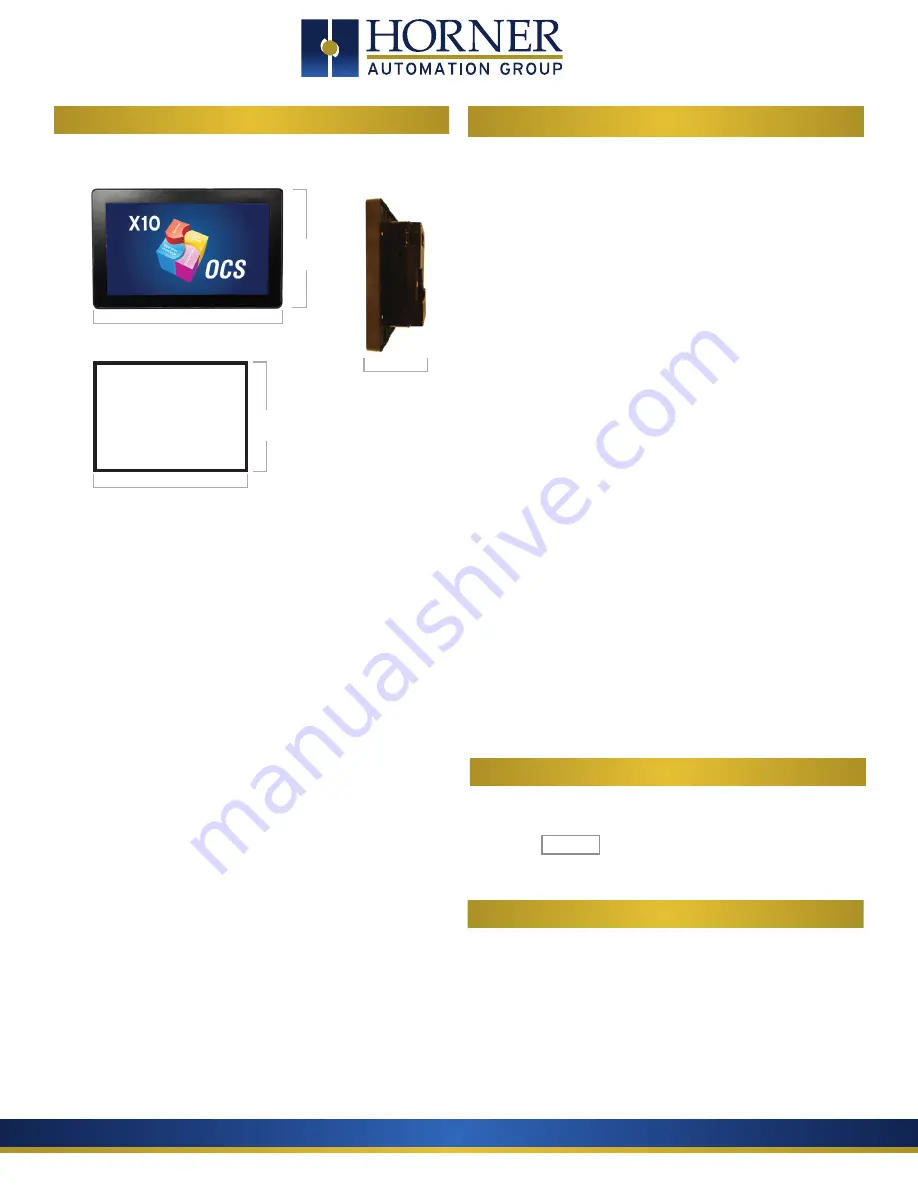
5/17/2022 | MAN1278-03-EN
Indianapolis, USA | Cork, Ireland | Calgary, Canada | Bangalore, India | Oakleigh, Australia | Tianjin, China | Esteio, Brazil
Please visit our website for a complete listing and to learn more about certified Horner Automation products.
This document is the property of Horner Automation Group, and is subject to change.
page 8 of 8
8.1 - WARNINGS
1.
WARNING
- Do not disconnect while circuit is live unless area is known to be non-hazardous.
AVERTISSEMENT
- Ne pas déconnecter pendant que le circuit est sous tension à moins que
la zone ne soit connue pour être non dangereuse.
2. WARNING - EXPLOSION HAZARD
- Do not disconnect
equipment unless power has been
removed or the area is known to be non-hazardous.
AVERTISSEMENT - RISQUE D’EXPLOSION
- Ne déconnectez pas l’équipement à moins que
l’alimentation n’ait été coupée ou que la zone soit réputée non dangereuse.
3.
