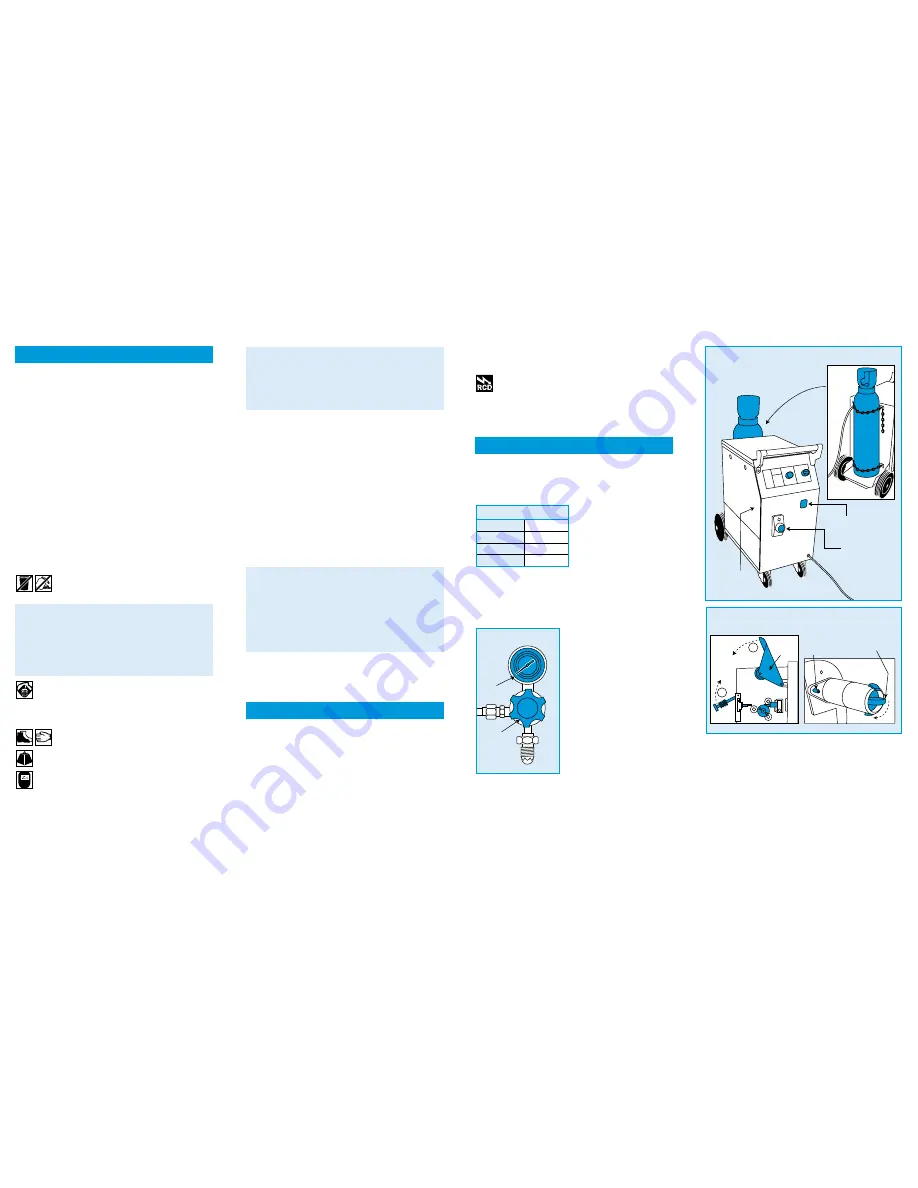
For advice
on the safety and suitability of this equipment
contact your local HSS Hire Weld Depot.
There is a serious risk of personal injury if you do
not follow all instructions laid down in this guide.
The hirer has a responsibility to ensure that all
necessary risk assessments have been completed
prior to the use of this equipment.
Most welding tasks may be considered as hot work
in site situations and may be subject to specific
permits to work.
This equipment should only be used by an operator
who has been deemed competent to do so by
his/her employer.
This equipment should be used by an able bodied,
competent adult
who has read and understood these
instructions. Anyone with either a temporary or permanent
disability, should seek expert advice before using it.
Keep children, animals and bystanders away from
the work area. Cordon off a NO GO area using
cones and either barriers or tape, available for hire
from your local HSS Hire Weld Depot.
Welding screens are also available for hire from
your local HSS Hire Weld Depot.
Never use this equipment if you are ill,
feeling tired, or under the influence of
alcohol or drugs.
Fumes produced by the welding process, if
inhaled, can be harmful to health.
A suitable
mask must be worn when using this equipment.
Respiratory protective equipment is available for
hire
, contact your local HSS Hire Weld Depot for details.
Skin must be covered – wear practical,
protective clothing, gloves and footwear.
