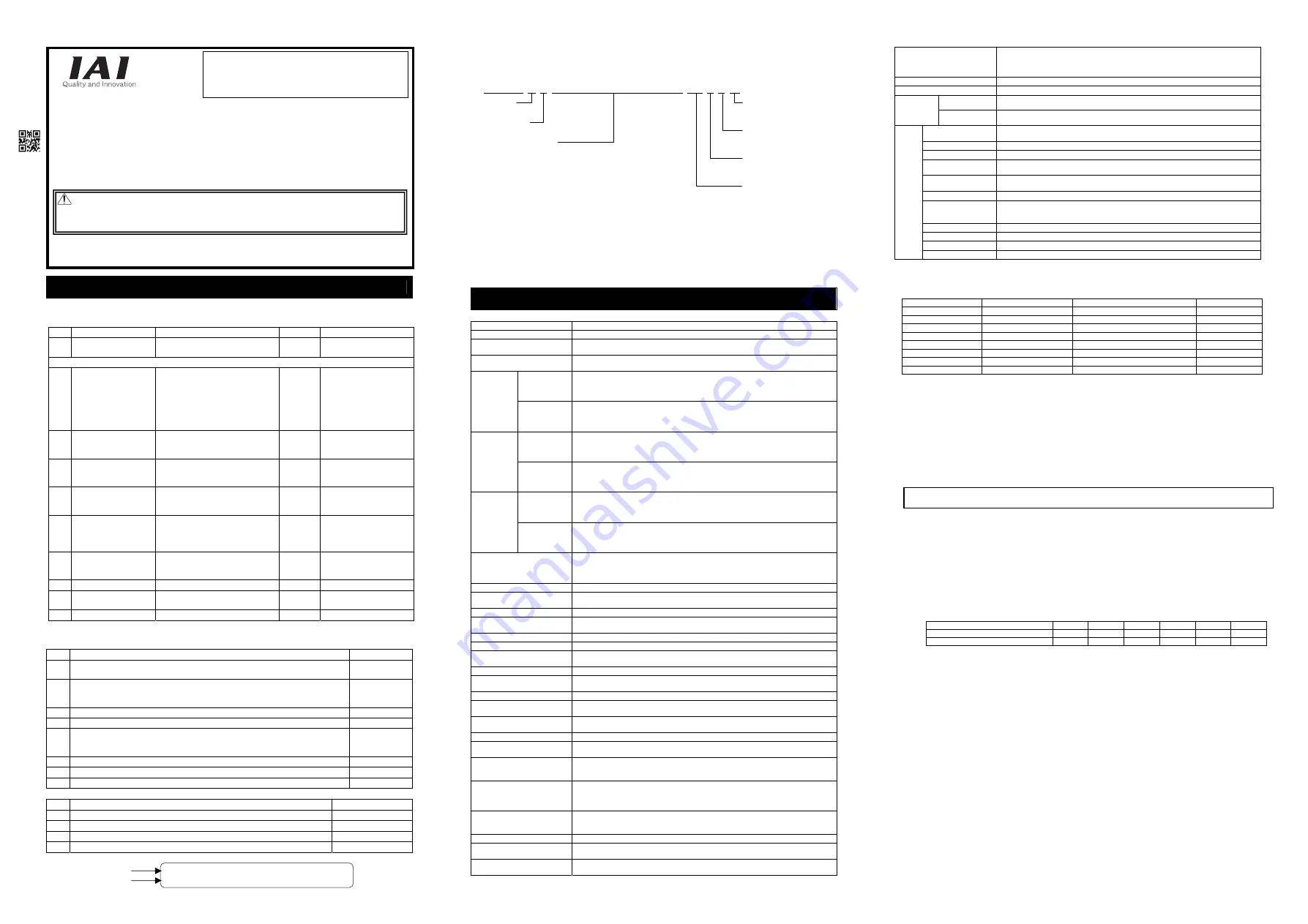
MSCON
First Step Guide First Edition
Thank you for purchasing our product.
Make sure to read the Safety Guide and detailed Instruction Manual (CD/DVD) included with the product in addition to
this First Step Guide to ensure correct use.
This Instruction Manual is original.
•
Using or copying all or part of this Instruction Manual without permission is prohibited.
•
The company names, names of products and trademarks of each company shown in the sentences are registered
trademarks.
Product Check
This product is comprised of the following parts if it is of standard configuration.
If you find any fault in the contained model or any missing parts, contact us or our distributor.
