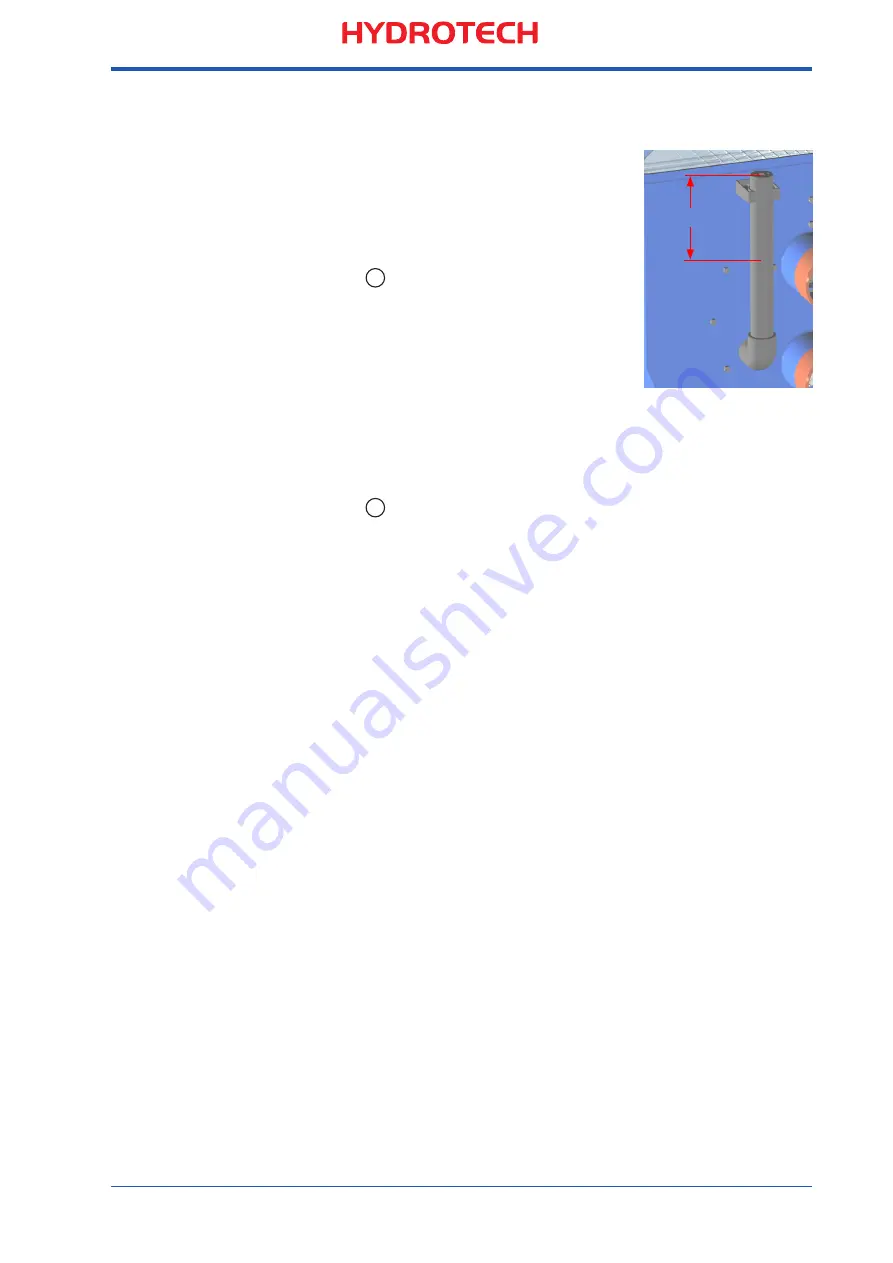
15
Operation and maintenance manual for
Hydrotech Drumfilter HDF501-series
5.2.3.Adjusting.the.level.sensor
Adjust the level sensor to 230-250 mm below the
top of the level pipe. The optimal position depends
on how turbulent the water surface is (see
Figure
5.5.2
).
5.2.4.Setting.the.time.relay
A time relay (see
5
Figure 5.2
) is used to delay
the backwash stop when the water level is below
the level sensor. The time relay is preset so that the
drum is backwashed during one rotation.
In some applications it might be necessary to
increase the backwash time delay to avoid long
term clogging.
5.2.5.Setting.the.level.relay
The sensitivity of the level sensor can be set from MIN. to MAX. on the level
relay and three different sensitivity ranges can be selected on the lower level
relay switch (see
6
in
Figure 5.2
).
If the appropriate sensitivity is not within the selected range change it to
another sensitivity range. For water with a high conductivity (= low resistance)
chose setting 1. For water with a low conductivity (= high resistance) chose
setting 3. Sea water, for example, has a high conductivity.
See also appendix E, level sensors.
5.3.Backwash.system
The standard backwash nozzles (TeeJet 6505) have an equivalent opening
size of 1.4 mm. For some applications it may be necessary to use a lower
rinse water flow. This can be achieved by installing nozzles with a smaller
opening size. Contact the supplier or Hydrotech for more information.
The backwash system pressure is set to 7-8 bars.
5.4.Drum.rotation
The filter is powered by a gear motor that rotates the drum by direct drive.
Direction of rotation is marked on the motor cover.
5.5.Re-tightening.of.bolts
After two working weeks or 80 production hours, all bolted joints must be re-
tightened.
Figure 5.5.2
Adjusting the level sensor
230-250 mm