This equipment is heavy
(54kg),
never attempt
to lift it on your own, always get help.
A head shield with an 11 EW shade MUST be
worn by anyone in the work area – goggles
are not suitable.
Avoid loose garments and jewellery
that could interfere with the work.
If the headshield or lens becomes damaged, return
it to your local HSS Hire Weld Depot.
Never use welding equipment near computers or
any sensitive electronic equipment.
Warning
If you are wearing an electronic life support
device (a heart pacemaker) you must consult
your doctor before going near or working with
this equipment. Magnetic fields associated with
high currents may affect these devices.
GENERAL SAFETY
Always transport, store and operate the machine
in an upright position.
Keep the power unit’s air vents clear of all
obstructions.
Always switch equipment OFF before making any
adjustments to it. Never leave it switched ON and
unattended.
Ensure the work area is well lit and ventilated,
a
fume extractor or smoke eliminator should be used. If in
doubt, ask about lighting and ventilation equipment at
your local HSS Hire Weld Depot.
Do not work near flammable gases or liquids,
petrol
or paint thinner fumes for example
. Keep combustible
materials at a safe distance -
at least 5m.
Make sure you know how to switch this machine
OFF before you switch it ON
in case you get into
difficulty.
Check the condition of the equipment before use.
If it shows signs of damage or excessive wear, return it to
your local HSS Hire Weld Depot.
COSHH information sheets are available from your local
HSS Hire Weld Depot.
This equipment must only be powered from a
16amp 240V supply, either by use of a 16amp
240V socket or by wiring direct to a 240V circuit,
protected by a 16amp fuse. All mains connections
may only be made by a qualified electrician.
If the equipment fails, or if its power supply cable
or plug becomes damaged, return it.
Never try to
repair it yourself.
Keep cables out of harm’s way,
and clear of the
work area
.
Extension leads should be fully unwound and
loosely coiled, away from the equipment.
Never run
them through water, over sharp edges or where they
could trip someone.
ELECTRICAL SAFETY
Vehicle Safety
Before carrying out welding work on cars/lorries
and similar vehicles...
Remove the vehicle’s battery and disconnect the
alternator.
Remove all combustible material and other
fire/explosion hazards.
Let It Cool
Handle welding equipment and work with care
– it will be hot. Leave equipment to cool before
changing welding rods, moving earth clamps,
and so on.
Keep the equipment dry, using electrical
equipment in very damp or wet conditions can be
dangerous.
To reduce the risk of electric shock, always use
a suitable RCD
(Residual Current
-
Operated Device)
available from your local HSS Hireweld Depot. Or power
the equipment from a mains circuit with a built in RCD.
Ensure the welder and the power socket are
switched OFF before plugging into the power
supply.
This guide is designed to help the user to safely set
up and dismantle the welder. It is not intended as
a guide to welding techniques as it is assumed
that the user already has the necessary
training/knowledge and experience.
It is important that the
equipments duty cycle is
taken into consideration
when in use.
Place the unit on a
suitable surface and
make sure that there is a
minimum of 200mm
clearance around the unit to allow a good
circulation of air.
DO NOT use the unit in the rain or in extremely
damp environments.
Ensure that the unit is switched OFF and isolated
from the power supply.
Connect the argon gas
supply hose to the
regulator then fit the
regulator to the argon
cylinder and secure with
the spanner supplied.
Attach the MIG torch to the
connection socket on the
units’ front panel. Simply
align the pipes and pins,
insert and lock in place by
turning the collar
clockwise.
Remove the wire feed
compartment cover.
Remove the welding guns
shield and tip, pull through
any remaining wire and remove any empty roll.
Place a new roll of wire onto the spool holder
making sure that the wire is fed from the bottom of the roll.
Ensure the brake location pin fits correctly to the
wire roll. Turn the spool holder securing cap by 90°
to retain the wire roll.
You must now switch the welder ON.
GETTING STARTED
Pull approximately 150mm of wire from the roll
ensuring you DO NOT let go of the wire
(as the wire
will spring loose).
Snip the end of the wire to leave a
straight leading piece.
Feed the wire through the wire feed roller and into
the guide. Close the tensioning roller and set the
tension. Feed the wire through to the gun until
25mm of wire is exposed then re-fit the tip.
The welder offers a range of different settings to
suit the type of welding task being performed.
Work through the following list of options selecting the
settings best suited to the work.
Duty Cycle
150A
14%
90A
35%
75A
60%
60A
100%
Wire Feed
Compartment
Cover
Torch
Connection
Socket
ON / OFF
Switch
Argon
Cylinder
Spool Location
Securing Cap
Brake
Location Pin
2
1
Tension
Roller
Wire Feed Unit
180amp MIG Welder
Gauge
Adjuster
Gas Regulator