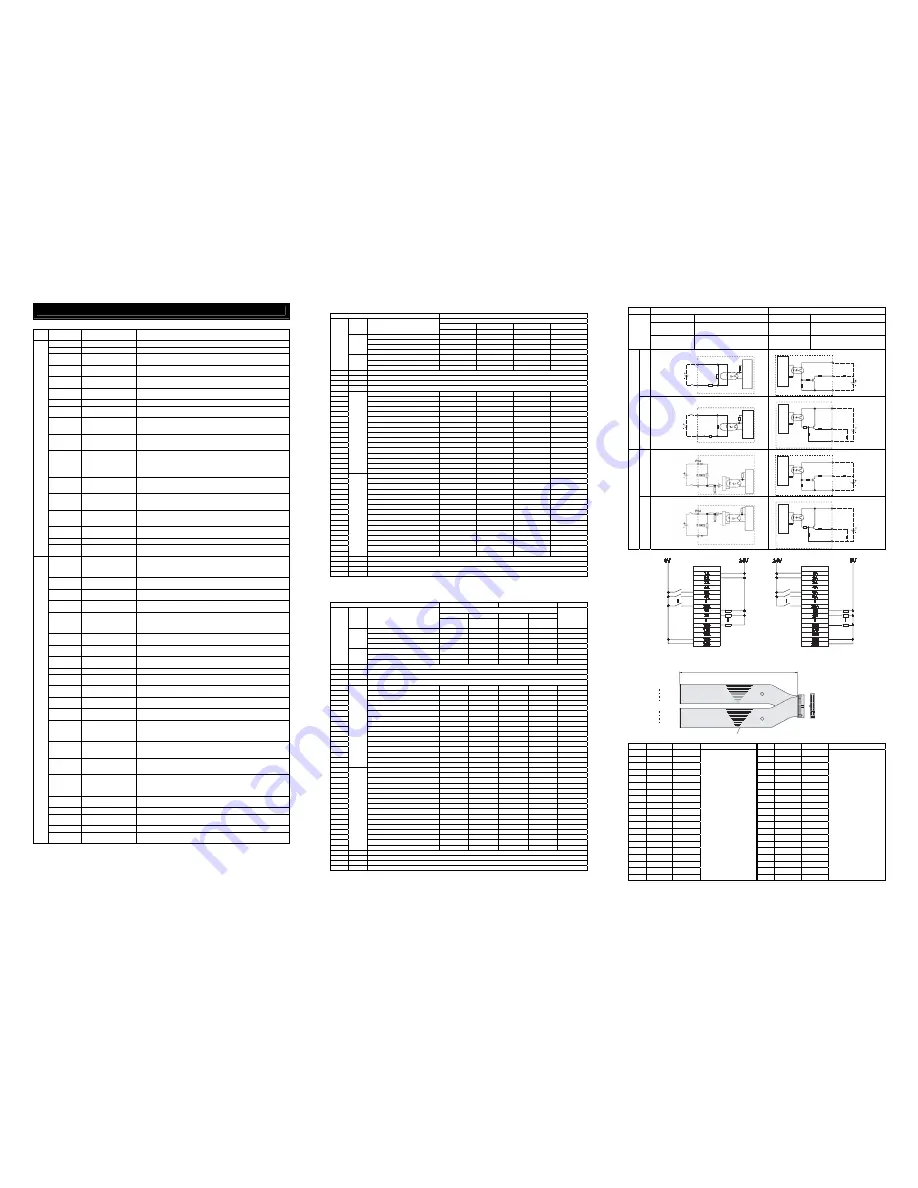
I/O Signal
Explanation of I/O Signal Functions
Category Abbreviated
Code
Signal Name
Contents of Functions
CSTR
Start Signal (PTP Strobe) Starts moving toward the position set in Command Position No.
PC1 to PC256 Command Position No.
