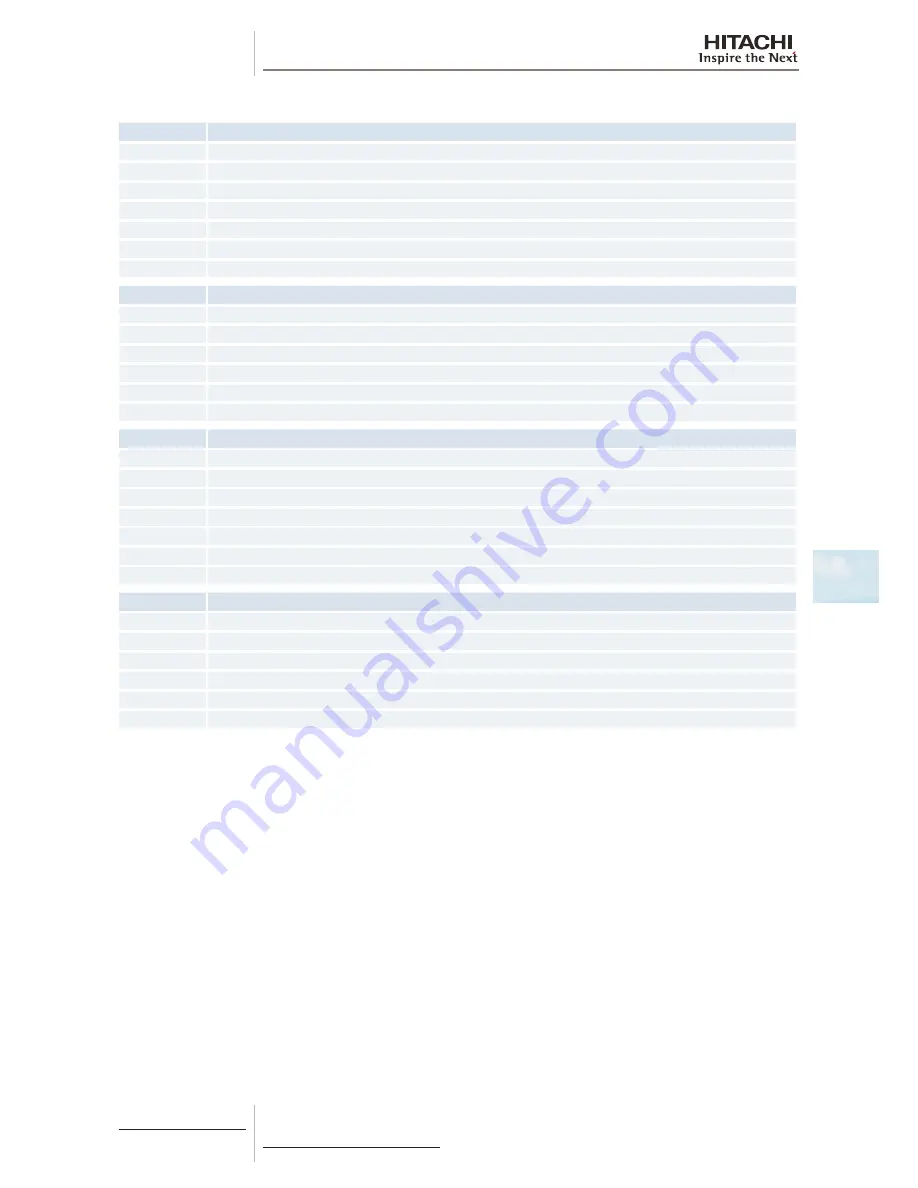
6 Optional functions
221
6
SMGB0077 rev.0 - 01/2013
DX-Interface series 1 - Input / Output signals
Input signal
Available from DX-Interface series 1
1
Control using the field-supplied room thermostat (cooling).
2
Control using the field-supplied room thermostat (heating).
3
Function 1 - remote ON/OFF of the unit (by contact).