1. Parts
No. Part
Name
Model
Quantity
Remarks
1 Controller
Refer to “How to read the model
plate”, “How to read the model”
1
Accessories
2
Control Power Supply
Connector
MC1.5/5-STF-3.81
(Supplier: PHOENIX CONTACT)
1
Recommended cable size
•
Control Power Input area
KIV3.5 to 0.75mm
2
(AWG12 to 18)
•
Brake Power Input area
KIV0.75mm
2
(AWG18)
3
Motor Power Supply
Connector
GMSTB2.5/3-STF-7.62
(Supplier: PHOENIX CONTACT)
1
Recommended cable size
KIV3.5 to 1.25mm
2
(AWG12 to 16)
4
System I/O Connector
FMCD1.5/4-ST-3.5
(Supplier: PHOENIX CONTACT)
1
Recommended cable size
KIV1.25 to 0.2mm
2
(AWG16 to 24)
5
CC-Link Connector
(For CC-Link Type)
SMSTB2.5/5-ST-5.08 AU
(Supplier: PHOENIX CONTACT)
1
Trminal resistance
(130
Ω
1/2W, 110
Ω
1/2W)
enclosed one unit each
6
DeviceNet Connector
(For DeviceNet Type)
SMSTB2.5/5-ST-5.08 AU
(Supplier: PHOENIX CONTACT)
1
Prepare a terminal resistor
separately if this controller is
to be allocated at the
terminal.
7
Absolute Battery Unit
(Option)
(Battery AB-5)
-
Depends on number of
actuators to be used in
absolute type
8 First
Step
Guide
1
9
Instruction Manual
(CD/DVD)
1
10 Safety
Guide
1
2. Teaching Tool (to be purchased separately)
For the setup operation such as position setting and parameter setting by a teaching, conduct it on PC software.
Prepare a teaching tool such as PC software and so on for the operations and tunings.
No. Part
Name
Model
1
PC Software
(Includes RS232C Exchange A Peripheral Communication Cable)
RCM-101-MW
2
PC Software
(Includes USB Exchange A USB Cable + Peripheral Communication
Cable)
RCM-101-USB
3
Teaching Pendant (Touch panel teaching)
CON-PTA
4
Teaching Pendant (Touch panel teaching equipped with a deadman switch)
CON-PDA
5
Teaching Pendant
(Touch panel teaching equipped with a deadman TP adapter
(RCB-LB-TG))
CON-PGA
6 Teaching
Pendant
CON-T
7
Teaching Pendant (equipped with dead man’s TP adapter (RCB-LB-TG))
CON-TG
8
Gateway Parameter Setting Tool
-
3. Instruction Manuals related to this product, which are contained in the Instruction Manual (CD/DVD).
No. Name
Manual
No.
1
MSCON Controller Instruction Manual
ME0304
2
PC Software
RCM-101-MW/RCM-101-USB Instruction Manual
ME0155
3 Touch
Panel
Teaching CON-PTA/PDA/PGA Instruction Manual
ME0295
4 Teaching
Pendant
CON-T/TG Instruction Manual
ME0178
4. How to read the model plate
5. How to read the model
(Example) Consists of 5 axes : Axis No.0, 2, 3 = 60W actuators to be connected incremental type
Axis No.4, 5 = 100W actuators to be connected incremental type
Axis No.1 = When no connected axis
M S C O N - C - 5 - 6 0 I - N - 6 0 I - 6 0 I - 1 0 0 I - 1 0 0 I - D V - 2 - 0 - * *
Basic Specifications
Specifications
Number of Controlled Axes
Max. 6-axis
Control Power Voltage
24V DC
±
10%
Control Power Current
Consumption
Max. 2.4A
Add the Control Power In Rush
Current
(Note1)
Max. 7A 5msec or less
Driving Source
Voltage
100V AC
Specification
AC100 to 115V
±
10%
Drive (Motor)
Power Supply
Voltage
Driving Source
Voltage
200V AC
Specification
AC200 to 230V
±
10%
Driving Source
Voltage
100V AC
Specification
10A max. with 20A for 80msec (driving source voltage 100V in ambient temp. 25
°
C)
10A max. with 45A for 80msec (driving source voltage 115V × 10% in ambient temp. 40
°
C)
Drive (Motor)
Power Supply
In-Rush
Current
(Note1)
Driving Source
Voltage
200V AC
Specification
10A max. with 45A for 40msec (driving source voltage 200V in ambient temp. 25
°
C)
10A max. with 95A for 40msec (driving source voltage 230V × 10% in ambient temp. 40
°
C)
Driving Source
Voltage
100V AC
Specification
Max. 200W/axis (up to 450W in total for six axes)
Motor
Capacity of
Connectable
Actuators
Driving Source
Voltage
200V AC
Specification
Max. 200W/axis (up to 900W in total for six axes)
Electromagnetic Brake Power
Supply Voltage
(when brake-equipped actuator
connected)
DC24V
±
10%
Brake Power Supply Current
Max. 1A/axis (0.5A/axis at steady state)
Brake Power Supply In-Rush
Current
(Note1)
Max. 10A 10msec or less
Drive (Motor) Power Capacity
Refer to Power Capacity and Heat Generation.