To input position No. desired to move (binary input)
BKRL
Brake Compulsory
Release
To release the brake compulsorily
RMOD
Operation Mode
Changeover
Operation Mode can be changed over when MODE Switch on the controller
is on AUTO. The setting is AUTO when signal is OFF, and MANU when ON.
*STP Pause
Turn the signal off during operation to decelerate and stop. Turn the signal
ON to resume the operation.
RES Reset
Turn the signal on to reset the alarm. Also, it is possible to cancel the
residual operation if turning on during the pause (*STP is off).
SON
Servo ON
Turn on to turn the servo ON, and off to turn the servo OFF.
HOME Home
return
Perform the home-return operation with the signal rising edge (OFF
→
ON).
MODE Teaching
Mode
Turn the signal on to set to the Teaching Mode, and off to cancel the
Teaching Mode. The mode will not be switched over unless CSTR, JOG
+
and JOG
−
are all off and the actuator operation is stopped.
JISL Jog/Inching
Changeover
Jog Operation can be performed with JOG
+
and JOG
−
while this signal is
off.
Inching Operation is performed with JOG
+
and JOG
−
when it is on.
JOG
+
JOG
−
Jog
Jog Operation is performed to positive direction by detecting ON edge of
JOG
+
signal and to negative direction by JOG
−
signal while JISL signal is
off. The actuator will decelerate and stop if OFF edge is detected while in
each Jog Operation.
Inching Operation is performed while JISL signal is on.
PWRT Teaching
Write the current position to the indicated position if indicating the written
position and turn this signal on for more than 20ms during the Teaching
Mode.
CLBR
(Specified only
for CA)
Loadcell Calibration
Command
Turn this signal on for more than 20ms to perform calibration of loadcell.
ST0 to ST6 Start Signal 0 to 6
The actuator moves to the commanded position with this signal on during
the electromagnetic valve mode.
(CSTR signal is not required)
TL Torque
Limit
Select Puts torque limitation to the motor with the signal on and the value set to
the parameter.
DCRL
Deviation Counter Clear Clears the deviation count with the signal on.
Input
CSTP Compulsory
Stop
Performs compulsory stop of the actuator. Turn the signal on to decelerate
and stop the actuator and turns the servo off.
PEND/INP Position
Completion
Turns on in the positioning band range after actuator operation. PEND
signal will not turn off once it turns on until the next operation even if the
actuator goes off the range of positioning band. INP will turn off. PEND
and INP can be switched over by the parameter.
PM1 to PM256 Completion Position No. Outputs (binary output) the position No. that is reached at the same time
the positioning is complete.
HEND
Home Return Completion Turns on when home-return operation is complete. It will be kept on unless
the home position is lost.
ZONE1, 2
Zone
Turns on if the current actuator position is within the range set to the
parameter.
PZONE Position
Zone
Turns on when the current actuator position gets into the range set to the
position data during the move towards the position. It can be utilized
together with ZONE 1, however, PZONE is effective only when moving
towards the set position.
RMDS
Operation Mode Output
Outputs the operation mode status. It turns on when the controller is on
Manual Mode.
*ALM Alarm
Turns on when controller in normal condition, and off when alarm is
generated.
MOVE
While in Operation
Turns on during the actuator is moving (including home-return operation
and pressing operation).
SV
Servo ON status
Turns on when the servo is on.
*EMGS
Emergency Stop Output Turns on when the controller emergency stop is cancelled, and off during
the emergency stop (regardless of alarms).
MODES
Teaching Mode Output
Turns on when it turns to the Teaching Mode by MODE signal input. It is off
in the normal mode.
WEND Writing
Complete
Turns on after the writing by PWRT signal is complete in the Teaching
Mode. This signal turns off if PWRT signal is turned off.
PE0 to PE6 Current Position Number Turns on when moving to the target position is complete in
Electromagnetic Valve Mode.
LS0 to LS2 Limit Switch Output
Turns on when the current actuator position is within the range of
positioning band (
±
) of the target position. It is output even before the
movement command and the servo is off if the home-return operation is
completed.
