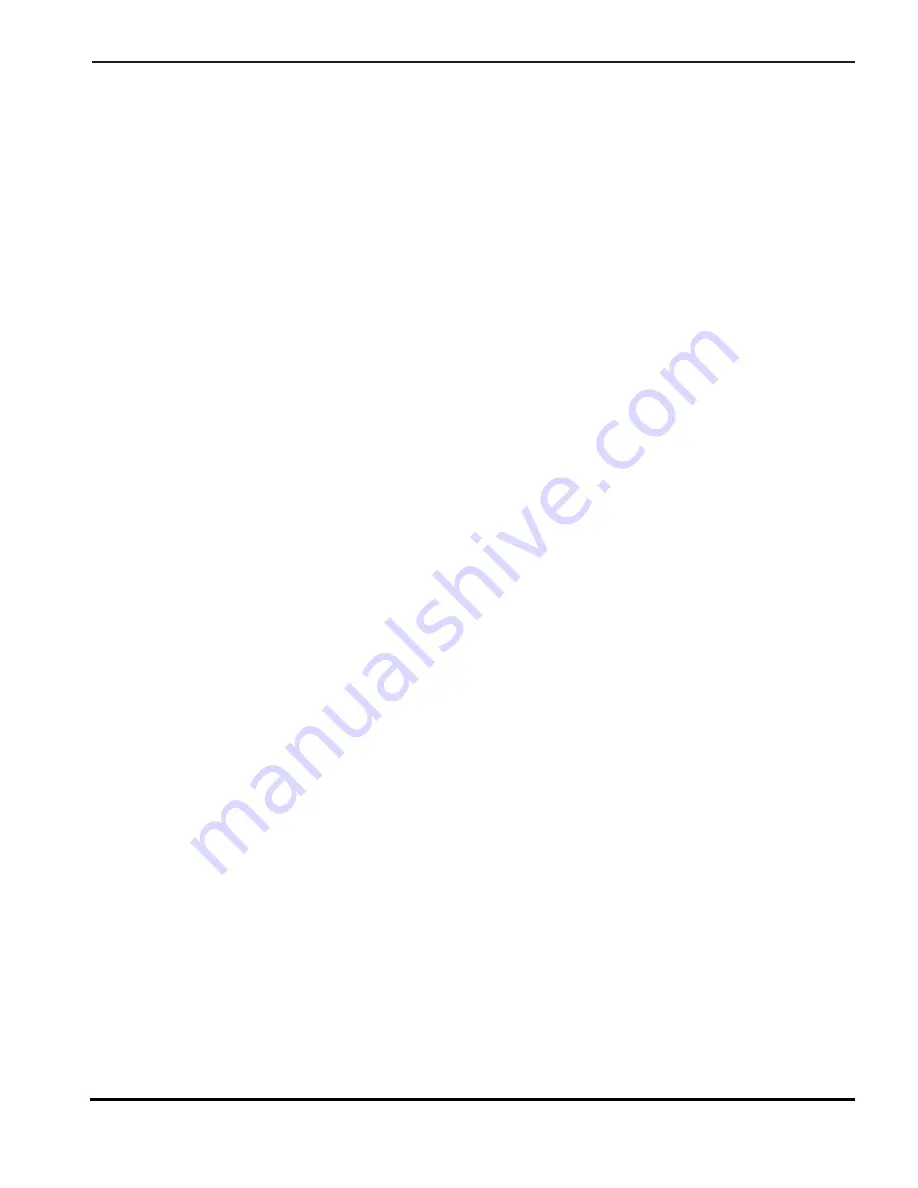
ELECTROMAGNETIC COMPATIBILITY (EMC)
EMC INTRODUCTION
Hypertherm's CE-marked equipment is built
in compliance with standard EN50199. The
equipment should be installed and used in
accordance with the information below to
achieve electromagnetic compatibility.
The limits required by EN50199 may not be
adequate to completely eliminate interfer-
ence when the affected equipment is in
close proximity or has a high degree of sen-
sitivity. In such cases it may be necessary to
use other measures to further reduce inter-
ference.
This plasma equipment is designed for use
only in an industrial environment.