Leak Current
3.5mA (Motor power supply)
◎
There is no leak current of control power supply and brake power supply.
Heat Generation
Refer to Power Capacity and Heat Generation.
Drive (Motor) Frequency
50/60Hz
±
5%
Transient Power Cutoff Durability 1msec (Control Power Supply), 20msec (Drive (Motor) Power Supply), 5msec (Brake
Power Supply)
Motor Control System
Sinusoidal Wave PWM Vector Current Control
Applicable Encoder
Incremental Serial Encoder
Absolute Serial Encoder
Actuator Cable Length
Max. 20m
Serial Communication
(SIO Port: For Teaching)
RS485 1ch (complying with Modbus Protocol) Speed : 9.6 to 230.4kbps
External Interface
DeviceNet, CC-Link, PROFIBUS-DP, CompoNet, MECHATROLINK ll, EtherNet/IP,
EtherCAT®
Data Setting and Input
PC software, Teaching pendant, Gateway parameter setting tool
Number of Positioning Points
Position data and parameters are saved in the nonvolatile memory.
(There is no limitation in number of writing)
Number of Positioning Points
Max. 256 points (There is no limit for simple direct and direct indication modes)
Note: The number of positioning points differs depending on the operation mode select
by the parameter setting.
LED Indication
(Mounted on Front Panel)
LED lamp for driver status display 2 points
Gateway Status LED 5 points
Fieldbus Status LED 2 points
Power Supply Status LED 2 points
Forcibly Releasing of
Electromagnetic Brake
(Mounted on Front Panel)
Switching NOM (standard)/RLS (compulsory release)
Protective Functions
Overload, overcurrent, overvoltage, etc.
Protection Function against
Electric Shock
Class I
Insulation Resistance (Between
secondary power source and FG) 500V DC 10M
Ω
or more
Withstanding Voltage (Between
primary and secondary power
sources, Between primary power
source and PE)
1500V AC for 1 min. (for MSCON individually)
Cooling Method
Forced air-cooling
External Dimensions
225W × 154H × 115D
Incremental Type Approx. 1900g
Weight
(when drivers
for 6 axes
mounted)
Absolute Type
Approx. 2000g (including batteries)
Surrounding air
temperature
0 to 40
°
C
Surrounding humidity
85%RH or less (non-condensing)
Surrounding environment [Refer to Installation and Storage Environment.]
Surrounding storage
temperature
-20 to 70
°
C
(Note) 0 to 40
°
C for absolute battery.
Surrounding storage
humidity
85%RH or less (non-condensing)
Usable Altitude
1000m or lower above sea level
Vibration Durability
Frequency 10 to 57Hz/ Swing width: 0.075mm
Frequency 57 to 150Hz/ Acceleration 9.8m/s
2
XYZ Each direction Sweep time: 10 min. Number of sweep: 10 times
Package Drop
Dropping height 800mm, 1 corner, 3 edges and 6 surfaces
Protection Class
IP20
Pollution Degree
I
Enviro-
nment
Overvoltage Category
II
Note 1 The rush current value varies depending on the impedance of the power line.
<Power Capacity and Heat Generation>
Shown in the table is the relation between the motor wattage and motor power capacity of an actuator that
can be connected
RS : Rotary Shaft
<Remark 1>
Selection of Circuit Breaker
•
3 times of the rated current flows to the controller during the acceleration/deceleration. Select an
interrupter that does not trip with this value of current. If a trip occurs, select an interrupter that
possesses the rated current of one grade higher. (Check the operation characteristics curves in the
product catalog.)
•
Select an interrupter that does not trip with the in-rush current. (Check the operation characteristics
curves in the product catalog.)
•
Consider the current that enables to cutoff the current even when a short circuit current is flown for
the rated cutoff current.
Rated Interrupting Current > Short Circuit Current = Circuit Breaker Primary Power Capacity / Power Voltage
Consider margin for the rated current on the circuit breaker.
<Remark 2> Selection of Leak Current Breaker
•
It may be mandatory by low to install a leakage breaker.
•
A ground fault circuit interrupter needs to be selected carefully considering the purposes of prevention
of fire and protection of human (Determined by law).
•
Leak current varies depending on the capacity of connected motor, cable length and the surrounding
environment. Measure the leak current at the point where a ground fault circuit interrupter is to be
installed when leakage protection is conducted.
•
Use the harmonic type (for inverter) for the ground fault circuit interrupter.