CEND
(Specified only
for CA)
Loadcell Calibration
Complete
Turns on after loadcell calibration is complete. This signal turns off if CLBR
signal is turned off.
*BALM
Warning for Absolute
Battery Voltage Drop
Turns on when the battery voltage for the absolute type actuator is within
the normal voltage range. Replace the battery if it is turned off. (this signal
is always on for the incremental type actuator.)
LOAD
Load Output Judgment
Signal
Outputs when current exceeds the value set to “threshold” within range of
position data “ZONE
+
” or “ZONE
−
” during the pressing operation.
Utilize this signal for a judgment of a press-fitting process being properly
performed, etc.
TRQS Torque
Level
Output Outputs when current of motor reaches the value set to “threshold” by the
slider (or rod) being hit to an obstacle during the pressing movement.
ALM1 to 8
Alarm Code Output
Outputs the alarm code when an alarm is generated
TLR Torque
Limit
Restricted
Turns on when torque reaches the limit while in torque restriction (TL
signal is on).
PWR
System Standby
Turns on when the controller is able to be controlled.
Output
*ALML
Light Error Alarm
(only for SCON-CA)
This turns on when any of the absolute battery alarm, overload alarm or
message level alarm is occurred.
Signal Assignment for Each Mode
The signal assignment of I/O flat cable by the PIO pattern is as shown below. Follow the following table to connect the external equipment (such as PLC).
Corresponding Type
All Types
Selection in Parameter No. 25 (PIO Pattern)
0 1 2 3
Category PIO
Functions
Positioning mode Teaching mode
256-point mode 512-point mode
Number of Positioning Points
64 points
64 points
256 points
512 points
Jog Signal
×
{
×
×
Teaching Signal (Current Position Writing)
×
{
×
×
Input
Brake Release
{
×
{
{
Signal during Operation
{
{
×
×
Zone Signal
{
×
×
×
Pin No.
Output
Position Zone Signal
{
{
{
×
1A 24V
P24
2A 24V
P24
3A
−
−
4A
−
−
5A
IN0
PC1 PC1 PC1 PC1
6A
IN1
PC2 PC2 PC2 PC2
7A
IN2
PC4 PC4 PC4 PC4
8A
IN3
PC8 PC8 PC8 PC8
9A
IN4
PC16 PC16 PC16 PC16
10A
IN5
PC32 PC32 PC32 PC32
11A IN6
−
MODE PC64 PC64
12A IN7
−
JISL PC128 P128
13A IN8
−
JOG
+
−
PC256
14A IN9
BKRL
JOG
−
BKRL BKRL
15A
IN10
RMOD RMOD RMOD RMOD
16A IN11
HOME
HOME
HOME
HOME
17A IN12
*STP
*STP
*STP
*STP
18A IN13
CSTR
CSTR/PWRT
CSTR
CSTR
19A IN14
RES
RES
RES
RES
20A
Input
IN15
SON SON SON SON
1B
OUT0
PM1 (ALM1)
PM1 (ALM1)
PM1 (ALM1)
PM1 (ALM1)
2B
OUT1
PM2 (ALM2)
PM2 (ALM2)
PM2 (ALM2)
PM2 (ALM2)
3B
OUT2
PM4 (ALM4)
PM4 (ALM4)
PM4 (ALM4)
PM4 (ALM4)
4B
OUT3
PM8 (ALM8)
PM8 (ALM8)
PM8 (ALM8)
PM8 (ALM8)
5B OUT4
PM16
PM16
PM16
PM16
6B OUT5
PM32
PM32
PM32
PM32
7B OUT6
MOVE
MOVE
PM64
PM64
8B OUT7
ZONE1
MODES
PM128
PM128
9B OUT8
PZONE/ZONE2 PZONE/ZONE1 PZONE/ZONE1
PM256
10B OUT9
RMDS
RMDS
RMDS
RMDS
11B
OUT10
HEND HEND HEND HEND
12B OUT11
PEND
PEND/WEND
PEND
PEND
13B OUT12
SV
SV
SV
SV
14B OUT13
*EMGS
*EMGS
*EMGS
*EMGS
15B
OUT14
*ALM *ALM *ALM *ALM
16B
Output
OUT15 *BALM
*BALM *BALM *BALM
17B
−
−
18B
−
−
19B 0V
N
20B 0V
N
(
Note
)
“*” in codes above shows the signal of the active low.