4
Function2 - turns unit ON.(by pulse).
5
Function2 - turns unit OFF.(by pulse).
6
Cancellation of commands from remote control switch after forced stoppage.
7
Setting of the cooling mode or the heating mode.
Output signal
Available from DX-Interface series 1
1
Operation signal.
2
Alarm signal.
3
Cooling signal.
4
Thermo-ON signal.
5
Heating signal.
6
Defrost signal.
Input signal
Available from Outdoor unit
1
Control using the field-supplied room thermostat (cooling).
2
Control using the field-supplied room thermostat (heating).
3
Function 1 – remote ON/OFF of the unit (by contact).
4
Function2 - turns unit ON (by pulse).
5
Function2 - turns unit OFF (by pulse).
6
Cancellation of commands from remote control switch after forced stoppage.
7
Setting of the cooling mode or the heating mode.
Output signal
Available from Outdoor unit
1
Operation signal.
2
Alarm signal.
3
Cooling signal.
4
Thermo-ON signal.
5
Heating signal.
6
Defrost signal.
Thermo - On / Off control option
With DX-Interface series 1 it is possible to perform the thermo-On/thermo-Off control by three different ways.
• Standard thermo-On / thermo-Off control (Default setting).
Suitable for installations controlled by suction or discharge temperature.
The thermo-On / thermo-Off logic is decided based on the difference between the inlet temperature to the coil and the
set temperature on the remote controller or central controller.
•
By an external input.
The thermo-On / thermo-Off control can be driven externally by an input signal connected to the CN3 socket of the
PCB1 of the DX-Kit.
Setting note: DIP Switch 1 – Pin 6 of DX-Kit PCB2 (small PCB) must be switched on (PCB2-DSW1#6 switched ON).
Once the PCB DSW has been set, the input “i1” of CN3 is automatically set for thermo-On / thermo-Off control. The
setting of input “i2” is kept as set on the remote controller.
Please refer to Hitachi Indoor Units Service Manual for further information about the setting and connection of the
auxiliary inputs to CN3 socket.
•
By the duty signal.
For systems controlled by a duty signal it is possible to force the thermo-Off by the duty signal itself. When the duty
signal becomes the minimum of its range (0 V or 4 mA) the system will be switched to thermo-Off condition. To be
switched to thermo-On condition the duty must become higher than the 8% of its range.
Содержание RCD-2.5FSN2
Страница 2: ......
Страница 4: ...SMGB0077 rev 0 01 2013 IV Index ...
Страница 12: ...TCGB0077 rev 0 01 2013 XII Index ...
Страница 24: ......
Страница 102: ...2 Unit installation 90 SMGB0077 rev 0 01 2013 ...
Страница 180: ...4 Electrical wiring 168 SMGB0077 rev 0 01 2013 Wiring diagrams for RCIM 0 8 2 0 FSN2 ...
Страница 181: ...4 Electrical wiring 169 4 SMGB0077 rev 0 01 2013 Wiring diagrams for the RCI 1 0 6 0 FSN3Ei indoor units ...
Страница 182: ...4 Electrical wiring 170 SMGB0077 rev 0 01 2013 Wiring diagrams for the RCD 1 0 5 0 FSN2 indoor units ...
Страница 183: ...4 Electrical wiring 171 4 SMGB0077 rev 0 01 2013 Wiring diagrams for the RPC 2 0 6 0 FSN2E indoor units ...
Страница 184: ...4 Electrical wiring 172 SMGB0077 rev 0 01 2013 Wiring diagrams for the RPI M 0 8 6 0 FSN4E indoor units ...
Страница 185: ...4 Electrical wiring 173 4 SMGB0077 rev 0 01 2013 Wiring diagrams for the RPI 8 0 10 0 FSN3E indoor units ...
Страница 186: ...4 Electrical wiring 174 SMGB0077 rev 0 01 2013 Wiring diagrams for the RPK 0 8 1 5 FSN3M indoor units ...
