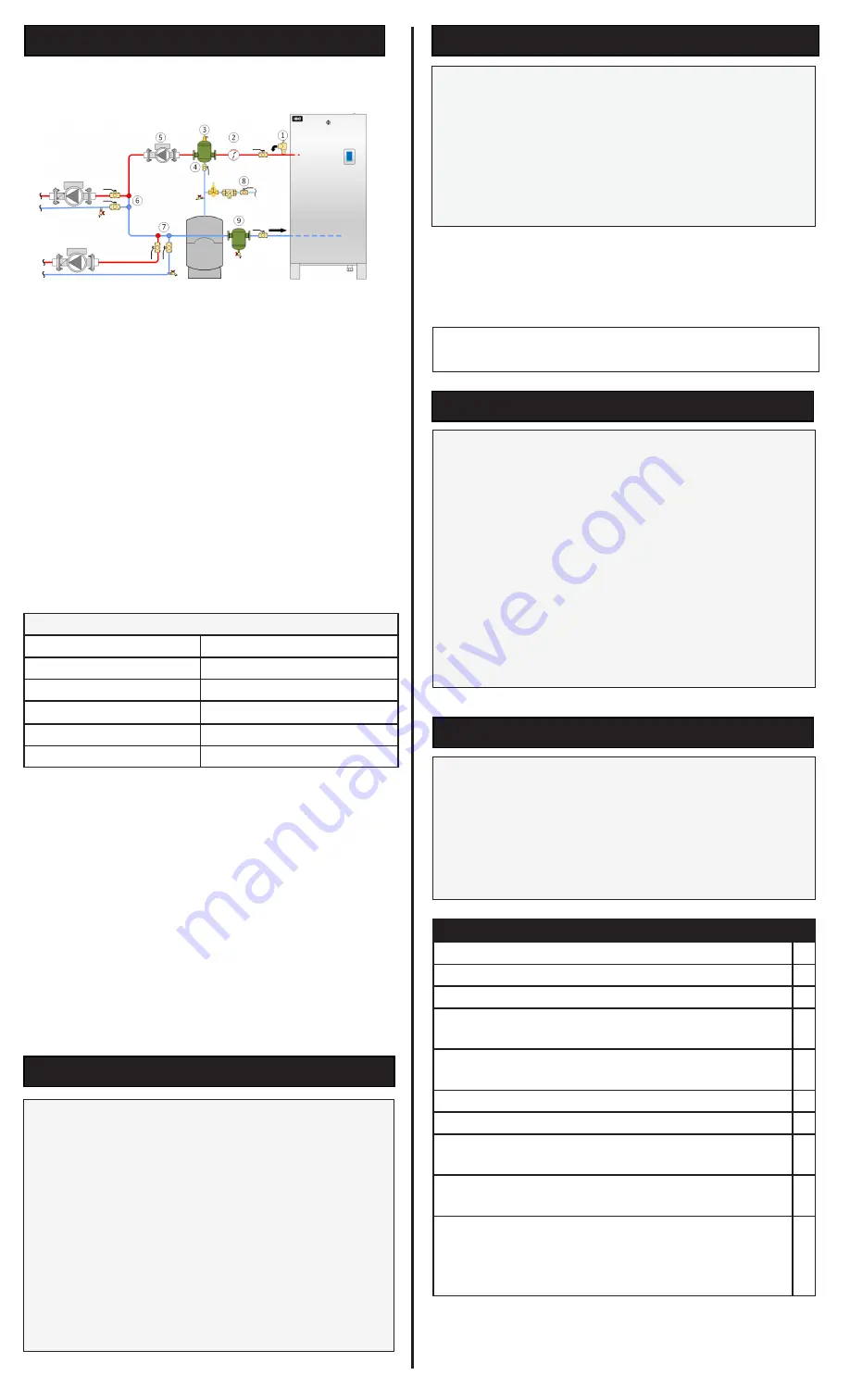
We recommend that you always use a primary/secondary piping
configuration (see below for a basic configuration).
In the case of hard water, use distilled or purified water. Glycol
systems require the use of propylene glycol. For large volume
systems, the optimum hardness is ≤2 grains.
