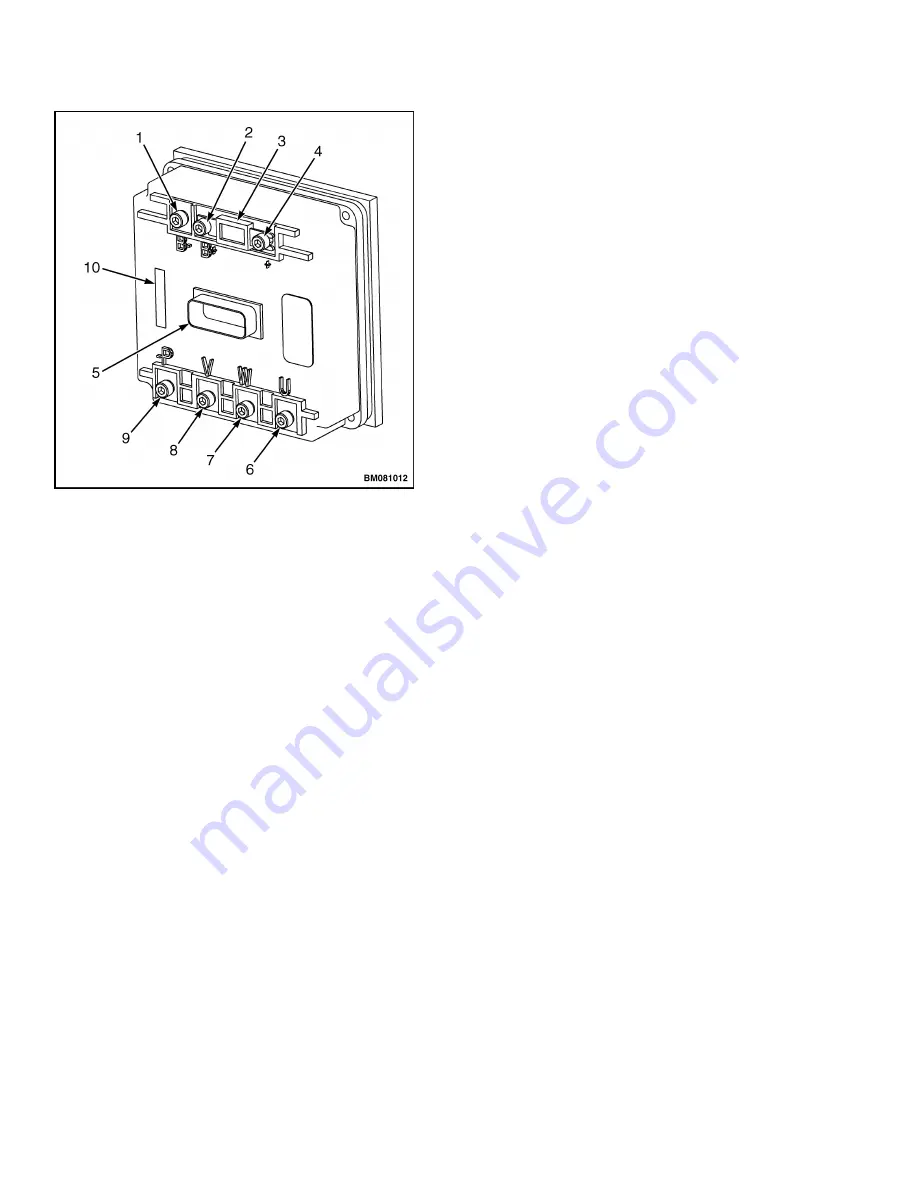
Repairs
2200 SRM 1357
1.
B– TERMINAL
2.
B+ TERMINAL (POS CONNECTION STD)
3.
MAIN FUSE (STD LOCATION)
4.
+ TERMINAL (POS CONNECTION EE)
5.
MAIN CONNECTOR
6.
TRACTION MOTOR POS (TERMINAL U)
7.
TRACTION MOTOR POS (TERMINAL W)
8.
TRACTION MOTOR POS (TERMINAL V)
9.
PUMP MOTOR POS (TERMINAL P)
10. LABEL (PART NUMBER)
Figure 7. Controller Wiring
4.
Discharge the capacitor. See Special Precautions
in this section.
5.
Tag and disconnect wires from the controller. See
Figure 7.
6.
Remove mounting screws and remove controller.
Install
1.
Install replacement controller on lift truck using
mounting hardware.
2.
On models with the Arctic option, install shield
box to controller studs and secure using four
nuts.
3.
Connect wires and cables to the proper terminals
as identified during the removal procedure.
4.
Connect battery and turn the key switch to the
ON position.
5.
Turn parking brake to the OFF position and test
for proper operation.
6.
Install the drive unit compartment covers. See
the section Periodic Maintenance 8000 SRM
1368.
CONTROL MODULE
Check
The control module converts analog signals from the
control handle to digital signals for the controller to
read. If the controller is reporting an input error
fault code, then the control module may be malfunc-
tioning. Check the control module using the follow-
ing steps. See Figure 8.
1.
Connect the battery and turn the key switch to
the ON position. Make sure the parking brake
switch is in the OFF position.
2.
Connect the negative voltmeter lead to the nega-
tive battery cable connection at the controller.
3.
Disconnect the output connector (J5) from the
control module.
4.
Using the positive voltmeter lead, test pin #6 at
the output connector (J5-6).
5.
If there is no voltage at J5-6 then troubleshoot
the controller. See the section AC Motor Con-
troller 2200 SRM 1352.
6.
If the voltmeter shows the proper reading (+24V),
check the input connector (J4) voltages. See Ta-
ble 2.
NOTE:
Voltage should be present at J4-2, J4-3, J4-6,
and J4-9 ONLY while activating the corresponding
function. See Table 2.
7.
If the input values differ from those in the table,
troubleshoot the control handle components, con-
troller, and wiring. Make any necessary repairs,
and recheck the input values.
8.
If the input values are correct, replace the control
module. See Remove.
NOTE:
ETACC may be used to check communication
between control handle, control module, and traction
controller. See the section AC Motor Controller
2200 SRM 1352.
10