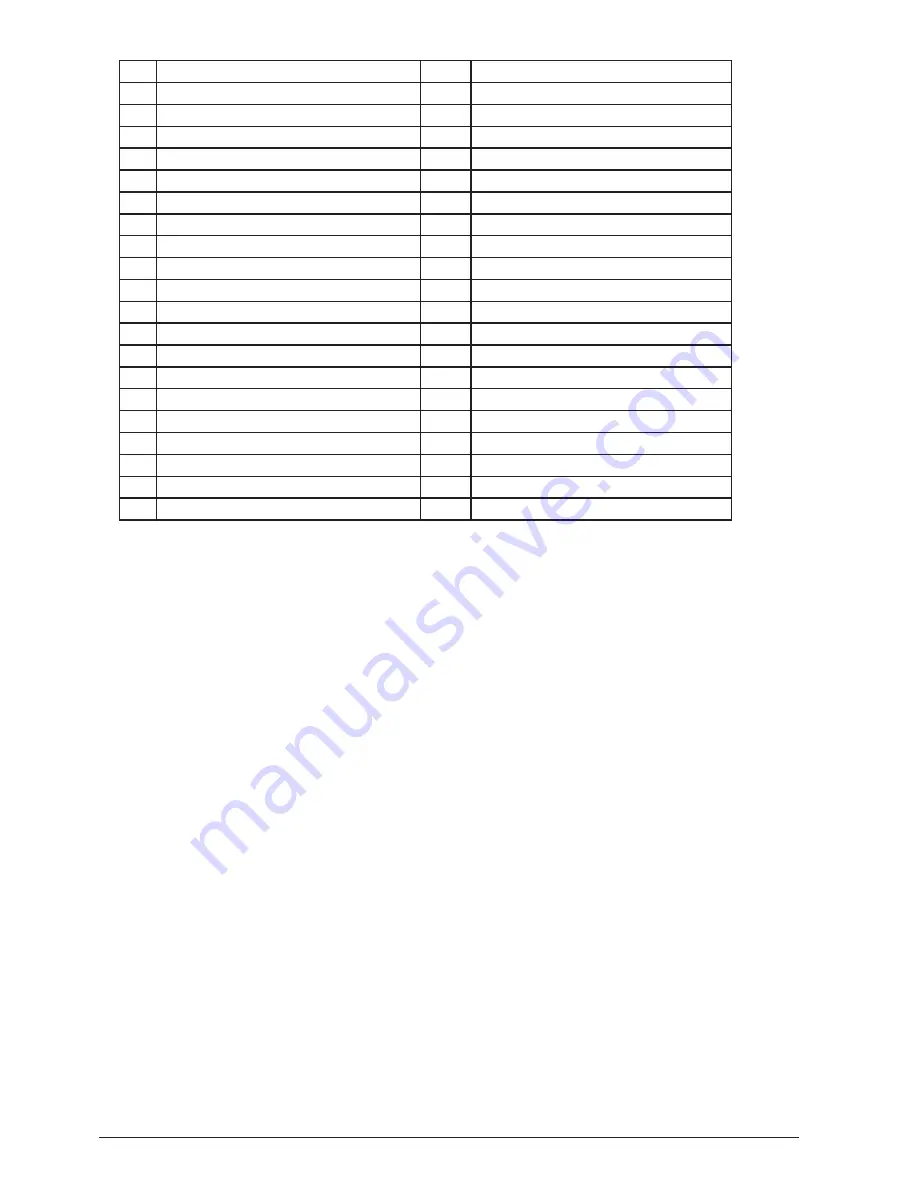
9
CHANGES AND T YPING ERRORS RESERVED
CHANGES AND T YPING ERRORS RESERVED
48
Handle
116
Center shaft
49
Sleeve fasten ring
117
Sleeve
50
Bearing 7206
e
118
Connect sheet
51
Bearing cover
119
Gear z33
52
O shape seal
120
Inner gear sheet
53
Oil cup
121
Connector
54
Taper head fasten screw
122
Key
55
Fixture sleeve
123
Gear z51
56
Key
124
Sleeve
57
Worm gear z28
125
Bearing 3056203
58
Sleeve
126
Gear z42
59
Small shaft
127
Fixture ring
60
Gear z17
128
Taper ring
61
Connection rod
129
Pin
62
Handle base
130
Arm
63
Handle ball
131
Shaft pin
64
Handle bar
132
Tape pin
65
Handle base
133
Handle
66
Pin
134
Spring
67
Elastic block ring
135
Steel ball
68
Washer
6. s
TrUcTUre
anD
aDjUsTmenT
The vertical column is mounted on the bottom base, loosen the fasten handle 63 ( fig.5 ) and rotate handle 17
( fig.2 ), the spindle box can move along the vertical column, loosen the fasten handle 63, the spindle box fixed
at any position, so to suit the different machining requirements, loosen cover nut 73 ( Fig.5 ) and rotate nut 72,
the swivel angle of the fasten handle can be adjusted and the tightness of the spindle box can also be changed,
when adjustment completes, fasten the cover nut.