Страница 187: ...4 Electrical wiring 175 4 SMGB0077 rev 0 01 2013 Wiring diagrams for the RPK 0 8 1 5 FSNH3M indoor units ...
Страница 188: ...4 Electrical wiring 176 SMGB0077 rev 0 01 2013 Wiring diagram for the RPK 2 0 4 0 FSN3M indoor unit ...
Страница 189: ...4 Electrical wiring 177 4 SMGB0077 rev 0 01 2013 Wiring diagrams for the RPF I 1 0 2 5 FSN2E indoor units ...
Страница 191: ...4 Electrical wiring 179 4 SMGB0077 rev 0 01 2013 DX Interface EXV 2 0 10 0 E1 ...
Страница 192: ...4 Electrical wiring 180 SMGB0077 rev 0 01 2013 ...
Страница 218: ......
Страница 264: ...7 Test run 252 SMGB0077 rev 0 01 2013 ...
Страница 276: ...9 Spare parts 264 SMGB0077 rev 0 01 2013 9 1 RCI 1 0 6 0 FSN3 SPN201201 ...
Страница 278: ...9 Spare parts 266 SMGB0077 rev 0 01 2013 9 2 RCI 1 0 1 6 FSN3Ei EPN 201204A ...
Страница 280: ...9 Spare parts 268 SMGB0077 rev 0 01 2013 9 3 RCIM 0 8 2 0 FSN2 Electr ical parts Drawing number EPN 0606A 3B Optional ...
Страница 282: ...9 Spare parts 270 SMGB0077 rev 0 01 2013 9 4 RCD 1 0 3 0 FSN2 ...
Страница 284: ...9 Spare parts 272 SMGB0077 rev 0 01 2013 9 5 RCD 4 0 5 0 FSN2 ...
Страница 286: ...9 Spare parts 274 SMGB0077 rev 0 01 2013 9 6 RPC 2 0 6 0 FSN2E ...
Страница 288: ...9 Spare parts 276 SMGB0077 rev 0 01 2013 9 7 RPI 0 8 1 5 FSN4E ...
Страница 290: ...9 Spare parts 278 SMGB0077 rev 0 01 2013 9 8 RPI 2 0 3 0 FSN4E EPN 201208A 1B ...
Страница 292: ...9 Spare parts 280 SMGB0077 rev 0 01 2013 9 9 RPI 4 0 6 0 FSN4E EPN 201208A 2B ...
Страница 294: ...9 Spare parts 282 SMGB0077 rev 0 01 2013 9 10 RPI 8 0 10 0 FSN3E EPN 201108A 1B ...
Страница 296: ...9 Spare parts 284 SMGB0077 rev 0 01 2013 9 11 RPIM 0 8 1 5 FSN4E DU EPN 201206A 2B ...
Страница 298: ...9 Spare parts 286 SMGB0077 rev 0 01 2013 9 12 RPK 0 8 1 0 FSN H 3M ...
Страница 300: ...9 Spare parts 288 SMGB0077 rev 0 01 2013 9 13 RPK 1 5FSN H 3M ...
Страница 302: ...9 Spare parts 290 SMGB0077 rev 0 01 2013 9 14 RPK 2 0 4 0 FSN3M ...
Страница 304: ...9 Spare parts 292 SMGB0077 rev 0 01 2013 9 15 RPF 1 0 2 5 FSN2E ...
Страница 306: ...9 Spare parts 294 SMGB0077 rev 0 01 2013 9 16 RPFI 1 0 2 5 FSN2E ...
Страница 308: ...9 Spare parts 296 SMGB0077 rev 0 01 2013 9 17 KPI 252 2002 E H 3E and KPI 502 1002 X3E ...
Страница 310: ...9 Spare parts 298 SMGB0077 rev 0 01 2013 9 18 DX Interface ...
Страница 311: ...9 Spare parts 299 9 SMGB0077 rev 0 01 2013 ...