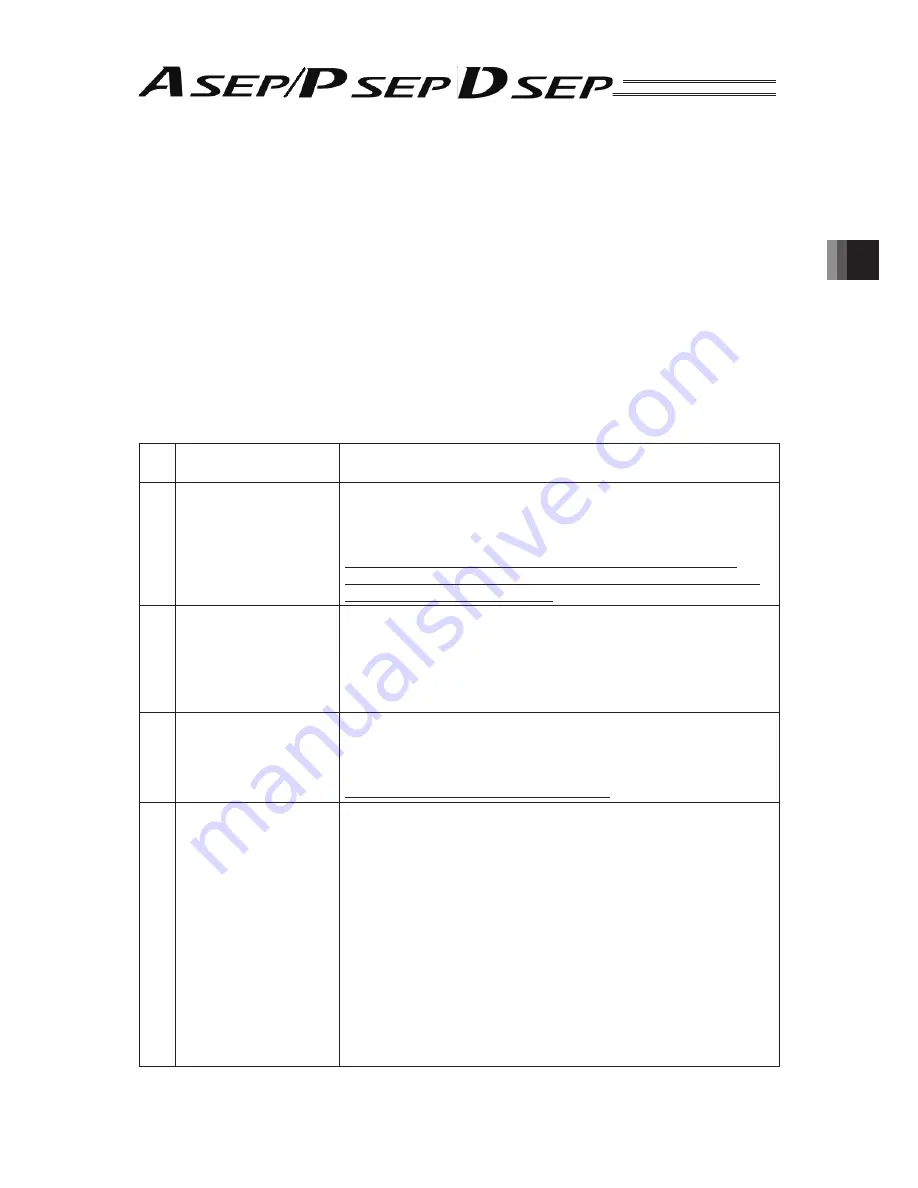
65
/
3. Operation
3.5 Servo
Adjustment
The parameters are preset at the factory before shipment to perform a stable operation in response to
the position command in the range of the actuator use with the rated (maximum) transportable weight.
However, the preset setting cannot always be the optimum load condition in the actual use. It is
considered that the actuator needs to be operated under various conditions including resonance,
vibration trigger, load
fl
uctuation, etc.
It is clear that the servo performs a more stable operation with the optimum adjustment that best suits
to the actual installation, load and operation conditions. Please note such a product like our actuator
that is designed to enable the operation in a large number of situations may need a servo adjustment
in a use under certain conditions.
3.5.1
Adjustment for ASEP and PSEP
(Note) Make an adjustment following Section 3.5.2 if using DSEP.
No.
Situation that Requires
Adjustment
How to Adjust
1
Takes time to
fi
nish
positioning/Positioning
accuracy is not
appropriate / Shorter
takt time is desired
Increase the “Servo-Motor Gain Number”. By setting a bigger
number, the follow-up ability to the position command becomes
better. Try to increase one by one. If the value is too large, an
overshoot is caused easily and may cause noise or vibration.
If the “Servo-Motor Gain Number” is increased, also adjust the
“Velocity Loop Proportional Gain” in increasing direction to ensure
the stability in the control system.
2
Vibration is generated
at acceleration/
deceleration
Decrease the numbers for “Acceleration/Deceleration Setting” and
“Servo-Motor Gain Number”. The cause of the problem is the lack
of strength in the mechanical structure. Reinforce the mechanical
structure,
fi
rst.
If the “Servo-Motor Gain Number” setting is too low, it takes long
time to
fi
nish the positioning.
3
Speed is uneven
during the movement/
Speed accuracy is not
appropriate
Increase the “Velocity Loop Proportional Gain” value. By setting a
bigger number, the follow-up ability to the speed command becomes
better. Setting the value too big makes the mechanical components
easy to vibrate. As a reference for the setting, increase the value
little by little by 20% from the initial setting.
4
Abnormal noise is
generated/Especially,
when stop and
operation in low speed
(less than 50mm/sec),
comparatively high
noise is generated.
Input the “Torque Filter Time Constant”. Try to increase by 50 as a
reference for the setting. If the setting is too large, it may cause a
loss of control system stability and lead the generation of vibration.
• Prior to Adjustment:
This phenomenon is likely to occur when the stiffness of the
mechanical components is not suf
fi
cient. The actuator itself may
also resonate if its stroke is over 600mm or it is belt-driven type.
Before having an adjustment, check if:
1) The settings for “Servo-Motor Gain Number”, “Velocity Loop
Proportional Gain” and “Velocity Loop Integrated Gain” values
are extreme.
2) The stiffness of the load is suf
fi
cient as much as possible, or
the attachments are not loosened.
3) The actuator unit is properly mounted with no looseness.
4) There is no waviness on the actuator mounting surface.
Содержание ASEP
Страница 1: ...DSEP Controller ASEP Controller PSEP Controller Instruction Manual Tenth Edition ...
Страница 2: ......
Страница 4: ... ...
Страница 115: ......