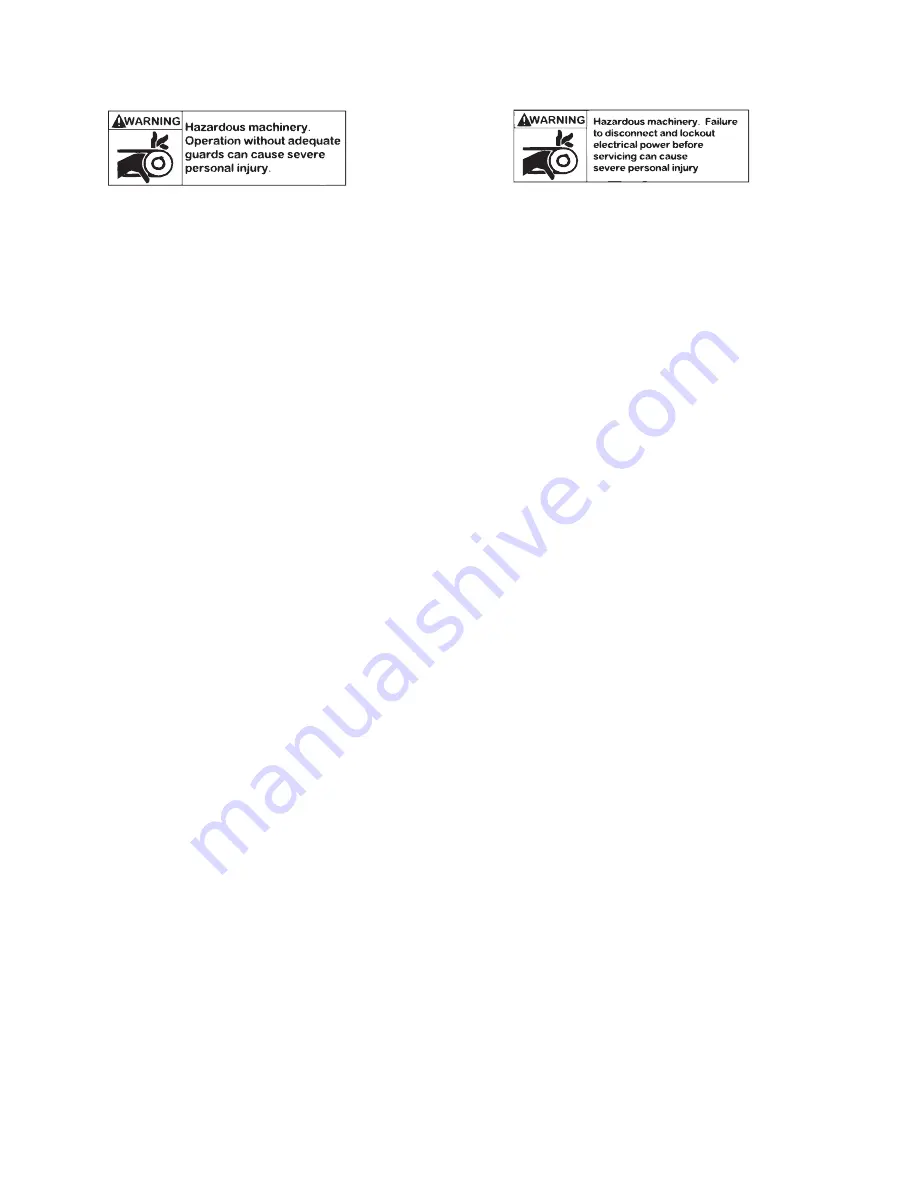
25
SECTION 2
COMPRESSOR STARTUP
Verify that the actual operating conditions will
match expected conditions.
Reciprocating compressors installed at
permanent locations must be mounted on a
reinforced concrete foundation (6 bag / 4000
psi mix) weighing at least twice the weight of
the bare compressor. Fill a permanent mounted
baseplate/skid with epoxy grout.
Allow for 18” of clearance for air circulation and
service access around the compressor.
Outdoor compressor installations must be
protected from the effects of the environment with
a suitable enclosure or overhead protection.
A power disconnect for the machine must be
installed as per NEC & local code.
Check the compressor oil level.
Lockout/tagout the compressor control panel and
tighten all electrical connections within the control
panel (if provided) before startup. Connections
can come loose during shipping leading to
intermittent faults.
Bump the compressor and check for proper
rotation (Clockwise viewed from oil pump end).
Use
fl
exible braided metal hose connections of
proper pressure and temperature rating, to the
compressor and system inlet and discharge ports.
Do not use rubber hose.
Ensure Gas Packing cases are properly plumbed
to vent/pad/purge locations.
All Air Booster and Gas Compressors must have
an inlet receiver sized per Hycomp installation
manual. Ensure that inlet and discharge receiver
tanks are secured and bolted down.
Air Booster and Gas compressors must have
a properly sized
fi
lter installed at the suction
receiver inlet to protect the booster from system
contamination. Filter should be 1 micron or better,
sized for minimal pressure drop.
Ambient Air Compressors must have an inlet
fi
lter
installed.
Ensure properly sized pressure safety valves are
protecting the inlet and discharge piping systems
and are placed between the compressor and any
isolation ball valve, per ASME Code.
A properly sized check valve must be located in
the discharge line, after the aftercooler.
Protect personnel from high temperature piping/
tubing by insulating, warning, and/or restricting
access to the machine boundary.
Instrument lines to control sensors, unloader
controls, etc., must be 3/8” tubing and drawn
from a receiver, not from the compressor inlet/
discharge piping.
Install an oil seep drain line and container to route
and contain drainage from the crosshead cylinder.
A hose barb is provided for this purpose.
Double nut, Nyloc nut, or Loctite foundation
bolting. Check all bolting after the
fi
rst few hours
and days of operation for tightness.
Compressors are shipped with ISO 100 / SAE
30 weight oil. Refer to installation manual to
ensure this is appropriate for your environmental
conditions.
Check your system for leaks and
fi
x as required.
Remove all pressure from system and isolate and
drain before attempting
fi
xes.
Complete the Hycomp Warranty Registration
Card and return it to Hycomp. Call 24/7 with
questions.
INSTALLATION CHECKLIST - REVIEW BEFORE CONTINUING
Содержание Air Boosters
Страница 2: ...THIS PAGE INTENTIONALLY LEFT BLANK ...
Страница 35: ...35 Controls Adjustment Notes make notes here Device Setting Date ...
Страница 58: ...THIS PAGE INTENTIONALLY LEFT BLANK ...
Страница 59: ...THIS PAGE INTENTIONALLY LEFT BLANK ...
Страница 60: ...WI 400 010 APP 1 Rev 5 Rev 2 13 ...