<Control Power Capacity>
Follow the description below for the calculation of 24V DC power capacity.
(1) Control Power Current Consumption :
Select from control power supply current in the table below
··············
1)
Number of Controlled Axes
(Note1)
1 Axis
2 Axis
3 Axis
4 Axis
5 Axis
6 Axis
Control Power Unit Heating Value [W]
25.5
31.5
38.2
44.2
50.9
56.9
Control Power Capacity [A]
1.1
1.3
1.6
1.8
2.1
2.4
Note 1 : See the line of max. number of controlled axes connectable to corresponding MSCON.
manufacturing name plate : MSCON-C-*-• • • •: “*” is the maximum number of connectable axes.
(2) Current Consumption of Brake Power Supply :
1A or 0.5A
(Note 2)
× number of brake-equipped actuators
··············
2)
Note 2 : The maximum current of 1A per actuator runs for approximately 100ms when a brake is
released. The current consumption after the release is 0.5A per unit.
Calculate the capacity with 0.5A per unit when a 24V DC power supply corresponding to
transient load change such as peak load appliance is used and capable for the maximum
current described above. For other cases, calculate with 1A per unit.
(3) Add the Control Power In Rush Current : 7A
····································································
3)
[Selection of Power Supply]
Usually, the rated current is to be approximately 1.3 times higher than the total of Control Power 1) and
Motor Power 2) above considering approximately 30% of margin to the load current. However, considering
the inrush currents [excitation 3)], even though it is a short time, select a power supply with sufficient “peak
load capacity”. If a power supply with insufficient peak capacity is utilized, a transient voltage drop or cutoff
may occur. This may present issues with power supplies providing remote sensing functionality.
<Remark 3> Selection of Power Supply Protection Circuit Breaker
It is recommended that the power supply protection is conducted on the primary side (AC power side)
of the 24V DC power supply unit.
If having 24V DC turned ON/OFF, keep the 0V connected and have the +24V ON/OFF (cut one side only).
Be careful to the in-rush current of the 24V DC power supply unit when making a selection. (Check it in
the operation characteristics curve graph in a catalog provided by the supplier.)
Consider the current that enables to cutoff the current even when a short circuit current is flown for the
rated cutoff current.
•
Rated Interrupting Current > Short Circuit Current = Circuit Breaker Primary Power Capacity / Power Voltage
•
(Remark) In-rush Current of IAI Power Supply Unit PS241 = 50 to 60A, 3msec
Actuator Motor Wattage
Motor Power Capacity [VA]
Peek Max. Motor Power Capacity [VA]
Heat Generation [W]
12 41
123 1.7
20 50
150 2.0
30D (Excluding RS)
47
141
2.0
30R (for RS)
138
414
4.0
60 146
438
4.8
100 238
714
7.0
150 328
984
8.3
200 421
1263
9.2
<Type Name>
C :
Standard Type
<Connected Axis>
1 to 6 : Number of driver axes
<Detail of Connected Axis>
[Motor Type]
12 :
12W Servo Motor, 20
:
20W Servo Motor
30D : 30W Servo Motor, 30R : 30W Servo Motor (for RS Series)
60
: 60W Servo Motor, 100 : 100W Servo Motor
150 : 150W Servo Motor, 200 : 200W Servo Motor
N
: Not connected
[Encoder Type]
I :
Incremental
A :
Absolute
[Option]
HA :
High
Accel/Decel
Type
L
: Home Sensor/Limit Switch Type
C :
Creep
Sensor
Type
B :
Brake
Type
<Identification for IAI use only>
*There is no identification in
some cases
<Power-supply Voltage>
1 : AC100V
2 : AC200V
<I/O cable Length>
0 : No cable
<I/O Type>
DV : DeviceNet Type
CC : CC-Link Type
PR : PROFIBUS-DP Type
CN : CompoNet Type
ML : MECHATROLINK Type
EP : EtherNet/IP Type
EC : EtherCAT® Type
Applicable Field Network
(DeviceNet, CC-Link, PROFIBUS, CompoNet,
MECHATROLINK-ll, EtherNet/IP, EtherCAT®)
Rated Current for Circuit Interrupter >
Total capacity of motor power for all the connected actuators / AC input voltage × Safety margin (1.2 to 1.3 for reference)
MODEL MSCON-C-6-200AHA-200AHA-200AB-100A-100A-60AB-DV-0-2
SERIAL No.01234567
Model No.
Serial number
Warning : Operation of this equipment requires detailed installation and operation instructions which are
provided on the CD/DVD Manual included in the box this device was packaged in. It should be
retained with this device at all times.
A hard copy of Manual can be requested by contacting your nearest IAI Sales Office listed at
the back cover of the Instruction Manual or on the First Step Guide.