Water Chemistry Allowable Limits
Acidity pH
6.6 - 8.5
Chloride
< 125 mg/l
Iron
< 0.5 mg/l
Copper
<0.1 mg/l
Conductivity
<
400μS/cm (at 25°C)
Water Hardness
<
7 Grains
•
Place an air separator at the highest point. These
must be
installed above each boiler
.
•
Install the pressure relief valve in a vertical position. Do not
use an isolation valve between the boiler and relief valve.
•
Support all piping with appropriate piping brackets.
•
Plumb an appropriately sized expansion tank and make up
the water station into a fitting on the suction side of the
circulator.
•
Size boiler piping and pumps for the BTU output of the boiler.
For non-oxygen barrier piping systems, use a dirt separator and/
or a side stream filter. Ensure that the system is free of iron
components, and treat with an inhibitor.
Electrical
(Section 3.10
)
1. Connect the boiler to a dedicated (max.)15 Amp breaker.
2. Wire the AC to the black and white wires labeled in the
Field wiring box.
3. Ensure that the boiler is properly bonded (grounded).
4. Refer to the “Wiring Diagrams” section in the
Installation
and Operating Instructions
manual (Fig 42) for more
information.
5. Wires labelled “Boiler Pump:” Wire power for the boiler
pump to the black wire, and the boiler pump “L” (hot)
connection to the yellow wire.
6. Wire the respective load pumps into the TB1 Terminal; for
example, PV 1, 2, 3, 4.
Electrical
continued
(Section 3.10
)
Water Piping
(Section 3.8)
1. Wire thermostats or end switch dry contacts to Therm 24
Vac, and then connect the other wire to Therm 1, 2, 3, 4
corresponding to the load pump PV1, 2, 3, 4.
2. For a DHW load, wire either an Aquastat to the appropriate
Therm. connection or a 10K Ω type II/B curve thermister to
the DHW Sensor connection.
The boiler requires proper grounding, which conforms to all
electrical codes, ensuring proper flame rectification.
•
For multiple-boiler setups, use a secondary loop sensor wired to
the Master boiler.
•
For zone valves or external peripherals, use external
transformers.
Note:
If a load is defined as Reset Heating, the outdoor sensor
must be used for proper operation.
Express Setup
1. On theV-10 Touchscreen controller, tap the
Home
(Standby)
screen>
Main Menu>Express Setup
.
2. Do the following:
a. Tap the
Enter Design Outdoor Temperature
box, and
enter a value.
b. Tap
Set Clock
to set the time and date.
c. Tap
Save
.
3. Select a load and then select the load type.
4. Accept the defaults, or change any of the settings.
5. You can find more substantial settings in "Installer Settings".
6. Tap the
Save
button.
Manual Pump Purge
After the system is pressurized and you have defined loads,
perform a manual pump purge to ensure air is purged.
On the touchscreen controller, go to
Main Menu
>
Installer
Settings
>
System Settings
>
Site Settings
>Set
Manual Pump
Purge to
"
ON
">
OK
>
Save.
The manual pump purge runs until it is turned off, or when there
is a call for heat.
Checklist
Treated water or Polypropylene glycol mixture in the pipes.
□
Boiler system is pressured and flushed ≥ 8 psi.
□
All gas connections soap-tested for leaks and now leak free.
□
Voltage supply to the boiler tested for voltage (nominal 120
Vac), polarity, and properly grounded.
□
The boiler requires a dry set of contacts in the Therm
connections.
□
Boiler power turned on.
□
Reset low gas pressure switch
□
Use the “Express Setup” in the touchscreen controller to set
up the required loads. See above for instructions.
□
Steps followed in the “6.3 Commissioning” section of the
Installation and Operating Instructions
manual.
□
Completed the Installation & Commissioning Report in the
Installation and Operating Instructions manual - Combustion
Readings recorded.
CO
2
_________
_
% O
2
________ % CO _______ppm
□
1. Pressure relief valve (shipped with boiler): no isolation valve
permitted between boiler and relief valve
2. Tridicator (shipped with boiler)
3. Microbubble air eliminators
4. Expansion tank connection
5. Boiler Pump
6. Closely-spaced tees to/from Load 1
7. Closely spaced tees to/from Load 2
8. Fill station
9. Dirt seperator recommended