INSTALLATION AND USE
The user is responsible for installing and
using the plasma equipment according to
the manufacturer's instructions. If electro-
magnetic disturbances are detected then it
shall be the responsibility of the user to re-
solve the situation with the technical assis-
tance of the manufacturer. In some cases
this remedial action may be as simple as
earthing the cutting circuit, see Earthing of
Workpiece. In other cases it could involve
constructing an electromagnetic screen en-
closing the power source and the work com-
plete with associated input filters. In all
cases electromagnetic disturbances must
be reduced to the point where they are no
longer troublesome.
ASSESSMENT OF AREA
Before installing the equipment the user
shall make an assessment of potential elec-
tromagnetic problems in the surrounding
area. The following shall be taken into
account:
a. Other supply cables, control cables, sig-
nalling and telephone cables; above, below
and adjacent to the cutting equipment.
b. Radio and television transmitters and
receivers.
c. Computer and other control equipment.
d. Safety critical equipment, for example
guarding of industrial equipment.
e. Health of the people around, for
example the use of pacemakers and hear-
ing aids.
f. Equipment used for calibration or mea-
surement.
g. Immunity of other equipment in the en-
vironment. User shall ensure that other
equipment being used in the environment is
compatible. This may require additional pro-
tection measures.
h. Time of day that cutting or other activities
are to be carried out.
Earthing of Workpiece
Where the workpiece is not bonded to earth
for electrical safety, nor connected to earth
because of its size and position, for example,
ship's hull or building steelwork, a connection
bonding the workpiece to earth may reduce
emissions in some, but not all instances.
Care should be taken to prevent the earthing
of the workpiece increasing the risk of injury
to users, or damage to other electrical equip-
ment. Where necessary, the connection of
the workpiece to earth should be made by a
direct connection to the workpiece, but in
some countries where direct connection is
not permitted, the bonding should be
achieved by suitable capacitances selected
according to national regulations.
Note. The cutting circuit may or may not be
earthed for safety reasons. Changing the
earthing arrangements should only be au-
thorized by a person who is competent to
assess whether the changes will increase
the risk of injury, for example, by allowing
parallel cutting current return paths which
may damage the earth circuits of other
equipment. Further guidance is given in IEC
TC26 (sec)94 and IEC TC26/108A/CD Arc
Welding Equipment Installation and Use.
Screening and Shielding
Selective screening and shielding of other
cables and equipment in the surrounding
area may alleviate problems of interference.
Screening of the entire plasma cutting in-
stallation may be considered for special ap-
plications
The size of the surrounding area to be con-
sidered will depend on the structure of the
building and other activities that are taking
place. The surrounding area may extend
beyond the boundaries of the premises.
METHODS OF REDUCING EMISSIONS
Mains Supply
Cutting equipment must be connected to the
mains supply according to the manufactur-
er's recommendations. If interference oc-
curs, it may be necessary to take additional
precautions such as filtering of the mains
supply. Consideration should be given to
shielding the supply cable of permanently
installed cutting equipment, in metallic con-
duit or equivalent. Shielding should be elec-
trically continuous throughout its length.
The shielding should be connected to the
cutting mains supply so that good electrical
contact is maintained between the conduit
and the cutting power source enclosure
Maintenance of Cutting Equipment
The cutting equipment must be routinely
maintained according to the manufacturer's
recommendations. All access and service
doors and covers should be closed and
properly fastened when the cutting equip-
ment is in operation. The cutting equipment
should not be modified in any way except for
those changes and adjustments covered in
the manufacturer's instructions. In particu-
lar, the spark gaps of arc striking and stabi-
lizing devices should be adjusted and main-
tained according to the manufacturer's
recommendations.
Cutting Cables
The cutting cables should be kept as short
as possible and should be positioned close
together, running at or close to the floor
level.
Equipotential Bonding
Bonding of all metallic components in the
cutting installation and adjacent to it should
be considered. However, metallic compo-
nents bonded to the workpiece will increase
the risk that the operator could receive a
shock by touching these metallic compo-
nents and the electrode at the same time.
The operator should be insulated from all
such bonded metallic components.
HYPERTHERM Plasma Systems
i