PM1 to PM8 indicate the alarm binary code output signal when an alarm is generated.
(Reference) Signal of Active Low
Signal with “*” expresses the signal of active low. A signal of active low is a signal that the input signal is processed when it is
turned off, output signal is ordinary on while the power is on, and turns off when the signal is output.
Corresponding Type
All Types
CA Type
All Types
Selection in Parameter No. 25 (PIO Pattern)
4 5 6 7
Category
PIO Functions
Electromagnetic
Valve Mode 1
Electromagnetic
Valve Mode 2
Force Control
Mode 1
Force Control
Mode 2
Pulse Train
Control Mode
Number of Positioning Points
7 points
3 points
32 points
5 points
−
Jog Signal
×
×
×
×
×
Teaching Signal (Current Position Writing)
×
×
×
×
×
Input
Brake Release
{
{
{
{
{
Signal during Operation
×
×
×
×
×
Zone Signal
{
{
×
×
{
Pin No.
Output
Position Zone Signal
{
{
{
{
×
1A 24V
P24
2A 24V
P24
3A
−
−
4A
−
−
5A IN0
ST0
ST0
PC1
ST0
SON
6A IN1
ST1
ST1
(JOG
+
)
PC2 ST1 RES
7A IN2
ST2
ST2
*1
PC4 ST2 HOME
8A IN3
ST3
−
PC8
ST3 TL
9A IN4
ST4
−
PC16
ST4
CSTP
10A IN5
ST5
−
−
−
DCLR
11A IN6
ST6
−
−
−
BKRL
12A IN7
−
−
−
−
RMOD
13A IN8
−
−
CLBR
CLBR
−
14A IN9
BKRL
BKRL
BKRL
BKRL
−
15A IN10
RMOD
RMOD
RMOD
RMOD
−
16A IN11
HOME
−
HOME
HOME
−
17A IN12
*STP
−
*STP
*STP
−
18A IN13
−
−
CSTR
−
−
19A IN14
RES
RES
RES
RES
−
20A
Input
IN15 SON
SON
SON
SON
−
1B OUT0
PE0
LS0
PM1(ALM1)
PE0
PWR
2B OUT1
PE1
LS1(TRQS)
PM2(ALM2)
PE1
SV
3B OUT2
PE2
LS2
*1
PM4(ALM4)
PE2
INP
4B OUT3
PE3
−
PM8(ALM8)
PE3 HEND
5B OUT4
PE4
−
PM16
PE4 TLR
6B OUT5
PE5
−
TRQS
TRQS
*ALM
7B OUT6
PE6
−
LOAD
LOAD
*EMGS
8B OUT7
ZONE1
ZONE1
CEND
CEND
RMDS
9B OUT8
PZONE/ZONE2 PZONE/ZONE2 PZONE/ZONE1 PZONE/ZONE1
ALM1
10B OUT9
RMDS
RMDS
RMDS
RMDS
ALM2
11B OUT10
HEND
HEND
HEND
HEND
ALM4
12B OUT11
PEND
−
PEND
PEND
ALM8
13B OUT12
SV
SV
SV
SV
−
/*ALML
*2
14B OUT13
*EMGS
*EMGS
*EMGS
*EMGS
−
15B OUT14
*ALM
*ALM
*ALM
*ALM
ZONE1
16B
Output
OUT15 *BALM
*BALM
*BALM
*BALM
ZONE2
17B
−
−
18B
−
−
19B 0V
N
20B 0V
N
(Note) Shown in ( ) after the signal names above tell the functions performed before the home-return operation. “*” in codes
above shows the signal of the active low.
