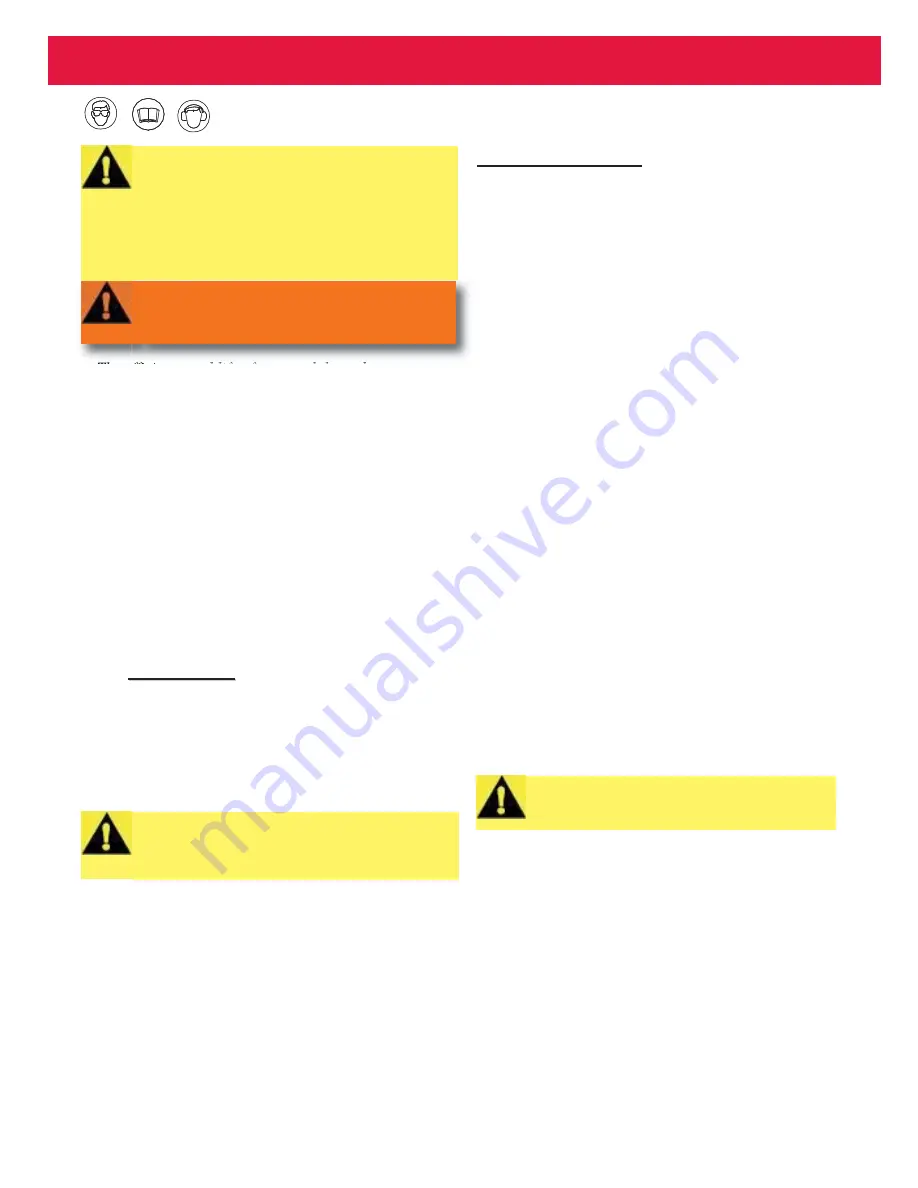
9
BTT35LS BOBTAIL Installation Tool
Alcoa Fastening Systems
M
M
AINTENANCE
AINTENANCE
•
The efficiency and life of your tool depends on proper
maintenance. Please read this section completely
before proceeding with maintenance and repair. Use
proper hand tools in a clean and well-lighted area.
Only standard hand tools are required in most cases.
Where a special tool is required, the description and
part number are given.
