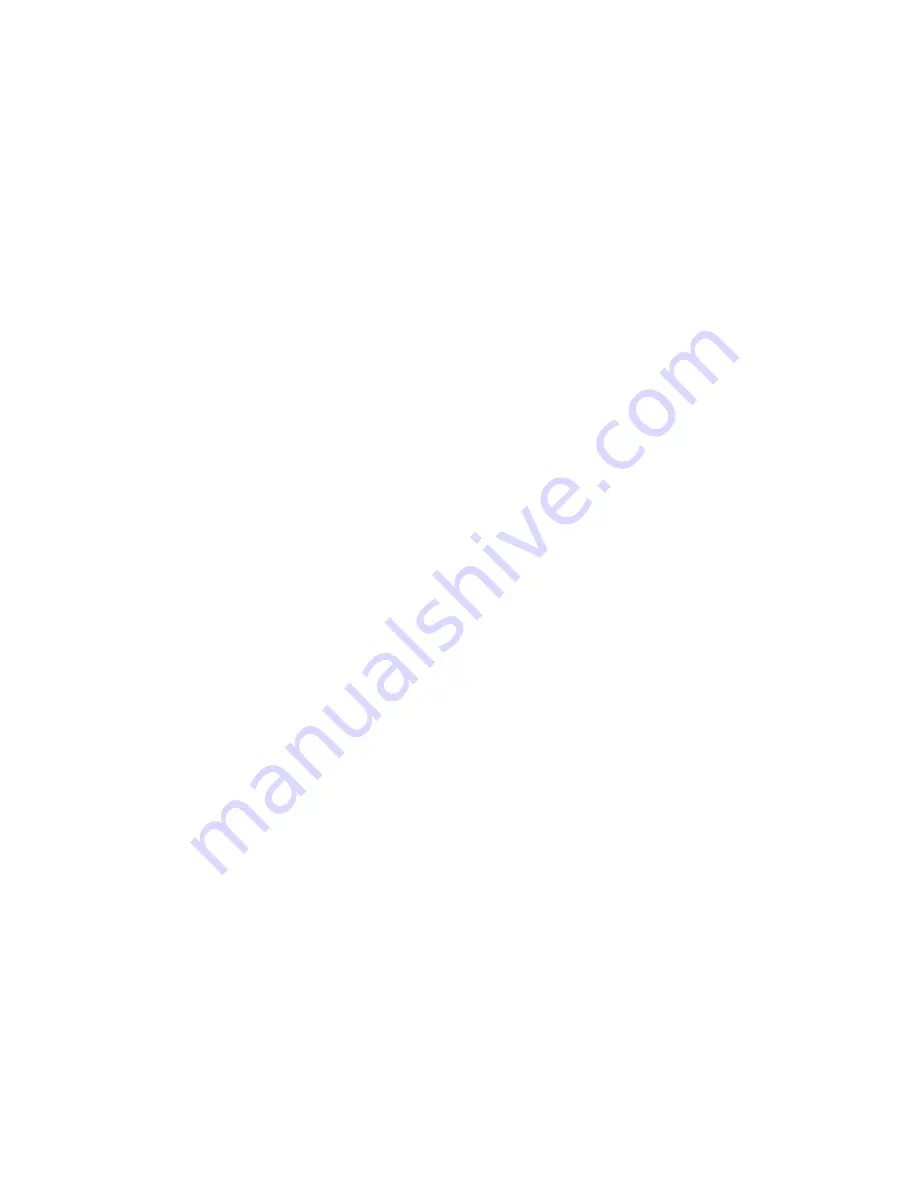
14
III. OPErATIOn
1. Leak Testing
Please refer to and follow the leak testing procedure outlined in this section before performing the
initial start-up, if the piping has been changed, if the vaporizer has just been cleaned, or for other
situations in which air/moisture has been allowed to enter the system.
Warning: When performing this step, ensure that all protective equipment is available.
Warning: Before beginning the leak test ensure that all appropriate measures have been taken
to remove any cutting oils and/or unwanted residue from the piping system. These residues can
cause accelerated pipe corrosion and result in a leak.
NOTe: Before performing this step, be sure to read Hydro Instruments “Nitrogen Purging” document
for further information.
a. Individually leak test all expansion chamber assemblies and pressure relief assemblies before
beginning this test procedure. Also, test the operation of the pressure switch in each expansion
chamber assembly and pressure relief assembly before beginning this procedure.
b. Ensure that piping is installed correctly and securely. Also check to ensure that all the chlorine
container valves are closed and that no chlorine is in the manifold piping.
c. Connect a dry air or nitrogen supply to the end of the chlorine manifold through a ball valve
suitable for chlorine manifold service. Make sure that required pressure controls are installed to
ensure that the nitrogen or dry air pressure entering the manifold cannot exceed 150 psi (10 bar).
d. Purge the system piping with a supply of dry air or nitrogen to remove any moisture or debris (for
more information, refer to the Chlorine Institute’s pamphlet 6).
e. Once the system has been adequately purged, pressurize the piping to 150 psi (10 bar) using dry
air or nitrogen. Then close the air or nitrogen supply valve and record the pressure reading. Watch
to ensure that the pressure reading does not drop. Any drop in pressure indicates the presence of a
leak that must be identified and corrected before proceeding further.
f. Check the entire manifold for leaks using soapy water all the way up to the regulator. If bubbles
form there is a leak. The piping must be re-worked and steps d and e must be repeated.
g. Lower the nitrogen/dry air pressure to slightly below the chlorine gas pressure, and seal off the
nitrogen/dry air connection to the chlorine manifold with a valve or connection that is rated for
chlorine manifold service. Then connect the manifold to the chlorine container gas valves (do not
connect to the chlorine container liquid valves). Ensure that no moisture has been allowed to enter
the system. Close all the valves in the pipeline.
h. Open one chlorine gas container valve and its isolation valve and then quickly close them. Check
for leaks on the manifold one section at a time using a 26 Baume solution of ammonia. If white
smoke appears, there is a leak. If there is a leak, evacuate the system using the ejector and correct
the leak. Then repeat steps d through h. Correct all leaks before moving to the next step.
i. Open all manifold valves (but, keep the isolation valves and the chlorine container valves closed).
Evacuate the system using the ejector. Open one chlorine container gas valve briefly and then
close the valves quickly to reintroduce chlorine gas into the system. Then check for leaks one
section at a time all the way up to the regulator using a 26 Baume solution of ammonia.
j. With the chlorine gas container valves and isolation valves still closed, evacuate the system by
operating the ejector until the pressure reads (and holds at) 0 psi (0 bar).
Содержание VPH-10000-2 Series
Страница 1: ...1 Series VPH 10000 2 Vaporizer Instruction and Operation Manual VPH 10000 2 Rev 5 7 15 ...
Страница 10: ...10 Figure 1 Heater Control Box Diagram for Power 3PH Power In ...
Страница 31: ...31 Figure 8 Chlorine Vapor Pressure Curve Figure 6 Chlorine Vapor Pressure Curve Vapor Pressure ...
Страница 33: ...33 Figure 10 Ammonia Vapor Pressure Curve Figure 8 Ammonia Vapor Pressure Curve Vapor Pressure Min Superheat ...