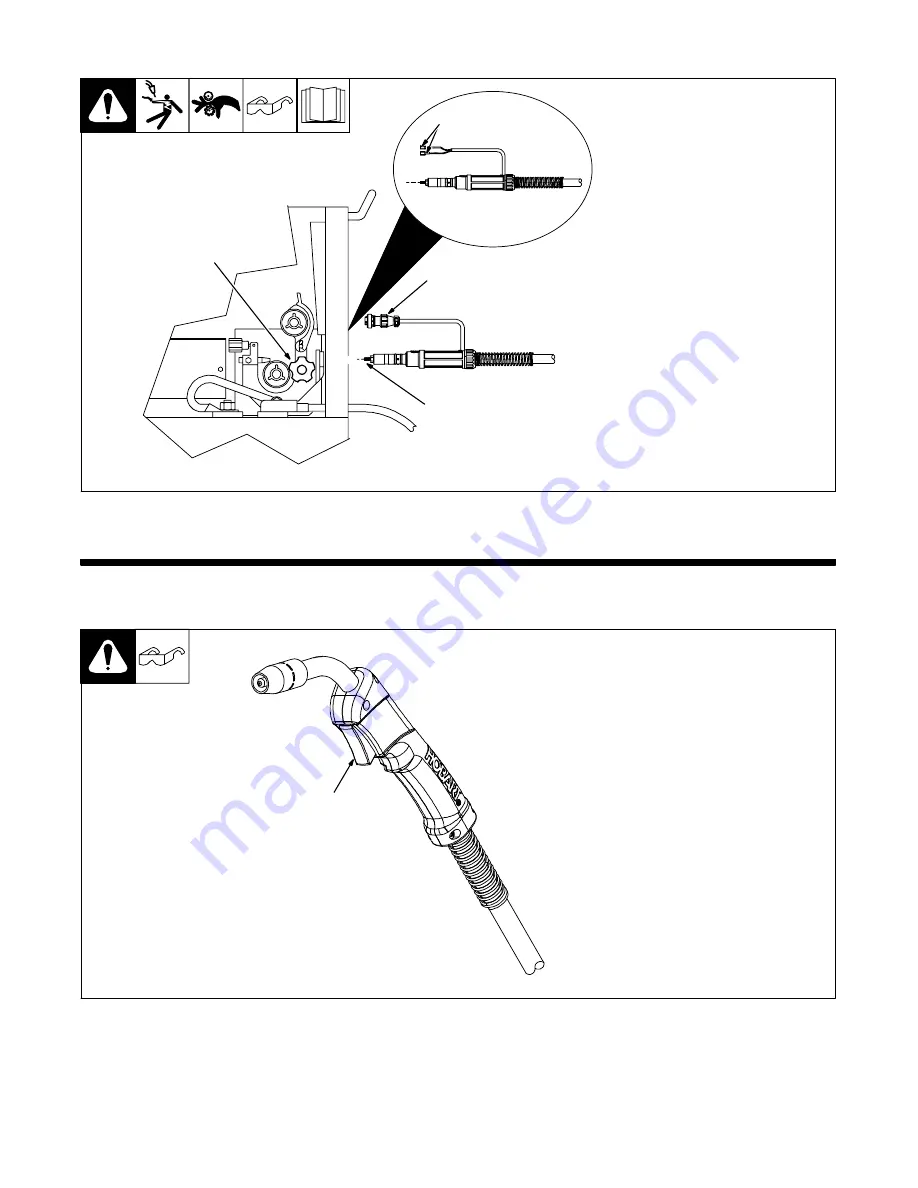
OM-245 987 Page 4
2-3. Installing Gun
243 861-A
1
Gun Securing Knob
2
Gun End
Loosen knob. Insert gun end until it
bottoms against drive assembly.
Tighten knob.
3
Gun Trigger Plug
Insert into receptacle, and tighten
threaded collar.
4
Friction Terminals
Some applications will require
cutting off trigger plug and installing
0.250 female friction terminals onto
end of leads.
See power source manual for
threading procedure.
1
3
2
4
SECTION 3
−
OPERATION
3-1. Operating The Gun
Ref. 243 838-A
1
Trigger Switch
When pressed, energized wire
feeds and shielding gas flows.
1
Содержание H100S4-10 Gun
Страница 4: ......
Страница 14: ...Notes ...