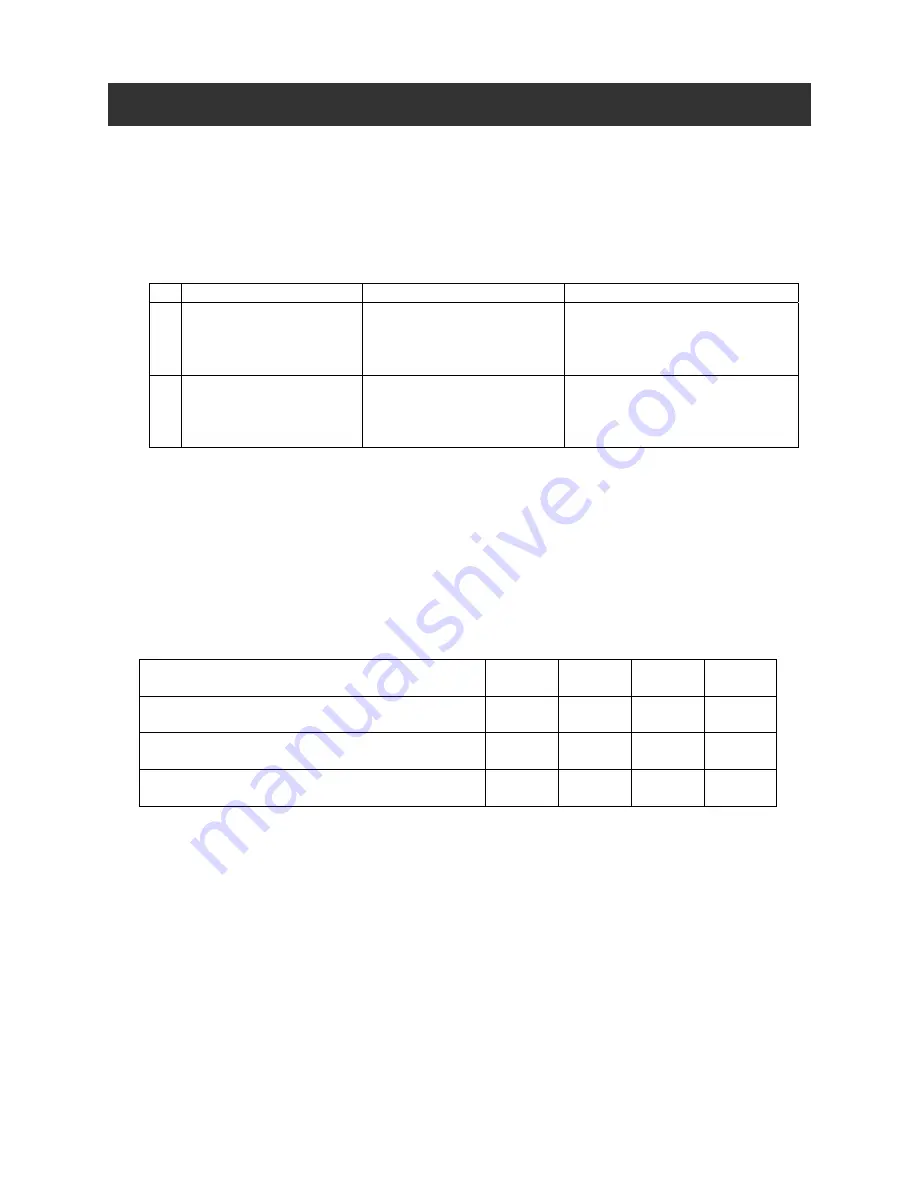
28
Chapter 7 FUNCTIONS
(Note 3) : N/D must be given as the ranges of 1/50
≤
(N/D)
≤
20.
(N: Electronic gear ratio numerator, D: Electronic gear ratio denominator)
(Note 4) : It depends on what type of main body combines with the SJ-FB, the setting
value conversion is different. Please refer to the (Note 3) of the “5.3 Items
regarding the feed back board of the inverter main body“.
Data setting of input-output terminals
Input-output terminal
With terminal assignment
Contents
Inp
ut
The pulse train position
command input
permission signal.
(STAT)
Set ‘48’ to one of
C001
∼
C008
Pulse train position command
input is valid while ON.
Outp
ut
Positioning completion
signal.(POK)
Set ‘23’ to one of
C021
∼
C025
Output when it entered into the
positioning completion range
Set ‘48’ (the pulse train position command input permission signal (STAT)) to one of
C001
∼
C008. Pulse train position command input is valid only in the case that the STAT terminal
is turned ON. In the case that the STAT terminal is OFF or unestablished, pulse train position
command input is invalid.
Below the example of the proportion of the slave side turn number to the master side turn number
by the setting of P019
~
P021 is shown. (Yet, the encoder pulse number of the master side and
slave side are same and be in the case of 1024 pulses. )
Position selection for electronic gear (P019)
01
(REF)
01
(REF)
00 (FB)
00 (FB)
Numerator of ration setting for electronic gear
(P020)
1024 2048 1024 2048
Denominator of ratio setting for electronic gear
(P021)
2048 1024 2048 1024
Slave side turn number to the master side turn
number
1/2 2 2 1/2