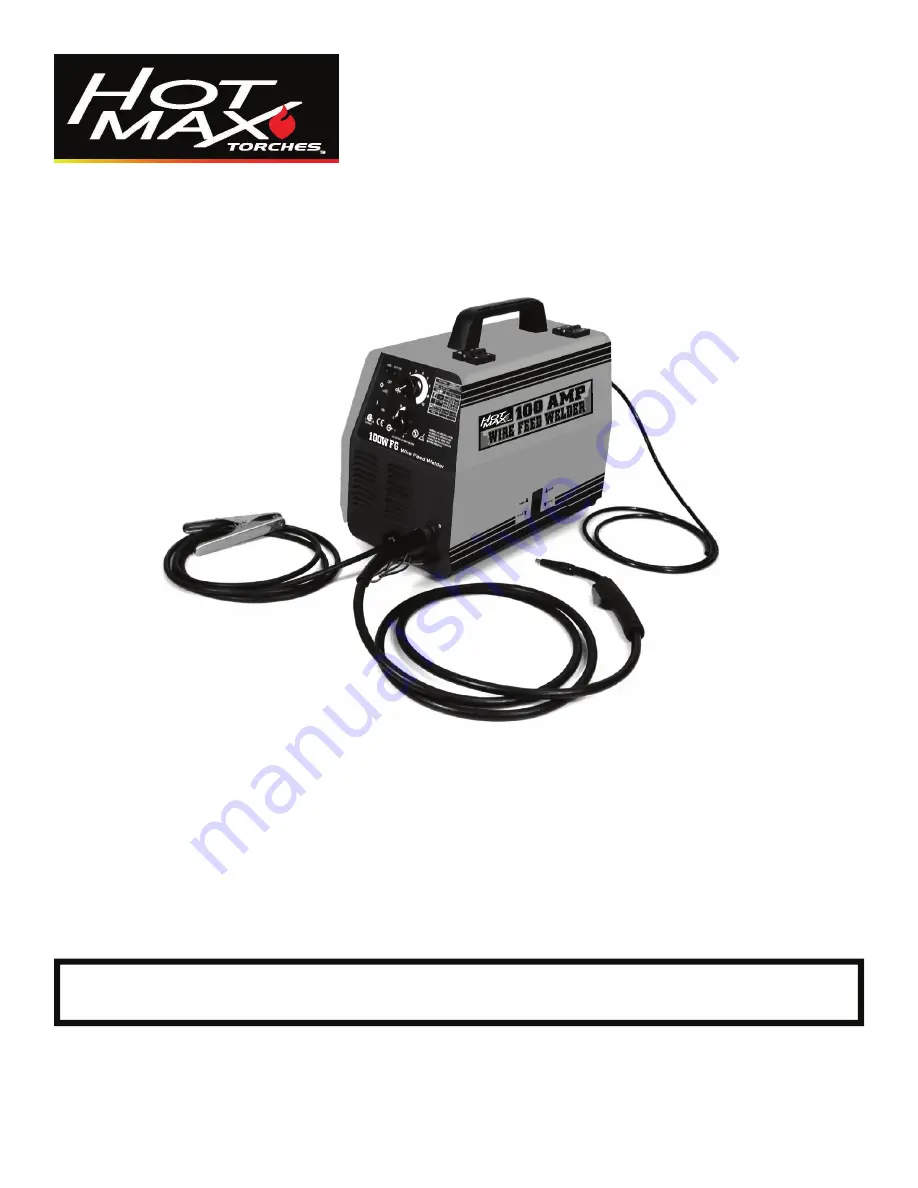
WARNING: Do not assemble, install, or operate this equipment without reading ALL of this manual
and the safety precautions and warnings illustrated in this manual.
KDAR
Company
Tel: 866-939-9013
15009
Manchester
Road
#283
Fax:
636-922-4622
Ballwin, MO 63011
Web Site: www.hotmaxtorches.com
Operator’s Manual
Models 100/135/175WFG
Wire Feed Welders
MIG Welders