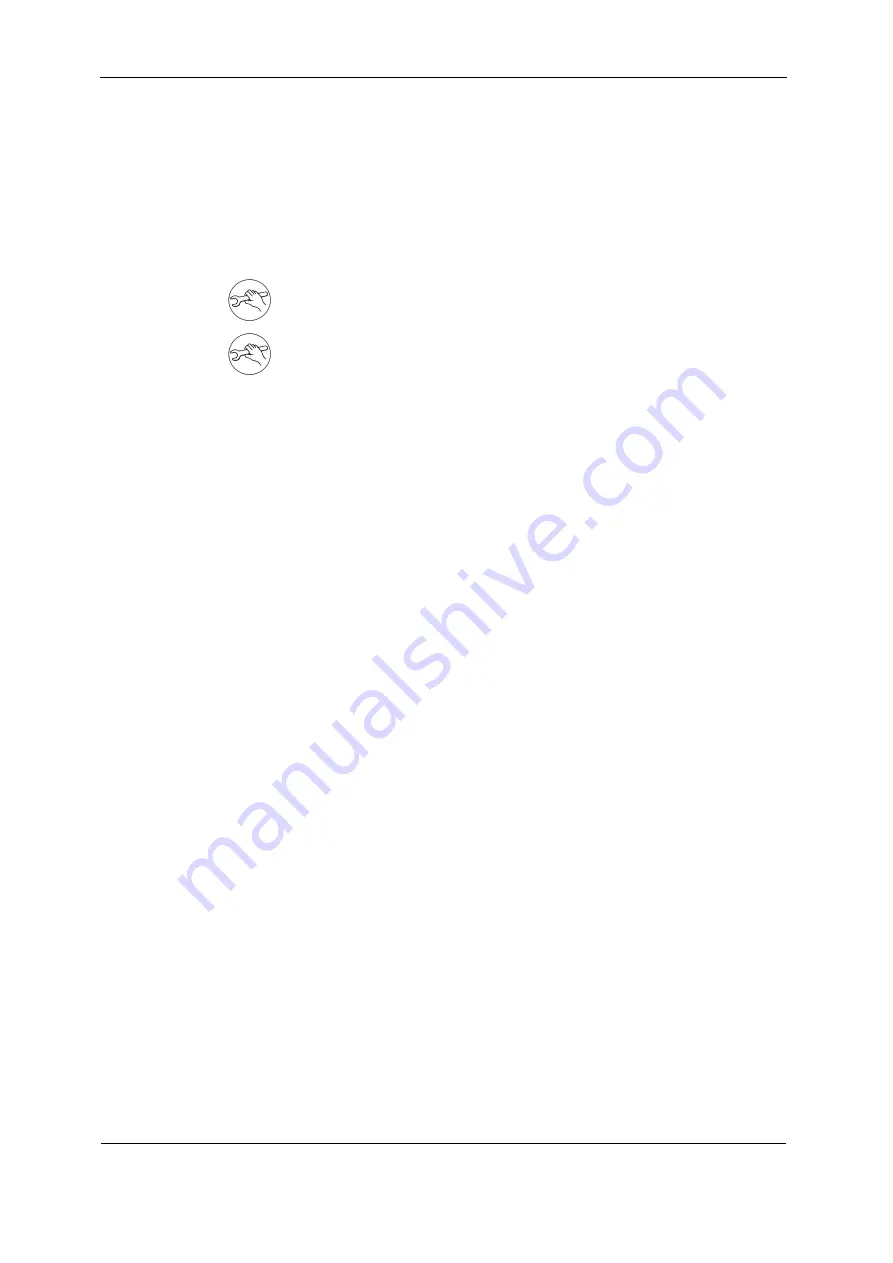
FAM 15/30 ATEX
Performing maintenance / inspection
HYDAC FILTER SYSTEMS GMBH
en(us)
Page 62 / 84
BeWa FAM15_30 Atex 3197970c en-us 2012-08-08.doc
2012-08-08
Replacing the filter element on the fluid filter
If the fault indicator lamp "Replace filter element" [H10]" lights up, replace the filter
element on the fluid filter. For details see page 62.
To change the filter element, you need the following:
Filter element N15DMxxx (quantity and type dependent on version)
Allen wrench, size 6 mm
Fork wrench, size 13 mm