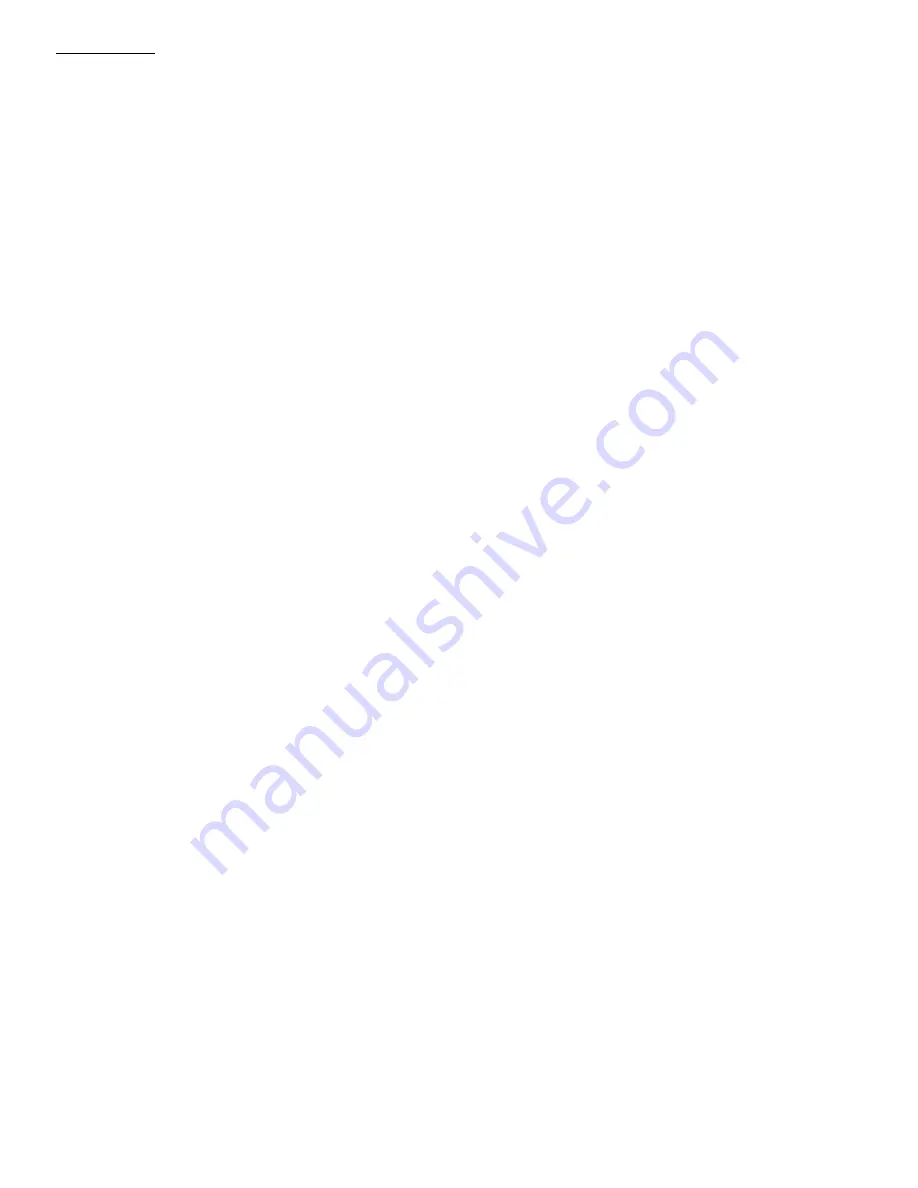
16
NOTE: Some burners continue to purge the oil lines
between the valve(s) and nozzle(s) even though the
fuel valve(s) is (are) closed. Termination of the firing
cycle rather than opening the master switch will allow
purging of the combustion chamber, if available. This
will reduce a buildup of fuel vapors in the combustion
chamber caused by oil line purging.
If the Flame Indicator LED remains on for more than
four seconds after the flame disappears, the photocell is
sensing hot refractory.
