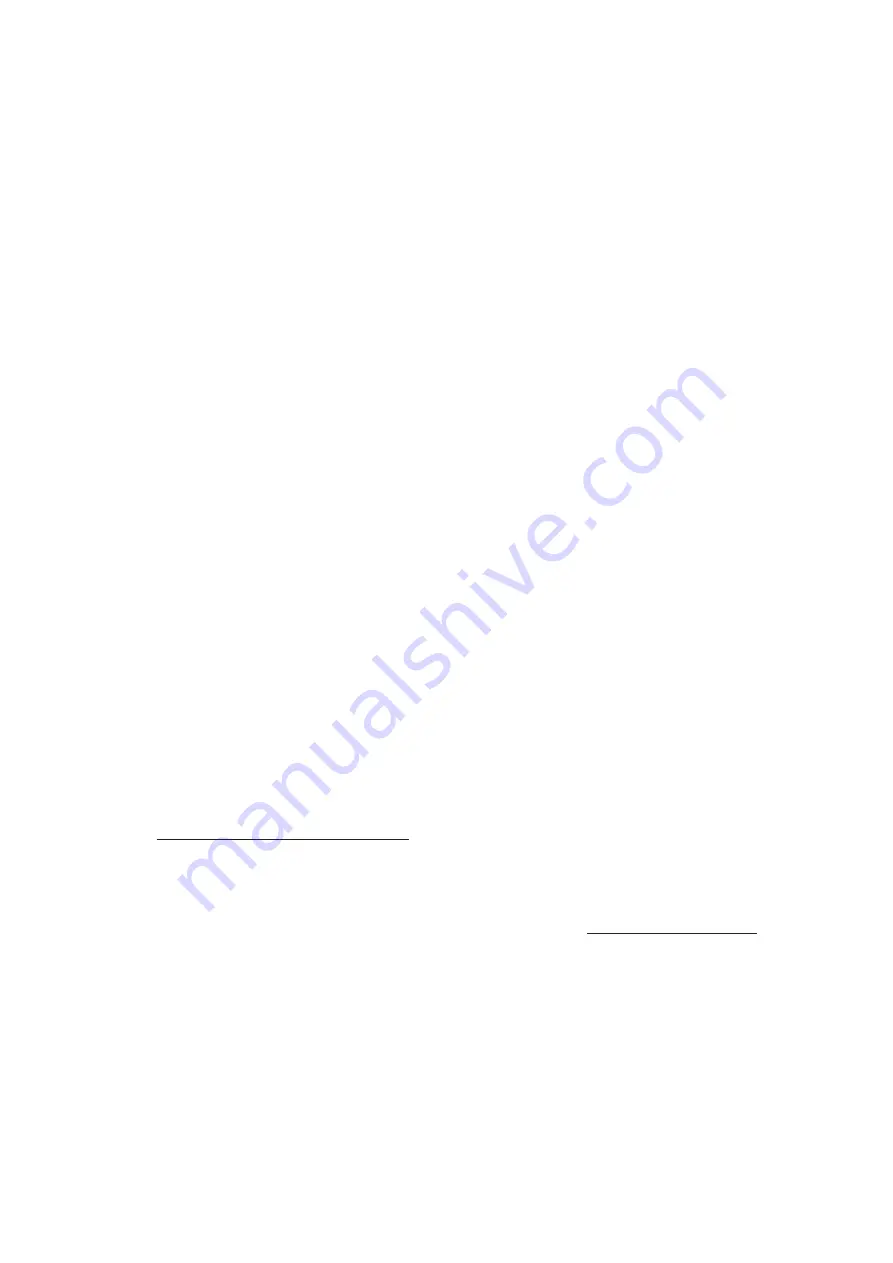
T: +44(0)161 430 6618
3
Emergency safety showers must be fed from a potable water supply – drinking water or water of a similar quality.
Minimum Supply Pressure: 2.8 Bar (40 PSI)
Maximum Supply Pressure: 6 Bar (87 PSI)
Where a high unregulated pressure is experienced, this must be monitored to ensure it does not exceed the recommended
maximum. If the water pressure exceeds the recommendations, please contact Hughes Safety Showers for advice.
The water supply pipe must be of a material compatible with the safety shower and/or eye/face wash equipment to avoid
corrosion.
The supply pipe should have at least the same diameter as the inlet pipe on the equipment.
If required, the supply pipe should be fitted with a non-return check valve.
Minimum flow rates must be in accordance with International and European standards, namely EN15154 or
ANSI Z358.1-2014.
Water inlet size: Please refer to your general arrangement drawing for details.
Good practice:
Fit isolation valves to the supply pipes in an accessible position for use during maintenance. These valves
should have locking mechanisms to prevent unauthorised shutoff and be labelled accordingly with fixed permanent tags.
Water supply and supply pipe materials
Operation
Employees working within hazardous areas must be trained in the use and location of emergency safety showers
or eye/face wash equipment. Instructions for all emergency equipment should be readily available and accessible
to personnel.
•
Pull lever activation
Maintenance
Regular servicing and maintenance of emergency safety shower and eye/face wash equipment is essential to ensure
correct functionality. All services and weekly activations must be recorded to ensure a full history is maintained as per
European and International standard requirements.
Weekly activation
All equipment should be visually inspected and activated at least once a week to ensure it is operating properly, to clear
the line of any sediment build up and check that the water runs clear.
Where fitted, the external test handle can be used for ease.
Please visit www.hughes-safety.com/weekly-activation to download the checklist and video detailing what to look out for to
remain compliant.
Servicing and cleaning
Hughes recommend equipment be serviced and cleaned regularly, and at least every 6 months. To discuss Hughes service
contract options or to purchase spare parts call us on +44 (0)161 430 6618 or email [email protected]
Periodic analysis of the water quality is recommended to ensure there is no build-up of harmful bacteria.
Regular cleaning of the outside of the emergency equipment is recommended. Abrasives or solvents must not be used to
clean the unit as this can damage the surface or affect the instruction stickers.
Safety showers:
•
Remove the shower head/nozzle periodically to clean, disinfect and ensure there is no build-up of debris or bacteria.
•
Remove the shower rose/nozzle and replace after flushing.
Electrical equipment:
•
Thorough visual inspections should be carried out to check for external damage to the electrical units, their cables
or the junction boxes. Should any part be found to be damaged, this must be reported and repaired or replaced
as soon as possible. A further test should be carried out to establish that it functions as intended. Any additional
electrical tests should be carried out at the discretion of a qualified electrician.