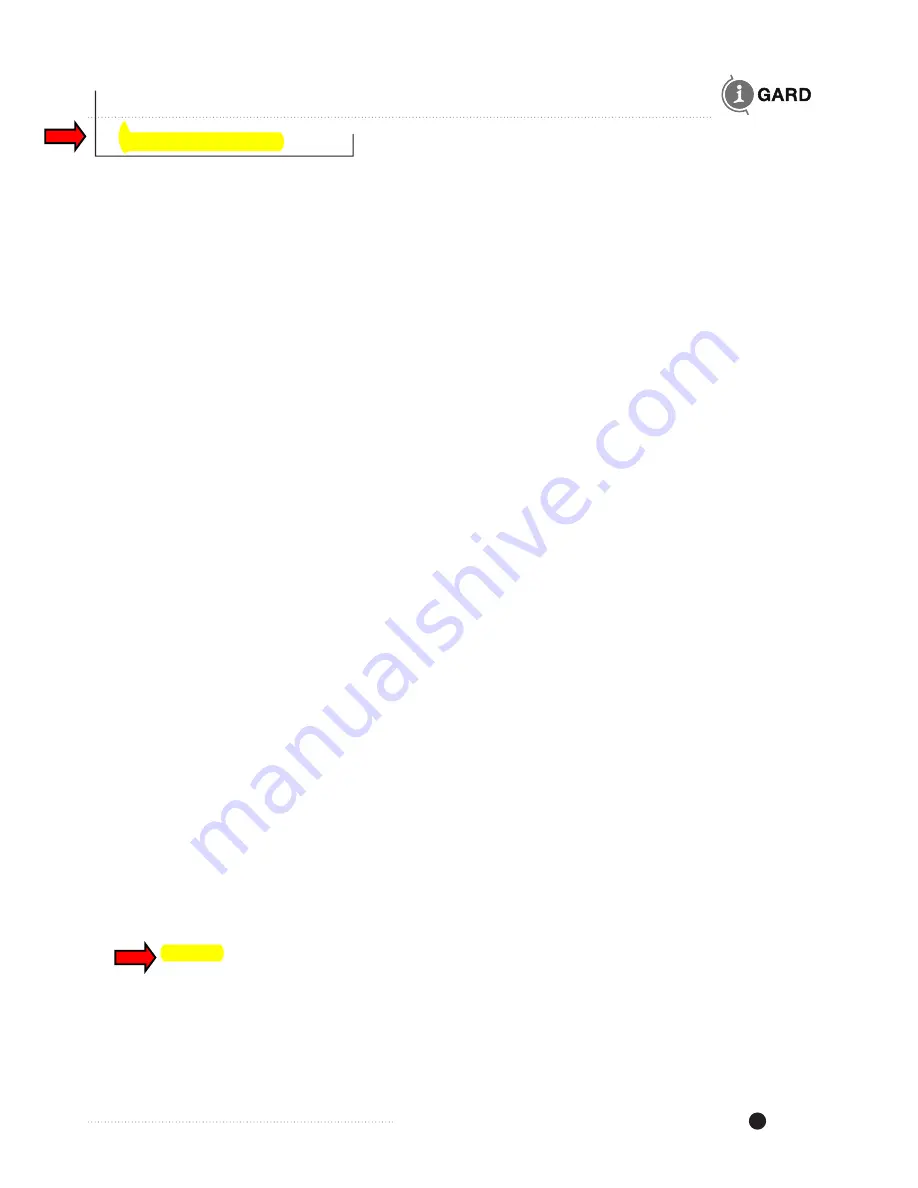
DSP-OHMNI Instruction Manual 429EM Version 2,
June 2010
I-GARD
3
1
INTROduCTION
High-Resistance-Grounding is becoming more prevalent in industrial and commercial electrical power
systems. As the need for reliable and stable power increases the inconvenience of unwanted downtime
in processing, robotics and data service also become more critical and costly.
Single Ground Faults in motors and equipment are common and will cause interruption of service in Solidly
Grounded systems. HRG prevents this event from happening by limiting the fault current to a sustainable
level for an indefinite time.
The DSP-OHMNI system will provide the user with an Alarm and indication of the location of the fault using
a combination of voltage and current measurements.
In some applications, however, it is desirable to clear any fault on the system when it occurs with fire
prevention or protection of sensitive equipment being the main concern rather than continuity of service.
e.g. petro-chemical, grain handling. In this case, in addition to fault indication the DSP-OHMNI can be
programmed up to Trip the breakers associated with the fault with or without adjustable Time Delay.
The DSP-OHMNI system is designed to detect the event of a single fault and signal an alarm condition and
point to the affected branch or feeder. Thus maintenance can be immediately alerted to the problem and an
operator dispatched to locate the fault to isolate it promptly. The DSP-OHMNI system can assist in locating
the fault with a pulsing fault location circuit that modulates the current in the fault circuit. This allows the
operator to identify and locate the fault location though the branch circuit which is carrying fault current by
using a portable clamp-on current probe connected
to an ordinary ammeter (DMM) meter.
Additionally, the DSP-OHMNI has two TRIP modes of operation. It can be set up to control circuit breakers
to TRIP on the occurrence of a single fault with or without time delay, or if the Feeder Circuit Ground Fault
current exceeds 100A on two (Phase to ground to Phase) faults. (This can only occur when two faults exist
since the current on a single fault cannot exceed the Grounding Resistor Rate current) the DSP-OHMNI can
then be set up to selective second ground fault trip on a priority basis to protect the critical feeder. Because
two circuits will be involved it is possible to prioritize which circuit will be interrupted by an priority setting.
This ensures that only the least important circuit is interrupted.
Where it is important to protect sensitive equipment, the DSP-OHMNI can be setup to TRIP the faulted
Feeder Module on the first fault, with, or without, time delay (up to 99 minutes). The Alarm Level is normally
set at 50% (default) of the system maximum ground current, however with the DSP-OHMNI Version 2
system other Alarm Levels between 10% and 90% may be set as desired.
The DSP-OHMNI system consists of a number of modules that are mounted on a 35mm DIN rail
typically located in a control compartment of switchgear. The modules are connected together through
20-conductor standard ribbon cable. A panel-mounted Display module provides a human interface to the
system allows set-up and control.
There are four DSP modules as follows:
Additionally there are other optional modules
DSP-DM Display Module
DSP-DRM Grounding Resistor Monitor
DSP-DPS Power Supply
DSP-DLM Data Logging Module
DSP-DSM System Module
DSP-CA Cable Adapter
DSP-DFM Feeder Module
DSP-CAS Cable Adapter with on/off switch