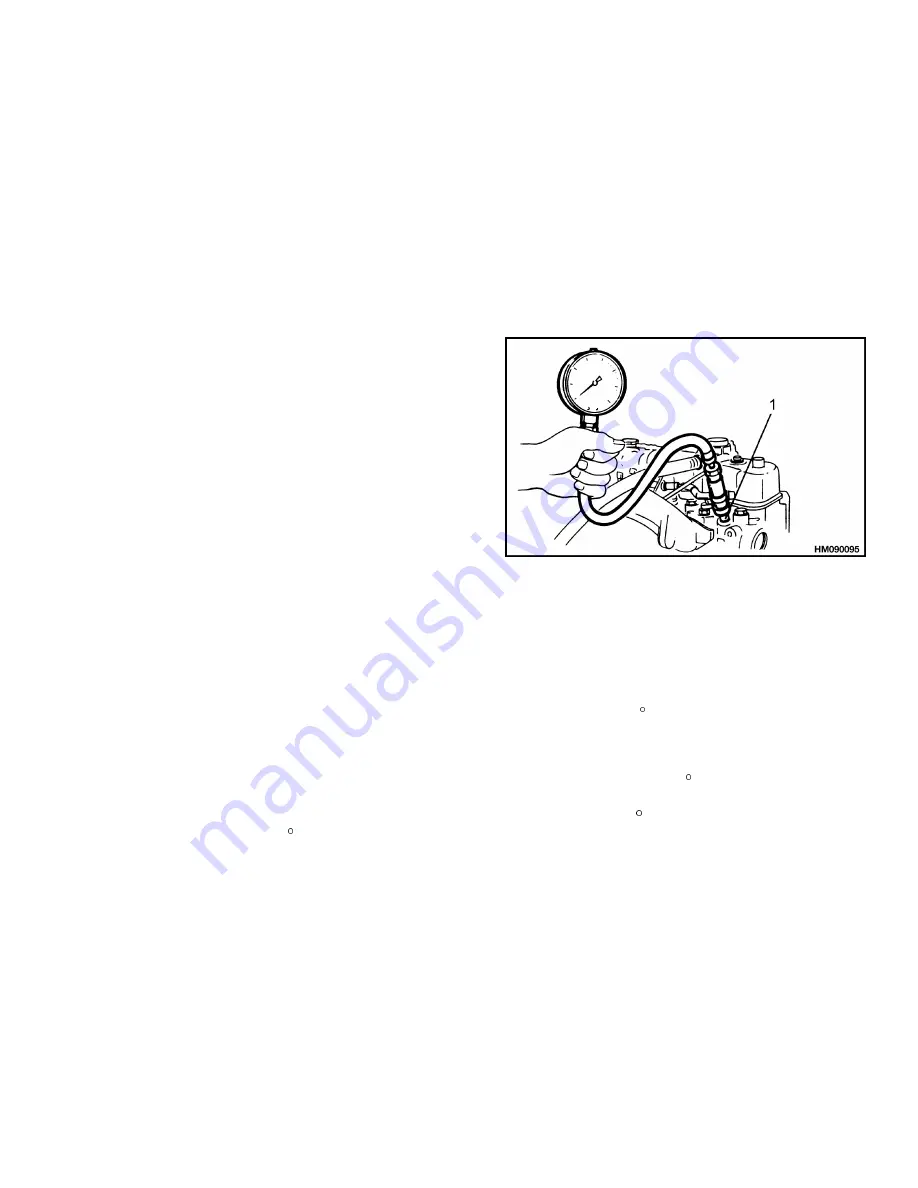
600 SRM 496
Engine Timing Adjustment
Compression Pressure Check
1.
Remove spark plugs from cylinder head. Discon-
nect high tension wire at ignition coil. See Fig-
ure 53.
2.
Install compression gauge in No.
1 cylin-
der. Make sure gauge has minimum range of
1725 kPa (250 psi).
3.
Use starter to crank engine at least six revolu-
tions. Check pressure reading and release pres-
sure. Repeat test again and make note of highest
pressure. Do this test for each cylinder.
Standard pressure reading is 1130 kPa (164 psi).
Minimum reading is 793 kPa (115 psi).
4.
If the readings are lower than minimum reading,
there is a problem with the valves, piston rings,
or cylinder head gasket. Do the following tests to
find the problem:
a. Add approximately 30 ml (1.0 oz) of engine
oil to each cylinder at spark plug hole.
b. Crank engine approximately 10 revolutions
to distribute oil.
c.
Install compression gauge and do same tests
as described in Step 3.
• If pressure reading increases to normal
reading, low pressure was caused by worn
or damaged piston rings.
Cylinder bore
may also be damaged.
• If pressure reading does not increase, low
pressure was caused by worn valves, valve
seats, or valve guides.
• If low pressure readings are in two cylin-
ders next to each other, cylinder head may
be leaking.
1.
ADAPTER
Figure 53. Compression Pressure Check
Engine Timing Adjustment
See Ignition System Check and Adjustment in the
section Mazda M4-2.0G And M4-2.2G Gasoline/
LPG Engines 2200 SRM 524 for the adjustment pro-
cedure for engine timing.
The correct timing for the H1.50-1.75XM, H2.00XMS
(S/H25-35XM, S/H40XMS) units is as follows:
• Gasoline Engine = 0 BTDC @ 725 ±25 rpm
(white mark)
• LPG Engine = 8 BTDC @ 725 ±25 rpm
The correct timing for the S/H2.00-3.20XM (SH40-
65XM) units is as follows:
• Gasoline Engine = 0 BTDC @ 725 ±25 rpm
(white mark)
• LPG Engine = 9 BTDC @ 725 ±25 rpm (red mark)
25
Содержание D010
Страница 37: ......
Страница 38: ...TECHNICAL PUBLICATIONS 600 SRM 496 2 01 4 96 1 96 1 95 9 93 4 93 Printed in U S A ...