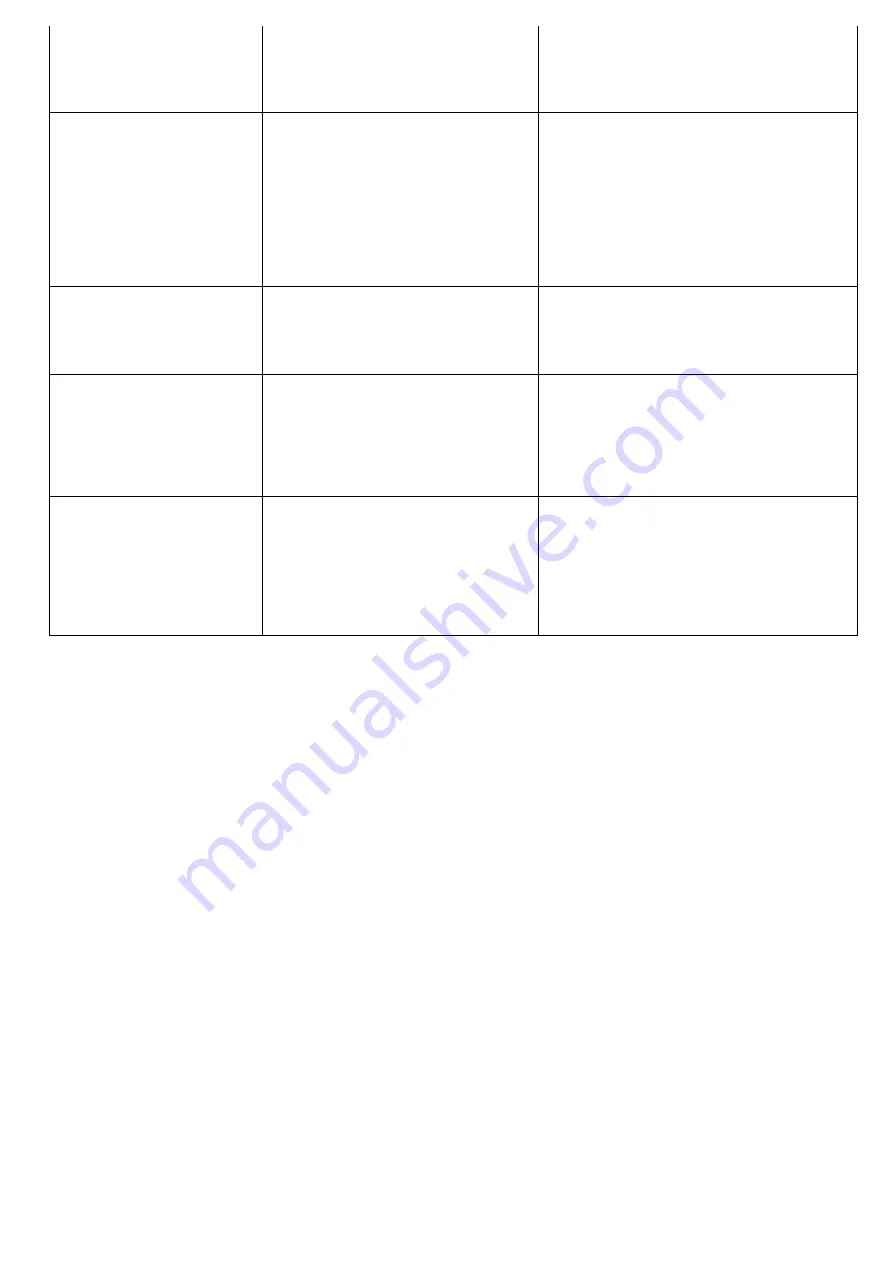
AS1375-940
Page
30
Disinfection of Water Conditioners
The construction materials of the water conditioner
system do not support bacterial growth or
contaminated the water supply. However, we
recommend that the conditioners be disinfected after
installation and before the conditioners are used to
treat potable water. In addition, a conditioner can
become fouled with organic matter during normal
usage or with bacteria from the water supply. Periodic
disinfection is recommended for all conditioners. Use
one of the following methods of disinfection based on
operating conditions, style of conditioner, type of ion
exchange, and disinfectant available.
Sodium Hypochlorite
Sodium Hypochlorite, 5.25% solutions, can be used
with polystyrene resin, synthetic gel zeolite,
greensand, and bentonites and are available under
trade names such as Chlorox, Linco, Bo Peep, White
Sail and Eagle Brand Bleach. Adjust the dosage if
stronger commercial solutions are used.
The recommended dosage for 5.25% solution is:
•
Polystyrene resin: 1.2 fluid ounces per cubic foot.
•
Non-resinous exchangers: 0.8 fluid ounces per
cubic foot.
Complete the following steps to disinfect the
conditioner: Add the sodium hypochlorite solution to
the brine well of the brine tank. Make sure that the
brine tank has water init so the solution is carried into
the conditioner. Proceed with normal regeneration.
Refer to the
Manual Regeneration
section for this
manual.
Calcium Hypochlorite
Calcium Hypochlorite, 70% available chlorine, is
available in several forms including tablets and
granules. These solid materials can be used directly
without dissolving before application.
The recommended dosage for Calcium Hypochlorite
is two grains (approx. 0.1 ounce) per cubic foot.
Complete the following steps to disinfect the
conditioner: Add the Calcium Hypochlorite to the
brine well of the brine tank. Make sure that he brine
tank has water in it so the solution is carried into the
conditioner. Proceed with normal regeneration. Refer
to the
Manual Regeneration
section of this manual.
6. Intermittent or irregular
brine draw .
a. Low water pressure.
b. Defective Injector.
!
a. Water pressure must be 20 psi
Minimum.
b. Replace both injector and injector cap.
7. No conditioned water
After regeneration.
a. Unit did not regenerate
b. No salt in brine tank
c. Plugged injector.
d. Air check prematurely closed.
a. Check for power.
b. Add salt to brine tank.
c. Remove injector and injector screen,
Flush with water.
d. Put control momentarily into brine refill
To free air check. Replace or repair air
check if needed. Refer to brine line
connection.
8. Control backwashes at
Excessively low or high
Rate.
a. Incorrect back wash controller.
!
b. Foreign matter effecting controller
Operation.
!
a. Replace with correct size controller.
b. Remove and clean controller seat and
Ball.
9. Flowing or dripping
Water at drain or brine
Line after regeneration.
a. Drain valve (5 or 6) or brine valve
(1) held open by foreign matter or
particle.
b. Weak valve stem return spring on
Top plate.
a. Manually operate valve stem to flush
Away obstruction.
b. Replace spring.
10. Hard water leakage
During service.
a. Improper regeneration.
b. Leaking external bypass valve.
c. O-ring around riser tube
Damaged.
d. Leaking past bypass valve disc.
a. Repeat regeneration making certain
Correct salt usage is used.
b. Replace o-ring.
c. Replace o-ring.
d. Replace defective part.
Содержание AS1375-940
Страница 20: ...AS1375 940 Page 20 Control Valving Identification Valve Disc Operation ...
Страница 21: ...AS1375 940 Page 21 Flow Diagrams ...
Страница 22: ...AS1375 940 Page 22 ...
Страница 24: ...AS1375 940 Page 24 ...
Страница 25: ...AS1375 940 Page 25 Valve Body and Tank Adaptor Module ...
Страница 29: ...AS1375 940 Page 29 ...