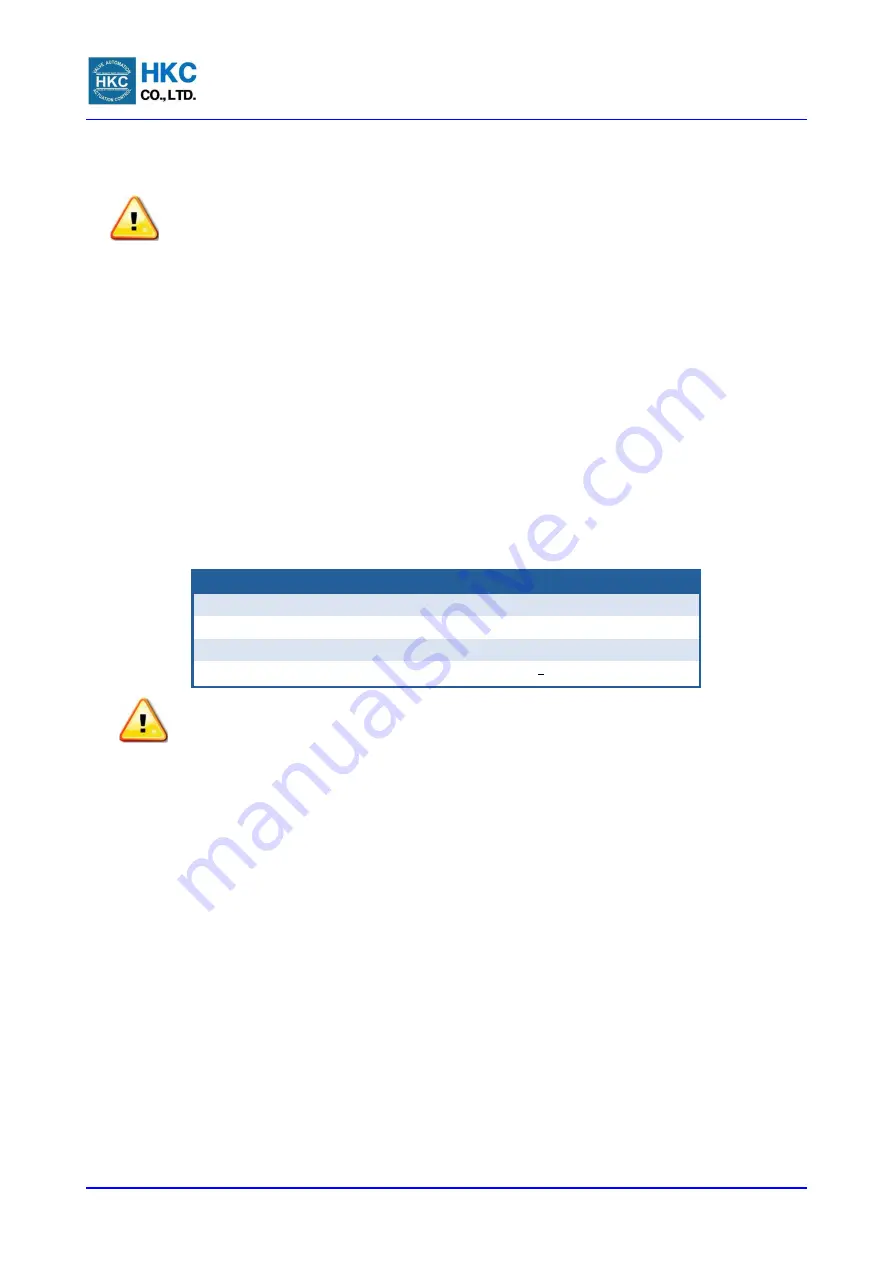
ET Series Heavy-duty Pneumatic Actuators
Installation Operation& Maintenance Manual
Doc No. : HUMG-ET-16 Rev0
Page 8 / 18
Valve Automation Leader, HKC
3.
Mounting and Operating
3.1.
Actuator Mounting
CAUTION:
Do not attempt to work on your HKC actuator without first shutting off its incoming
power, compressed air & related internal piping fluid
Note: Prior to mounting, the part-turn actuator must be checked for any damage
Damaged parts must be replaced by original spare parts
3.1.1.
Mounting is most easily done with the valve shaft pointing vertically upward. But mounting
is also possible in any other position; the actuator may be mounted in any position.
3.1.2.
The ET-series pneumatic actuators are supplied with a female drive output. The ISO5211
bolt patterns are provided for actuator mounting. The actuator drive bush is removable for
ease of machining.
3.1.3.
It is mandatory for the actuator to be firmly secured to a sturdy mounting bracket or
directly mounted to the valves’ ISO mounting pad. High tensile bolts or studs with spring
locking washers must be used.
3.1.4.
The valve output shaft must be in lined with the actuator output drive to avoid side-
loading the shaft. To avoid any backlash, flexibility in the mounting bracket or mounting
should not be allowed.
3.2.
Operating Pressure and Method
3.2.1.
The maximum operating Air supply pressure should not exceed 10bar (145psi). The air
supply should be clean, dry and lubricated. The following Table 3-1 contains information
regarding appropriate tube size which will provide enough air each actuator.
Table 3-1. Actuator Model and Tube Size
Cylinder Size
Inside-diameter of Tube
Ø 200 - 300
1/2 NPT
Ø 335 - 485
3/4 NPT
Ø 535 - 785
1 NPT
Ø 835 - 1250
1
NPT
CAUTION:
Before using an alternative air supply that is not of instrument quality, please
consult with HKC Co., Ltd.
3.3.
Working Principle
3.3.1.
Adjustment of the angle of Double Acting Actuator
①
Adjust the angle ± 5 degree with two bolts when the piston is operated back and forth at
90 degree
②
If you want to adjust the travel stops, first unfasten cap nut slightly and operate with a
spanner and then re-adjust.
3.3.2.
Double Travel working principle and solenoid valve attachment
①
When air is provided to center of the cylinder through port B of the actuator, piston
moves forward due to the air pressure. The rod, which is connected with piston, delivers
power to the Yoke. During this time, as the Yoke turns clockwise, the valve shaft is closed.
Additional air is vented out from port A.
②
Inversely to ①, air is provided to the center of the cylinder through port A of the actuator.
Everything basically operates in the opposite steps to ①
The operating principle and adjustment of the common assembly is as follows. Refer to
Figure 3-1 below.