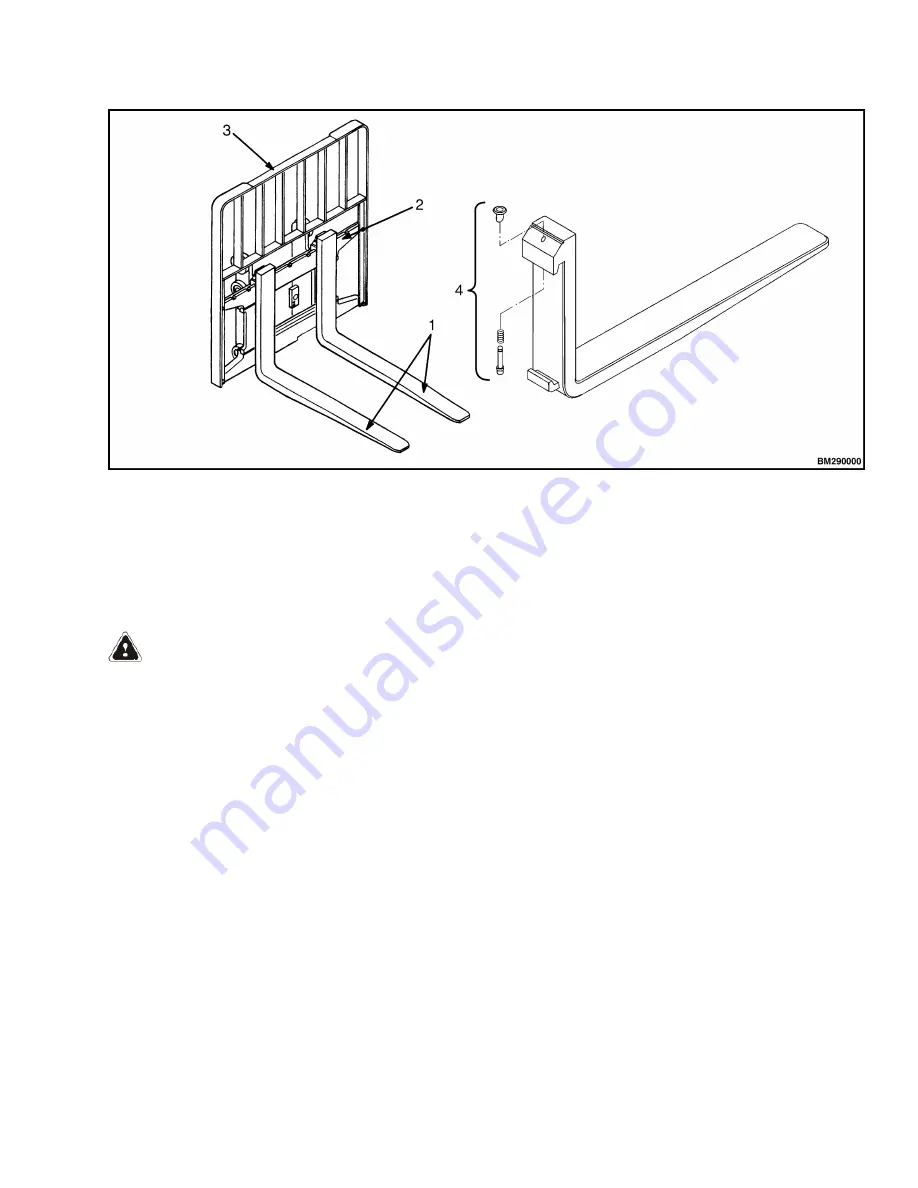
1. FORK
2. CARRIAGE
3. LOAD BACKREST
4. LOCK PIN
Figure 9. Fork Assembly
1.
Inspect the welds on the mast and carriage for
cracks. Make sure the nuts and capscrews are
tight.
WARNING
Always wear the proper protective equipment in-
cluding eye protection and petroleum-resistant
gloves when handling hydraulic oil. Thoroughly
wash oil from exposed areas of skin as soon as
possible.
Never check for leaks by putting hands on hy-
draulic lines or components under pressure. Hy-
draulic oil under pressure can be injected into the
skin.
Completely lower forks to relieve hydraulic pres-
sure before disassembling any part of the lift
pump or disconnecting any hydraulic hoses.
2.
Inspect the mast header hoses and fittings for
hydraulic leaks. Check the hose cover for cracks
or exposed reinforcement. Check for broken or
defective clamping devices. Repair or replace
any damaged components as necessary.
3.
Inspect the channel for excessive wear in the
areas of roller contact. Check the rollers for
wear or damage.
4.
Inspect the load backrest extension for cracks
and damage.
5.
Inspect the forks for cracks and wear. See Fig-
ure 10. Check that the fork tips are aligned
within
3%
of
each
fork
length
[32.00 mm (1.26 in.) for a standard
1067 mm (42 in.) fork]. Some applications can
require closer alignment. Check that the bot-
tom of the fork is not worn. Check that the
thickness of the fork blade (5, Figure 10) is at
least 90% of the thickness of the fork shank
(DIMENSION X). The fork's thickness can also
be checked using fork tool 3020387.
8000 SRM 1379
Maintenance Procedures Every 8 Hours or Daily
15