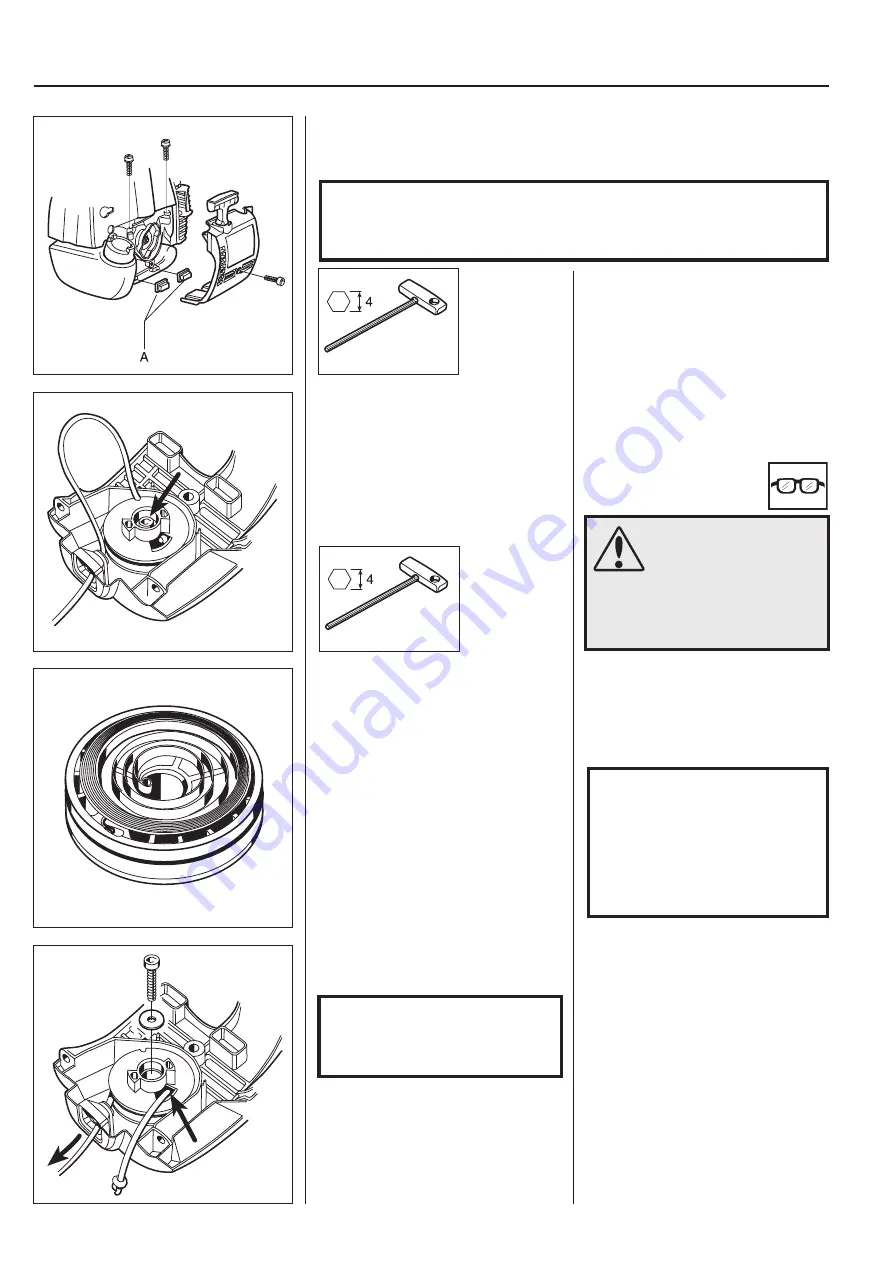
4
1
502 50 18-01
502 50 18-01
Starter
Dismantling
Remove the 3 screws and lift off the starter.
Offload the spring tension.
Remove the screw from the centre of
the starter pulley and lift off the starter
pulley.
Offload the spring tension.
Remove the screw in the centre of the
starter pulley. Carefully lift out the starter
pulley from the starter housing.
Assembly
Clean the component parts and
assemble in the reverse order as set out
for dismantling.
Assembly
Clean component parts before
assembling.
Replace the return spring/starter pulley
and starter cord, if necessary.
Assemble the starter pulley.
Assemble a new starter cord.
Lubricate the spindle with a little grease
and fit the starter pulley.
Position the washer and tighten the
screw.
Assemble a new starter cord. Slide it
into the starter pulley’s slot as
illustrated and then out through the
cord guide in the starter housing.
Make sure the knot on the end of the
cord is as small as possible!
NOTE!
The return spring and starter
pulley are supplied pre-
assembled and are fitted in the
starter housing as a single unit.
Exercise care when opening the
packaging so that the spring
does not fly out.
NOTE!
A new starter cord can be fitted
without the need of dismantling
the starter!
NOTE!
Ensure the bushings (A) that guide the starter towards the fuel tank are not
lost.
WARNING!
Wear protective glasses.
The return spring lies tensioned in
the starter and can fly out and
cause personal injury with
careless handling.
Содержание 326C, 326L, 326LX-Series, 326LDX-Series
Страница 1: ...Workshop manual 326R 326L 326C English ...
Страница 31: ...30 4 Centrifugal clutch ...
Страница 35: ...34 5 Angle gear ...
Страница 45: ...44 6 Cylinder and piston ...
Страница 51: ...50 7 Crankshaft and crankcase ...
Страница 55: ...2004W38 114 03 03 26 ...