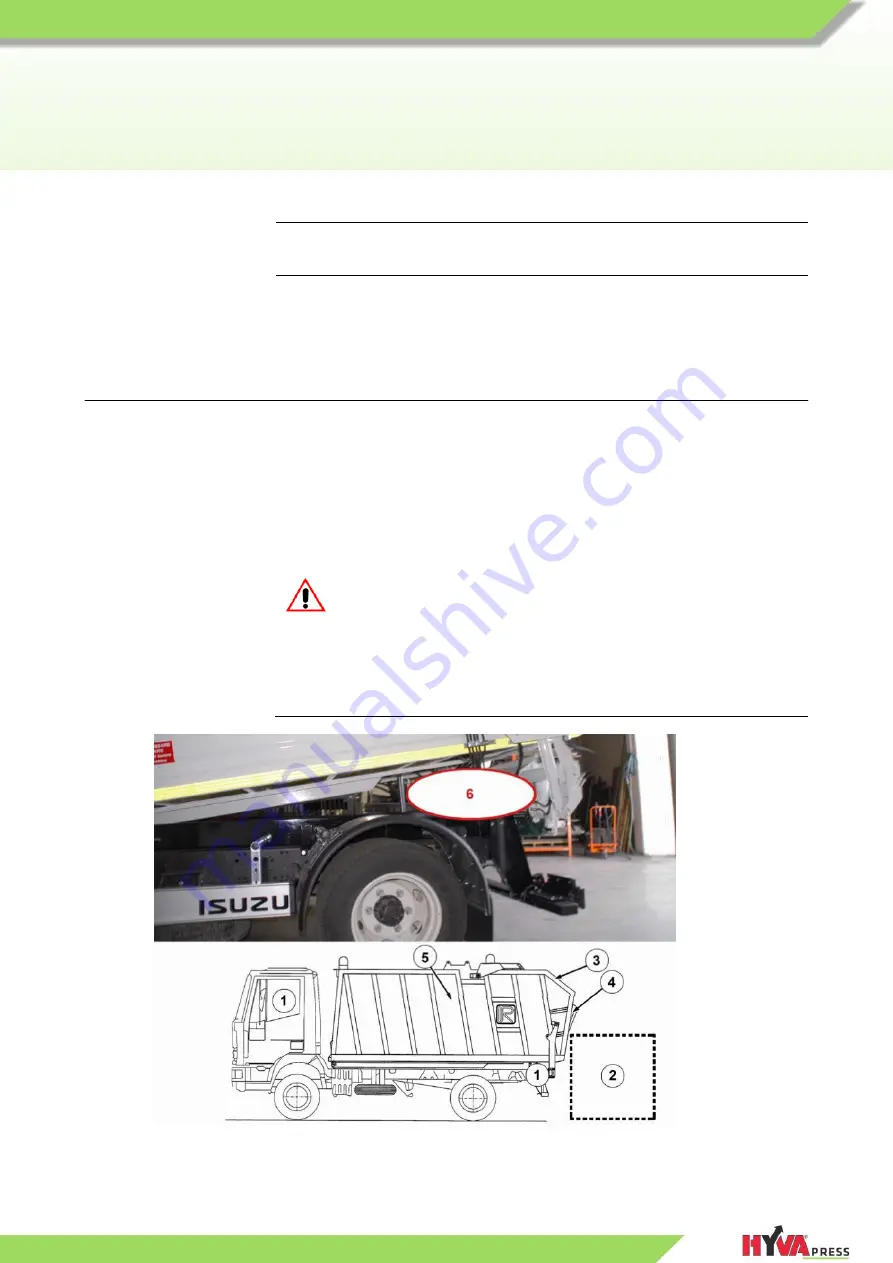
New R-Line Refuse Collection Micro
User Manual RCM10
22
3.7.1 Work areas and dangerous areas
Introduction
The work areas and dangerous areas are described below.
Work areas
The diagram in figure 3-1 indicates the work areas, the main command
areas, and the dangerous areas.
Work areas:
1) Operator command and control area;
2) Operator area for loading/unloading bins.
Dangerous areas
Dangerous areas:
3) The area inside the collection container, where the compacting
shovel functions;
4) The bin lifting and tipping area;
5) The movement area (inside the protection guards on both sides of
The tank) of the hydraulic arms that move the compacting shovel;
6) The area below the raised collection tank.
ATTENTION
The term "dangerous area" also includes:
• All the work areas inside the machine;
• All the areas protected by the special protection guards.
Fig.3 - 1