The gear box is mounted on top of the spindle box, rotate the feed handle 89 ( Fig.5 ) the spindle will move up
and down along with the sleeve Remove the gear box, loosen the anti-motion washer 41 ( Fig.4 ), adjust nut 40,
the clea ance of the spindle bearing can be altered. The above adjustments have been set when put to shipment,
nonqualified personal is not allowed to de this adjustments.
7. T
ransmission
sysTem
The spindle rotate ( Fig. 6 ) through motor and gear 95;126 or 99;100 to shaft . Through gear 102; 123 or 108;119
to shaft. Through guide and transmission key to spindle. The motor has double- speed, through changing the
transmission gears, the spindle will rotate in 8 grades of speeds.
Spindle feed motion. The spindle feed movement is controlled manually, the handle 88 ( Fig.5 ) through gear,
gear rack transmission, to make the spindle sleeve move downwards so realise the feed motion.
The up and down motion of the spindle box. It is also controlled by hand, loosen the fasten handle 63 ( Fig. 5 ),
move handle 17 ( Fig.2 ), the spindle box will move up or down.
8. o
peraTion
Before start the motor, first rotate the change switch ( 21 ) on the spindle box till teach the required position (
high speed to “2R”, Low speed to “1R”, low speed and reverse direction to “1L” ) , then press down the start switch
“1” (green) ; for stop the machine press “O” button ( red ): for reverse rotation, fist to stop the machine and rotate
the speed change switch to “1L” or “2L” wait till the motor to stop completely and then press the start switch.
The speed selection is realised through handle 133 ( Fig.7 ), adjust handle 133 to realise 4 kinds of speed
variations, matched with double speed motor, we can gain 8 grades of speeds ranging from 100 rpm to 2900 rpm.
It should be noted that the speed variations could only be done when the machine has stopped so to avid any
possible damages to the gears and couplers.
About the drilling depth, you only need to adjust the nut 38 ( Fig.2 ) to the require dimension. The drill automatic
release applies to GB1443-85 (ISO 296-1974 ). Morse 3 outer taper with flat tail, its operation is 1:ke this: put out
the handle 48 ( Fig.4 ), rotate handle 88 ( Fig.5 ), then the sleeve will lead the drill to the highest position, the drill
end touches the enter shaft end so to be pushed out, then push 48 to its original position, install the tool.
Содержание HU 25 T
Страница 1: ...HU 25 T D R I L L I N G M M A C H I N E S...
Страница 5: ...5 CHANGES AND TYPING ERRORS RESERVED 5 Parts drawings and list Figure 1 Figure 2 Figure 3...
Страница 6: ...6 CHANGES AND TYPING ERRORS RESERVED Figure 4 Figure 5...
Страница 7: ...7 CHANGES AND TYPING ERRORS RESERVED Figure 6 Figure 7...
Страница 12: ...12 CHANGES AND TYPING ERRORS RESERVED...
Страница 13: ...13 CHANGES AND TYPING ERRORS RESERVED...
Страница 16: ...2014 V1...