PIO Input and Output Interface
Input section
Output section
Input voltage 24V DC
±
10%
Load voltage
24V DC
Input current
5mA 1 circuit : SCON-CA
4mA 1 circuit : SCON-C
Peak load
electric current
100mA/1 point,
400mA/(Load current total)
Specifi-
cation
ON/OFF voltage
ON voltage MIN. 18V DC
OFF voltage MAX. 6V DC
Leak Current
MAX.0.1mA/1 point
N
P
N
Controller
Internal
Power Supply
P24
Input Terminal
680
Ω
5.6k
Ω
External
Power Supply
24V DC
±10%
Controller
10
Ω
N
Output Terminal
External
Power Supply
24V DC
±10%
Internal
Power Supply
Load
P24
SCO
N
-C
A
P
N
P
Controller
Internal
Power Supply
Input Terminal
680
Ω
5.6k
Ω
External
Power Supply
24V DC
±10%
N
Controller
P24
10
Ω
N
External
Power Supply
24V DC
±10%
Internal
Power Supply
⽶⩄
⽶⩄
Load
Output Terminal
Output Terminal
Output Terminal
N
P
N
Controller
Internal
Power Supply
Input Terminal
External
Power Supply
24V DC
±10%
Logic Circuit
Controller
10
Ω
N
Output Terminal
External
Power Supply
24V DC
±10%
Internal
Power Supply
Load
P24
SCO
N
-C
P
N
P
Controller
Internal
Power Supply
Input Terminal
External
Power Supply
24V DC
±10%
Logic Circuit
Controller
P24
10
Ω
N
External
Power Supply
24V DC
±10%
Internal
Power Supply
⽶⩄
⽶⩄
Load
Output Terminal
Output Terminal
Output Terminal
NPN Specification
PNP Specification
I/O Cable
Model
:
CB-PAC-PIO
□□□
(Enter the cable length (L) in
□□□
Example. 020
=
2m)
No.
Signal Name Cable Color
Wiring
No.
Signal Name Cable Color
Wiring
1A 24V BR-1
1B OUT0 BR-3
2A 24V RD-1
2B OUT1 RD-3
3A
−
OR-1
3B
OUT2
OR-3
4A
−
YW-1
4B
OUT3
YW-3
5A IN0 GN-1
5B
OUT4 GN-3
6A IN1 BL-1
6B
OUT5 BL-3
7A IN2 PL-1
7B
OUT6 PL-3
8A IN3 GY-1
8B
OUT7 GY-3
9A IN4 WT-1
9B
OUT8 WT-3
10A
IN5 BK-1
10B
OUT9 BK-3
11A
IN6 BR-2
11B
OUT10
BR-4
12A
IN7 RD-2
12B
OUT11
RD-4
13A
IN8 OR-2
13B
OUT12
OR-4
14A
IN9 YW-2
14B
OUT13
YW-4
15A
IN10 GN-2
15B
OUT14 GN-4
16A
IN11 BL-2
16B
OUT15 BL-4
17A
IN12 PL-2
17B
−
PL-4
18A
IN13 GY-2
18B
−
GY-4
19A
IN14 WT-2
19B
0V WT-4
20A
IN15 BK-2
Flat Cable
○
A
(Insulation-Displacement
Connectors)
AWG28
20B
0V BK-4
Flat Cable
○
B
(Insulation-Displacement
Connectors)
AWG28
Pin No.
Pin No.
Load
Load
Flat Cable (20-core)
×
2
BK-4
BR-3
BK-2
BR-1
Open-ended
Open-ended
20A
20B
1A
1B
Half Pitch MIL Socket
HIF6-40D-1.27R (manufactured by Hirose)
A
B
L
*1 It is invalid before home-return operation.
*2 Only for SCON-CA.