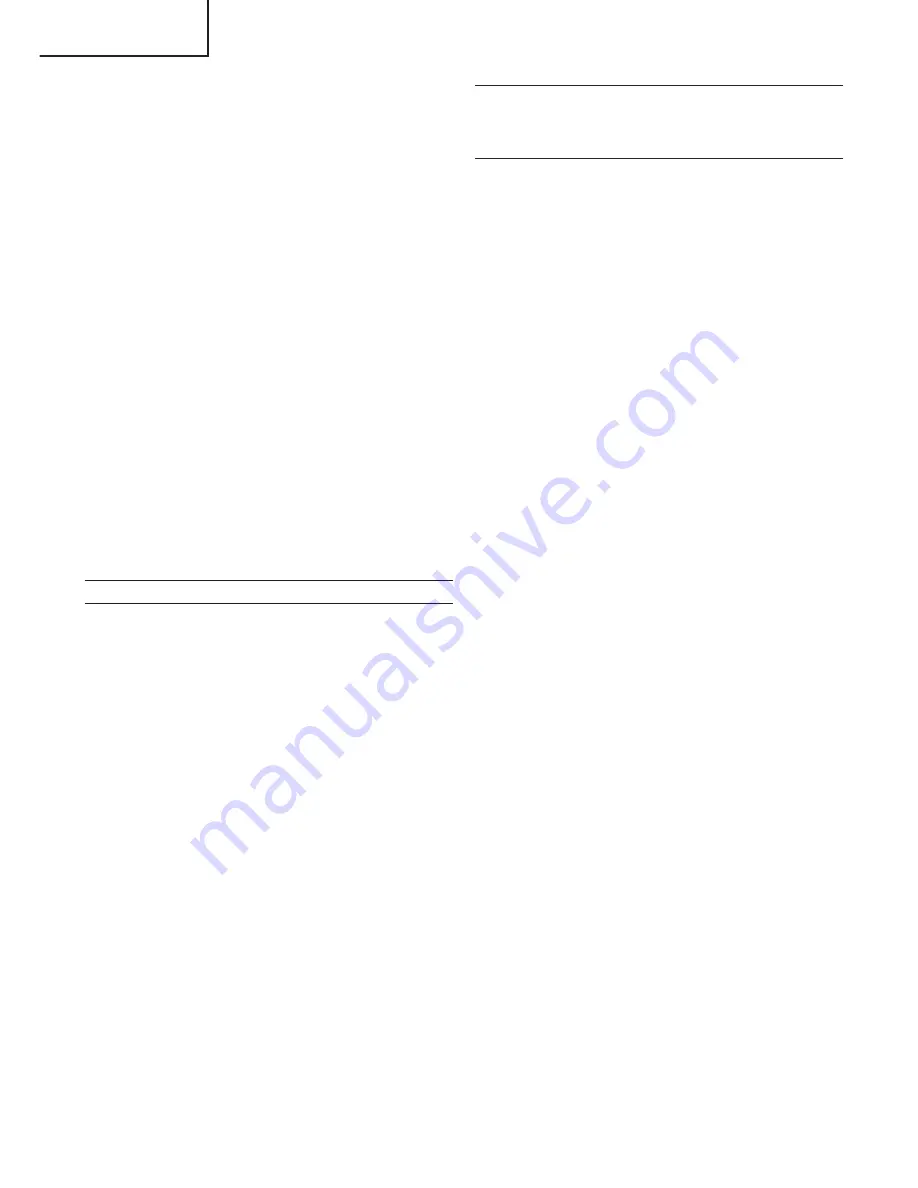
English
6
(3) Hold the tool firmly to control the tendency of the
tool to be kicked back by the material during cutting
operation.
(4) Ensure that the cutting depth is kept within 2~5mm
to prevent over-heating damage to the motor. Use
with moderate cutting speed, not to overload the
motor and do not apply excessive pressure on the
workpiece.
䡬
Mounting the Guide Base Assembly. (Fig. 4)
(1) Loosen the two small screws on the wheel guard.
(2) Insert the guide piece between the wheel guard and
set plate (A), and tighten one of the small screws.
Ensure that the guide will not move.
(3) Set the angle of the wheel guard to a suitable position
for operation, and securely tighten the remaining
small screw to fix the wheel guard in position.
䡬
Mounting the Diamond Wheel. (Fig. 5)
NOTE:
Mounting of the diamond wheel on the spindle is
illustrated in
Fig. 5
. Note that the wheel washer is
reversed from ordinary usage with depressed center
wheel.
(1) Mount the wheel washer and diamond wheel onto
the spindle.
(2) Mount the concave side of the wheel nut onto the
diamond wheel, and screw the wheel nut onto the
spindle.
(3) As shown in
Fig. 5
push in the lock pin to prevent
rotation of the spindle. Then, secure the diamond
wheel by tightening the wheel nut with the wrench.
MAINTENANCE AND INSPECTION
1. Inspecting the depressed center wheel
Ensure that the depressed center wheel is free of
cracks and surface defects.
Replace the depressed center wheel when it has been
worn out to about 60mm in external diameter.
2. Inspecting the mounting screws:
Regularly inspect all mounting screws and ensure
that they are properly tightened. Should any of the
screws be loose, retighten them immediately. Failure
to do so could result in serious hazard.
3. Maintenance of the motor
The motor unit winding is the very “heart” of the
power tool. Exercise due care to ensure the winding
does not become damaged and/or wet with oil or
water.
4. Inspecting the carbon brushes (Fig. 8)
The motor employs carbon brushes which are
consumable parts. Since an excessively worn carbon
brush can result in motor trouble, replace the carbon
brush with a new one having the same carbon brush
No. shown in the figure when it becomes worn to or
near the “wear limit”. In addition, always keep carbon
brushes clean and ensure that they slide freely within
the brush holders.
5. Replacing carbon brushes:
Disassemble the brush caps with a slotted-head
screwdriver. The carbon brushes can then be easily
removed.
NOTE
Due to HITACHI’s continuing program of research and
development, the specifications herein are subject to
change without prior notice.
Содержание PDA-100H
Страница 12: ...11 ...
Страница 13: ...301 Code No C99119531 N Printed in Japan ...