•
While clamping tool or parts in a vise, and when
parts require force, use suitable soft materials to
cushion impact. For example, using a half-inch brass
drift, wood block and vise with soft jaws greatly
reduces possibility of damaging tool. Remove compo-
nents in a straight line without bending, cocking or
undue force. Reassemble tool with the same care
.
Sealants, Lubricants, Service Kits
•
See
S
S
PECIFICATIONS
PECIFICATIONS
for fluid type. Dispose of fluid
in accordance with local environmental regulations.
Recycle steel, aluminum, and plastic parts in accor-
dance with local lawful and safe practices.
•
Rub Slic-Tite®* with PTFE thread compound, or
equivalent, on pipe plug threads and quick connect
fitting.
•
Smear LUBRIPLATE® 13OAA*, or equivalent lubri-
cant, on O-Rings and mating surfaces to aid assem-
bly and to prevent damage to O-Rings.
(LUBRIPLATE 13O-AA is available in a tube as
Huck P/N 502723.)
•
Each Service Kit contains perishable parts for your
specific tool. As foreseeable use may indicate, keep
extra kits (O-rings, Back-up Rings, other standard
items) and tool parts in stock. When stock is deplet-
ed, you can get kit items from any regular retailer of
these items. See kit parts list for: O-ring size
(AS568- number); material; durometer.
P
REVENTIVE
M
AINTENANCE
System Inspection
Operating efficiency of the tool is directly related to the
performance of the complete system, including the tool
with nose assembly, hydraulic hoses, trigger and con-
trol cord, and POWERIG. Therefore, an effective pre-
ventive maintenance program includes scheduled
inspections of the system to detect and correct minor
troubles. At the beginning of each shift/day:
• Inspect tool and nose assembly for external dam-
age.
• Verify that hydraulic hose fittings, couplings, and
electrical connections are secure.
• Inspect hydraulic hoses for damage and deteriora-
tion. Do not use hoses to carry tool. Replace hoses
if damaged.
• Observe tool, hoses, and hydraulic unit during oper-
ation to detect abnormal heating, leaks, or vibration.
• Max hydraulic fluid contamination level: NAS 1638
class 9, or ISO CODE 18/15, or SAE level 6.
POWERIG Maintenance
Maintenance instructions and repair procedures are
in the appropriate POWERIG Instruction Manual.
Tool Maintenance
Whenever disassembled and also at regular intervals
(depending on severity and length of use), replace all
seals, wipers, and back-up rings in tool. Service Kits,
hoses, and extra parts should be kept in stock.
Inspect cylinder bore, pistons, and piston rods for
scored surfaces and excessive wear or damage.
Replace as necessary.
Nose Assembly Maintenance
Clean nose assembly often. Dip in mineral spirits or
similar solvent to clean puller and wash away metal
chips and debris. At regular intervals, as experience
shows, disassemble nose and use a sharp "pick" to
remove imbedded particles from grooves of puller.
*
DEXRON is a registered trademark of General Motors Corp.
Quintolubric is a registered trademark of Quaker Chemical Corp.
Slic-Tite is a registered trademark of LA-CO Industries, Inc.
TEFLON is a registered trademark of DuPont Corp.
LUBRIPLATE is a registered trademark of Fiske Brothers
Refining Co.
WARNING: Inspect tool for damage or
wear before each use. Do not operate if
damaged or worn, as severe personal
injury may occur.
CAUTIONS:
- Consult MSDS before servicing tool.
- Keep dirt and other material out of
hydraulic system.
- Separated parts most be kept away from
dirty work surfaces.
- Dirt/debris in hydraulic fluid causes failure
in POWERIG® Hydraulic Unit’s valves.
CAUTION: Do not use TEFLON
®
* tape on pipe
threads. Pipe threads may cause tape to shred
resulting in tool malfunction. (Slic-Tite
®
* is
available in stick form as Huck P/N 503237.)
CAUTION: Always replace seals, wipers,
and back-up rings when tool is disassem-
bled for any reason.