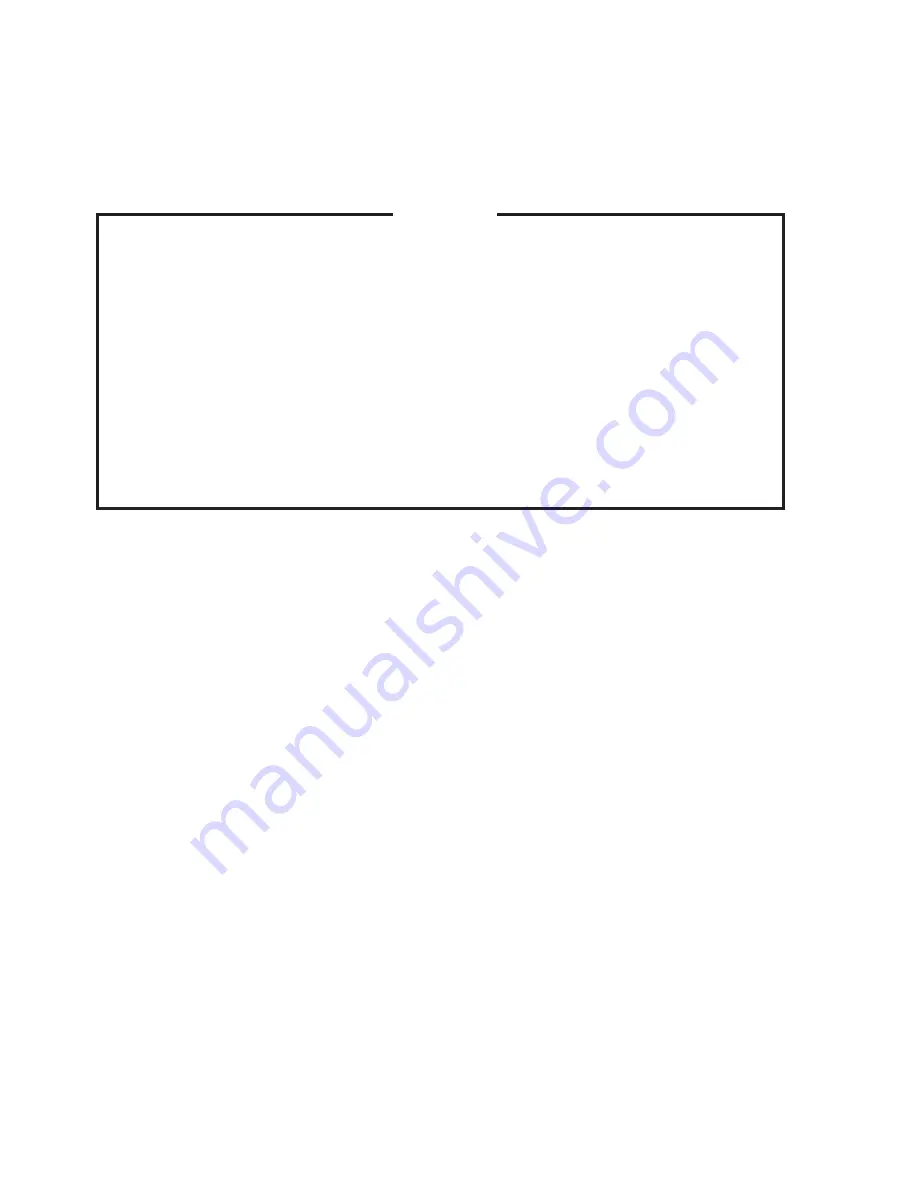
1
C. Control Board
• A HOSHIZAKI exclusive solid-state control is employed in the KMS-750MLH Modular
Crescent Cuber.
• All models are pretested and factory-adjusted.
CAUTION
1. Fragile, handle very carefully.
. A control board contains integrated circuits, which are susceptible to failure
due to static discharge. It is especially important to touch the metal part of
the unit when handling or replacing the board.
3. Do not touch the electronic devices on the board or the back of the board to
prevent damage to the board.
4. Do not change wiring and connections. Do not misconnect K3, K4 and K5,
because the same connector is used for the thermistor, mechanical bin
control and float switch.
5. Always replace the whole board assembly if it goes bad.
6. Do not short out power supply to test for voltage.