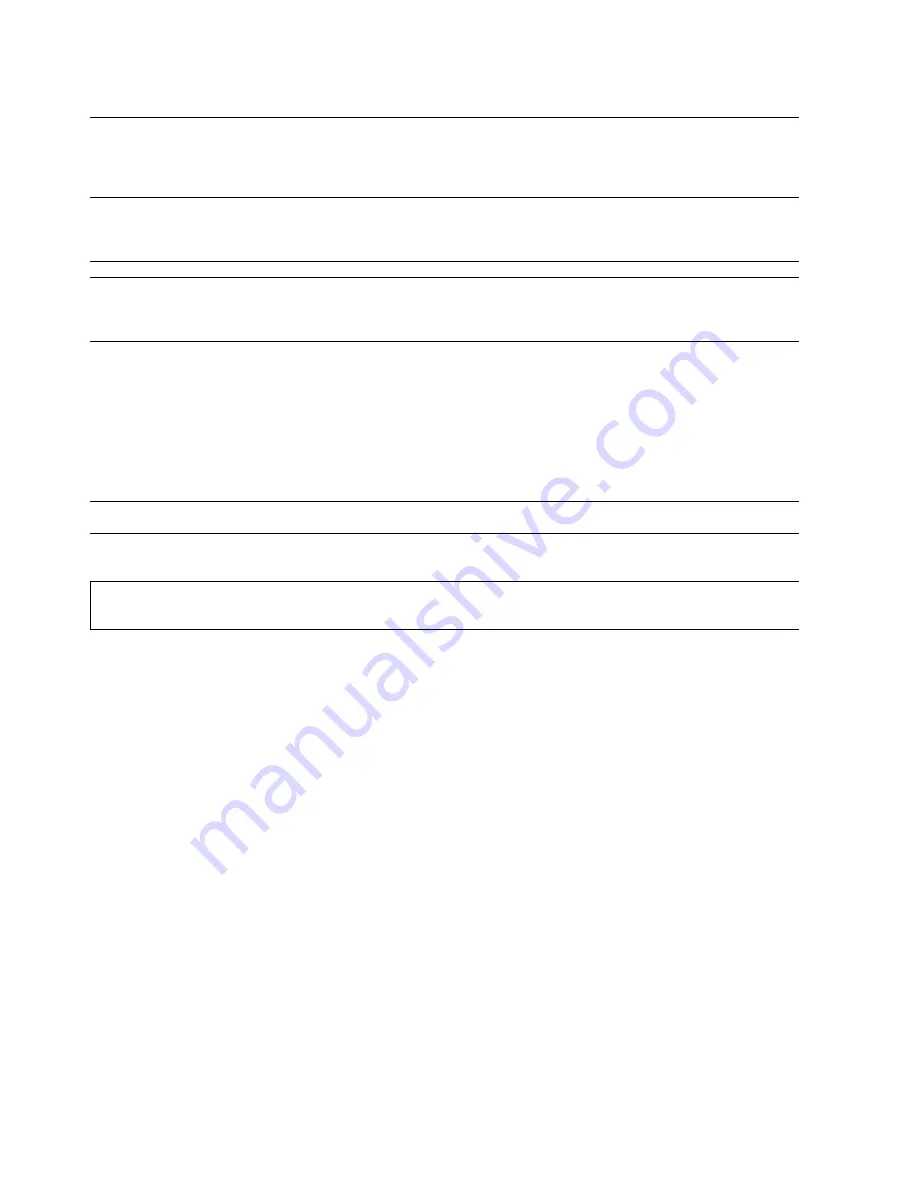
54
3. SRK-20J
Specification Sheet
AC SUPPLY VOLTAGE
208-230/60/1 ( 3 wire with neutral for 115V )
(115VAC Supplied to KMS via Factory Wire Harness)
AMPERAGE
23.3 A ( 5 Min. Freeze AT 104°F / WT 80°F )
MINIMUM CIRCUIT AMPACITY
30 A
MAXIMUM FUSE SIZE
30 A
EXTERIOR DIMENSIONS (WxDxH)
59-3/4" x 17" x 30" (1518 x 432 x 762 mm)
DIMENSIONS INCLUDING LEGS (WxDxH)
62" x 21" x 45" (1575 x 533 x 1142 mm)
SHIPPING DIMENSIONS (LxWxH)
64" x 22-1/8" x 34-3/8" (1626 x 562 x 873 mm)
EXTERIOR FINISH
Galvanized steel
WEIGHT
Net 280 lbs. (127 kg), Shipping 325 lbs. (147 kg)
CONNECTIONS - ELECTRIC
Main Power Supply: Permanent Connection
SRK to KMS: Wire Harness Connection
- REFRIGERATION
Suction line - 3/4" Brazed Connections
CIRCUIT
Liquid line - 1/2" Brazed Connections
COMPRESSOR
Hermetic, Model CS24K6E-PFV
CONDENSER
Air Cooled, Fin and Tube Type
COMPRESSOR PROTECTION
Auto-Reset Overload Protector (Internal)
FAN MOTOR PROTECTION
Thermal Protection
REFRIGERANT CIRCUIT PROTECTION
Auto-Reset High-Pressure Switch
REFRIGERANT CONTROL
Condensing Pressure Regulator
REFRIGERANT CHARGE
TOTAL R404A, 27 lb. 5.4 oz. (12400g)
ICEMAKER, 0 lb. 7.1 oz. (200g)
CONDENSER, 26 lb. 14.3 oz. (12200g)
DESIGN PRESSURE
High 467 PSIG, Low 230 PSIG
OPERATING CONDITIONS
VOLTAGE RANGE
187-253VAC
AMBIENT TEMP. (Outdoor use)
-20-122°F
ACCESSORIES -SUPPLIED
Legs and hardware
-REQUIRED
Compatible KMS-2000MLJ icemaker
Line set HS-0243, HS-0244, HS-0245
TOTAL HEAT OF REJECTION FROM CONDENSER
31,200 BTU/h [AT 90ºF (32ºC) / WT 70ºF (21ºC)]
TOTAL HEAT OF REJECTION FROM COMPRESSOR
4,300 BTU/h [AT 90ºF (32ºC) / WT 70ºF (21ºC)]
CONDENSER VOLUME
964 CU. IN.
ENG.F-032.1.0205