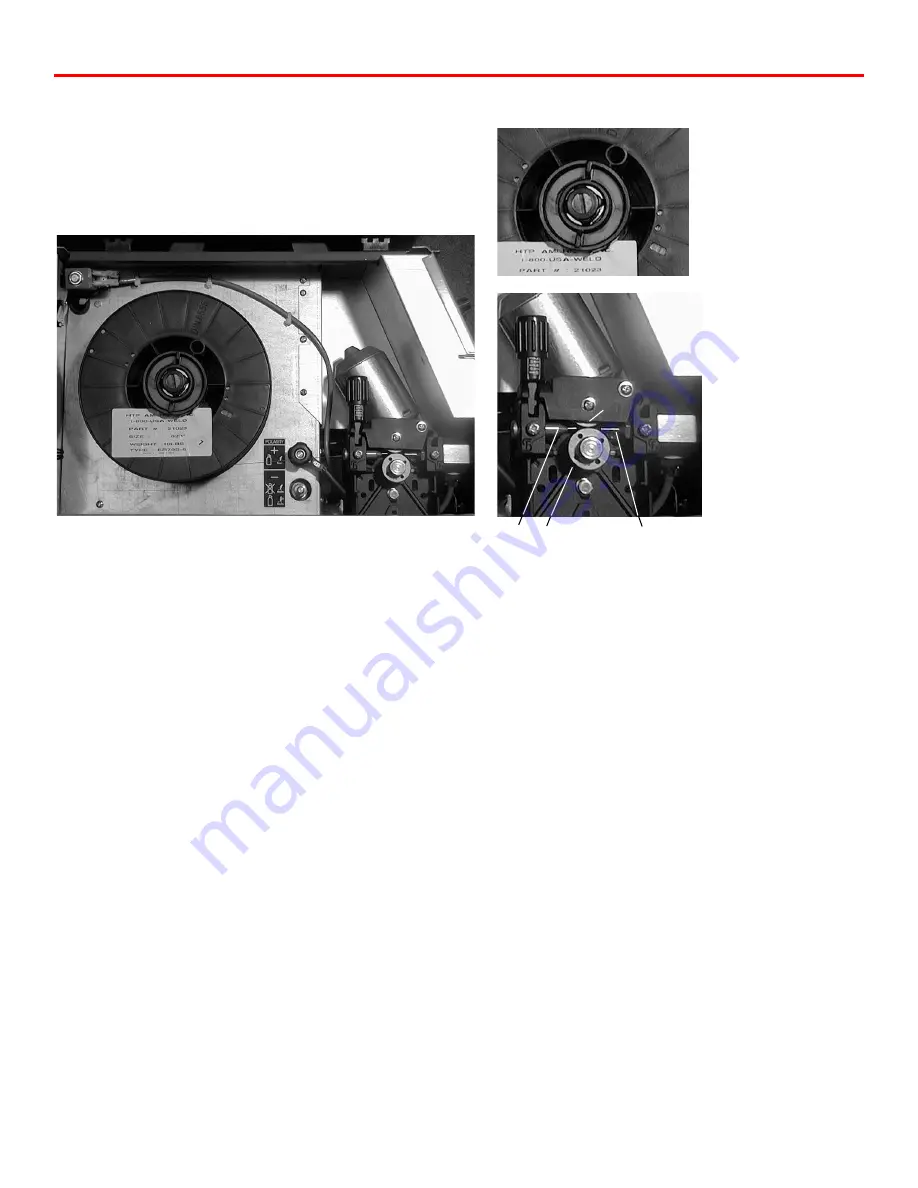
7
1. Your MTS 160 is designed to use standard 8" diameter 10 lb
spools of welding wire. Remove the spool retaining nut (A)
from the wire drive brake. Place the wire on the spool holder
so it unravels from the bottom. Install the spool retaining nut
(A) and tighten.
2. Loosen the wire from the spool. Be extremely careful not to
let the end of the wire go. Cut off the bent end of the wire to
expose a piece of straight wire.
3. Swing the pressure release handle (1) down, and the pressure
roller assembly (3) will swing up and out of the way.
4. Install the guide tube (8), which is taped to the bottom of the
machine into the adapter block though the front of the
adapter block. See figure 2 page 6.
5. Feed the wire into the inlet wire guide (4), across the drive
roll (5), and into the guide tube (8). (At this time it is a good
idea to check that the drive roll is set to the correct groove
for the wire size you are using. If not, see Changing the
Drive Roll.) Continue to feed the wire into the guide tube
until two or three inches of straight wire protrudes from the
front of the central adapter block. Note that the drive roller
is designed to "float" on the shaft of the wire drive motor.
6. Swing the pressure roller assembly (3) back into position.
Make sure that the wire is positioned in the groove of the
drive roll (5). Unscrew the pressure release handle (1) until
most of the pressure on the pressure roller has been released.
7. Remove the contact tip and gas nozzle from the welding gun.
Turn the wire feed rate to 6. Depress the trigger on the
welding gun. At this point, the wire feed should not be
consistent because there is not enough pressure on the
pressure roller. Slowly tighten the pressure roller adjusting
screw until the wire feeds evenly without slipping. Then
tighten an additional 1/4 turn for steel. No additional
tightening is necessary for aluminum. DO NOT
OVERTIGHTEN!
Continue feeding the wire until it appears at the tip of the
welding gun. Check your wire size and install the correct
contact tip. Install the gas nozzle.
8. Next, the tension on the wire drive brake must be set
correctly. The wire drive brake keeps the spool of wire from
continuing to rotate after we have stopped welding. In the
center of the spool holder is a square plastic bolt (B) with
a slot for a large screwdriver. This plastic bolt puts tension
on a spring, which in turn puts tension on the shaft, acting
as a brake for the spool of wire. Set the wire feed rate to
maximum, adjust the tension on the wire drive brake so the
spool will continue to rotate 1/8 to 1/4 turn after you have
released the trigger. This can be adjusted by hand if the
spool retaining nut (A) is removed.
9. Bend the welding wire 90 degrees and hold the welding gun
perpendicular to a non-conductive surface (concrete floor) so
the wire will not feed. While looking at the wire feed
mechanism, momentarily depress the trigger. The drive roll
should slip and act as a clutching mechanism. If not, the
drive roll will push the wire out between the roller and the
guide tube. This is known as “bird nesting”. If bird nesting
occurs, the pressure roller has been adjusted too tightly.
When properly adjusted, the drive roll will slip, and “bird
nesting” will never occur.
Figure 4
Figure 6
Wire Drive
1) Pressure Release Handle
2) Drive Motor
3) Pressure Roller Assy
4) Inlet Wire Guide
5) Drive Roller
6) Drive Roller
Retaining Screw
7) Pressure Roller
8) Guide Tube
Figure 5
Spool Holder
A) Spool Retaining Nut
B) Drive Brake Tensioner
Feeding the Welding Wire
(See Fig. 4, 5, 6)
A
B
1
2
3
5
8
6
4
7
Содержание MTS 160
Страница 21: ...21 Wiring Diagram MTS 160...
Страница 22: ...Parts Breakdown MTS 160 22...