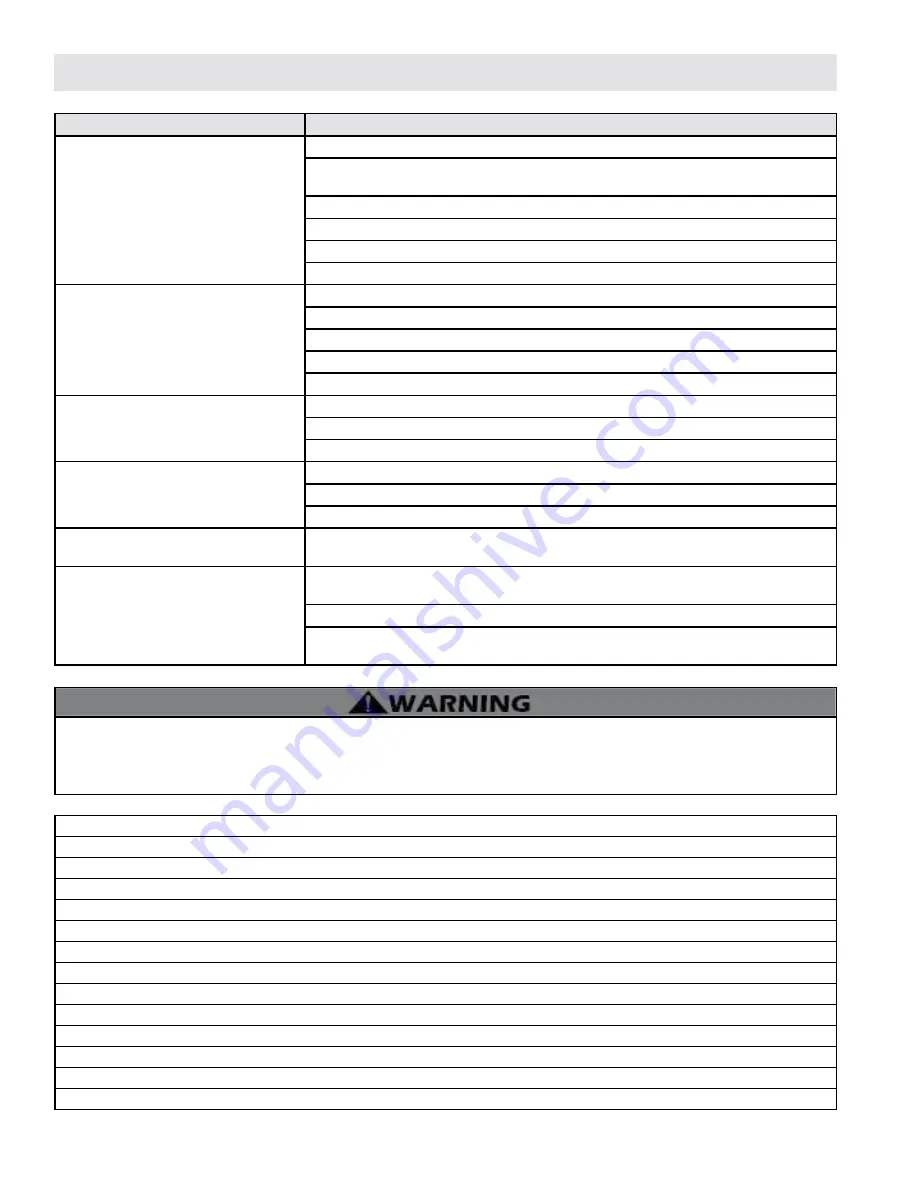
LP-447 Rev. 7.7.17
8
Part 5 - Troubleshooting
To save time and money, review the following initial diagnostic steps before calling for service.
Problem
Possible Solution
Burner Does Not Ignite
Make sure the the appliance is turned ON
If the control panel display is blank, ensure the power cord is intact. Check the circuit breaker
or fuse box. Ensure the appliance fuses are good.
Make sure that the appliance is supplied with and full of water
Make sure the cold and hot water lines are not plumbed in reverse
Make sure the water inlet and outlet and gas supply lines are open
Make sure the water lines are not frozen
Water Is Not Hot Enough
(VWH Models or Systems with Indirect
Water Heaters)
Make sure the temperature setting on the appliance / indirect water heater is not too low
Make sure any water supply line filtration devices are not clogged with debris
Make sure the appliance is connected to the correct gas supply
Check that supply and manifold gas pressures are in accordance with specifications
Make sure that water temperature sensor wires are intact and properly connected
Water is Too Hot
(VWH Models)
Make sure the temperature setting is not too hot on the appliance or indirect water heater
Make sure any filters in the cold water supply line are not clogged with debris
Make sure the appliance is connected to the correct gas supply
Hot Water Temperature Fluctuates
(VWH Models)
Make sure any filters in the cold water supply line are not clogged with debris
Make sure the appliance is connected to the correct gas supply
Make sure the supply gas pressure is sufficient
Blower Continues to Operate After
Combustion Stops
This is normal. The blower operates for one minute after combustion has stopped to vent the
remaining exhaust gas from the flue.
Appliance Makes Abnormal Sounds
During Operation
There is a leak of combustion gas between the sealed chamber and exhaust tube inside the
unit.
Make sure the venting installation complies with the installation manual.
Make sure supply gas pressure is sufficient. Insufficient gas pressure will cause unstable burn-
er flame and noise.
Table 2 - Troubleshooting Chart
This appliance is equipped with a control system that will shut down and lock the appliance out if certain operating conditions occur. If the
appliance locks out, turn off the gas valve at the manual shutoff. Check the vent terminations for obstructions. If no obstructions are found,
call a qualified service technician or the gas supplier to check the appliance. Failure to follow these instructions could result in property
damage, personal injury, or death.
Maintenance Notes