If the detector is sensing hot refractory, add an orifice
plate in front of the cell to restrict the viewing area of the
detector or resight the detector to a more distant, cooler
part of the combustion chamber.
NOTE: If the detector is resighted, the flame must still be
properly sighted.
Continue adjustment until hot refractory hold-in is
eliminated.
ULTRAVIOLET RESPONSE TESTS
(All Ultraviolet Detectors)
Ignition Spark Response Test
Make sure that ignition spark is not causing the Flame
Indicator LED to come on.
1. Close the pilot and main fuel manual shutoff valves.
2. Start the burner and run through the ignition period.
Ignition spark should occur but the Flame Indicator LED
must not come on.
3. If the Flame Indicator LED does come on, resight the
detector farther out from the spark. Measure the flame cur-
rent. It should not be more than one-fourth microampere.
NOTE: The Honeywell Q624A Solid State Spark Gen-
erator will prevent detection of ignition spark when
properly applied with the C7027, C7035, or C7044
Minipeeper Ultraviolet Flame Detectors. The Q624A is
for use only with gas pilots.
RESPONSE TO OTHER ULTRAVIOLET SOURCES
Some sources of artificial light produce small amounts
of ultraviolet radiation. Under certain conditions, an ul-
traviolet detector may respond to them as if it were detect-
ing flame. DO NOT USE AN ARTIFICIAL LIGHT
SOURCE TO CHECK THE RESPONSE OF AN
ULTRAVIOLET DETECTOR.
FLAME SIGNAL WITH HOT COMBUSTION
CHAMBER (All Installations)
With all initial tests and burner adjustments com-
pleted, operate the burner until it is at maximum expected
temperature. (Observe the burner manufacturer warmup
instructions.) Recycle the burner under these hot conditions
and measure the flame signal.
Check the pilot alone, the main burner flame alone, and
the main burner and pilot flames together (unless moni-
toring only the pilot flame when using intermittent igni-
tion, or only the main burner flame with direct spark
ignition). Check the signal at both high and low firing
rate, if applicable.
Also check the flame failure response time. Lower the
setpoint of the burner controller and observe the time it
takes for the Flame Indicator LED to go out after the burner
flame extinguishes (should be within four seconds).
If the flame signal is too low or is unsteady, check the
flame detector temperature. Relocate the flame detector if
the temperature is too high. If necessary, realign the sight-
ing to obtain the proper signal and response time. If the
response time is still too slow, replace the R7795. If the
detector is relocated or resighted, or the R7795 is replaced,
repeat all applicable tests in this section.
IMPORTANT: Repeat ALL required checkout tests af-
ter all adjustments have been completed. ALL tests
must be satisfactory when the flame detector is in its
FINAL position.
SAFE SHUTDOWN TESTS
Limit Action
With the burner operating, lower the high limit setting to
simulate an overheated boiler or furnace. Normal shutdown
should occur. Restore the normal light setting and the
burner should go through the normal prepurge, ignition,
and run cycle.
The use of manual reset limits is desirable to prevent the
system from cycling off the high limit, and to make sure
that the condition that caused the limit action is detected
and corrected as soon as possible.
Flame Failure
Let the burner operate five minutes; then manually
shut off the fuel supply to simulate flame failure. The
flame indicator LED should go out and the fuel valves
close. If the lockout on flame failure mode is chosen, the
R7795 will lock out in about 15 seconds. If the recycle
mode of operation is chosen, the system will purge and
then attempt to relight the pilot. After this attempt, the
system will lock out.
Power Failure
Let the burner run for five minutes. Simulate power
failure by opening the line switch. All relays should drop
out and the fuel valves should close. Close the power
switch. The R7795 should go through the complete nor-
mal cycle.
IMPORTANT: At the completion of all Checkout tests,
make sure that the R7795 is not on safety lockout,
that the pilot is turned up to the correct level, and all
limit settings are correct. Operate the system through
a normal cycle. Replace the device cover and tighten
the screw securely.
R7795A,B,C,D
CHECKOUT