To avoid the risk of electric shock or burns, always connect the safety (or earth) ground
before making any other connections.
4.
To reduce the risk of fire, electrical shock, or physical injury, it is strongly recommended to
fuse the voltage measurement inputs. Be sure to locate fuses as close to the source
as
possible.
5.
Replace fuse with the same type and rating to provide protection against risk of fire and
shock hazards.
6.
In the event of repeated failure, do NOT replace the fuse again as repeated failure indicates
a defective condition that will NOT clear by replacing the fuse.
7.
Only qualified electrical personnel familiar with the construction and operation of this
equipment and the hazards involved should install, adjust, operate, or service this equipment.
Read and understand this manual and other applicable manuals in their entirety before
proceeding. Failure to observe this precaution could result in severe bodily injury or loss of
life.
8.
If the equipment is used in a manner not specified by Horner APG, the protection provided by
the equipment may be impaired.
8.2 - FCC COMPLIANCE
This device complies with Part 15 of the FCC Rules. Operation is subject to the following
two conditions:
1.
This device may not cause harmful interference
2.
This device must accept any interference received, including interference that may cause
undesired operation
8.3 - PRECAUTIONS
All applicable codes and standards need to be followed in the installation of this product. Adhere
to the following safety precautions whenever any type of connection is made to the module:
1.
Connect the safety (earth) ground on the power connector first before making any other
connections.
2.
When connecting to the electric circuits or pulse-initiating equipment, open their related
breakers.
3.
Do NOT make connection to live power lines.
4.
Make connections to the module first; then connect to the circuit to be monitored.
5.
Route power wires in a safe manner in accordance with good practice and local codes.
6.
Wear proper personal protective equipment including safety glasses and insulated gloves
when making connections to power circuits.
7.
Ensure hands, shoes, and floor are dry before making any connection to a power line.
8.
Make sure the unit is turned OFF before making connection to terminals.
9.
Make sure all circuits are de-energized before making connections.
10.
Before each use, inspect all cables for breaks or cracks in the insulation. Replace immediately
if defective.
11.
Use copper conductors in Field Wiring only, 60/75°C.
12.
Use caution when connecting controllers to PCs via serial or USB. PCs and laptops may use
“floating power supplies” that are ungrounded which could cause a damaging voltage
potential between the laptop and controller. Ensure the controller and laptop are grounded
for maximum protection. Consider using a USB isolator due to voltage potential differences
as a preventative measure.
8 SAFETY
7.2 - Installation Procedure
This equipment is panel mounted and is meant to be installed in an
enclosure suitable for the environment, such that the back of the
equipment is only accessible with the use of a tool.
This equipment is suitable for use in Class I, Division 2, Groups A, B, C and
D; Class II, Division 2 Groups F and G; and Class III Hazardous Locations
or Non-Hazardous Locations only.
The X10 utilizes a clip installation method to ensure a robust and
watertight seal to the enclosure. Follow the steps below for the proper
installation and operation of the unit.
1.
Carefully locate an appropriate place to mount the X10. Be sure to
leave enough room at the top of the unit for insertion and removal
of the microSD™ card.
2.
Carefully cut the host panel per the diagram, creating a 175mm x
131.9mm (with a tolerance of +/- 1.0mm) opening into which the
X10 is to be installed. If the opening is too large, water may leak into
the enclosure, potentially damaging the unit. If the opening is too
small, the OCS may not fit through the hole without damage.
3.
Remove any burrs/sharp edges and ensure the panel is not warped
in the cutting process.
4.
Install and tighten the four mounting clips (provided in the box)
until the gasket forms a tight seal. For standard composite mounting
clips (included with product).
NOTE: Torque Rating is 2-3 in-lbs (0.23-
0.34 Nm).
For optional metal mounting clips, use a torque rating of
4-8 in-lbs (0.45-0.90 Nm).
5.
Connect communications cables to the serial port, USB ports, and
CAN port as required.
model
9 PART NUMBER BUILDER
GLOBAL MODEL NUMBERS
HE-X10
R
relay and solid state outputs
A
solid state output
10 TECHNICAL SUPPORT
For assistance and manual updates, contact Technical Support at the
following locations:
North America
Europe
(317) 916-4274
(+) 353-21-4321-266
www.hornerautomation.com www.hornerautomation.eu
[email protected]
7 DIMENSIONS & INSTALLATION
7.1 Dimensions & Panel Cutout
Panel Cutout
6.89” (175mm)
5.19”
131.9mm
6.61”
(167.8mm)
10.44” (265.2mm)
2.17” (55.1mm)
Panel Tolerance: +/- 1.0mm