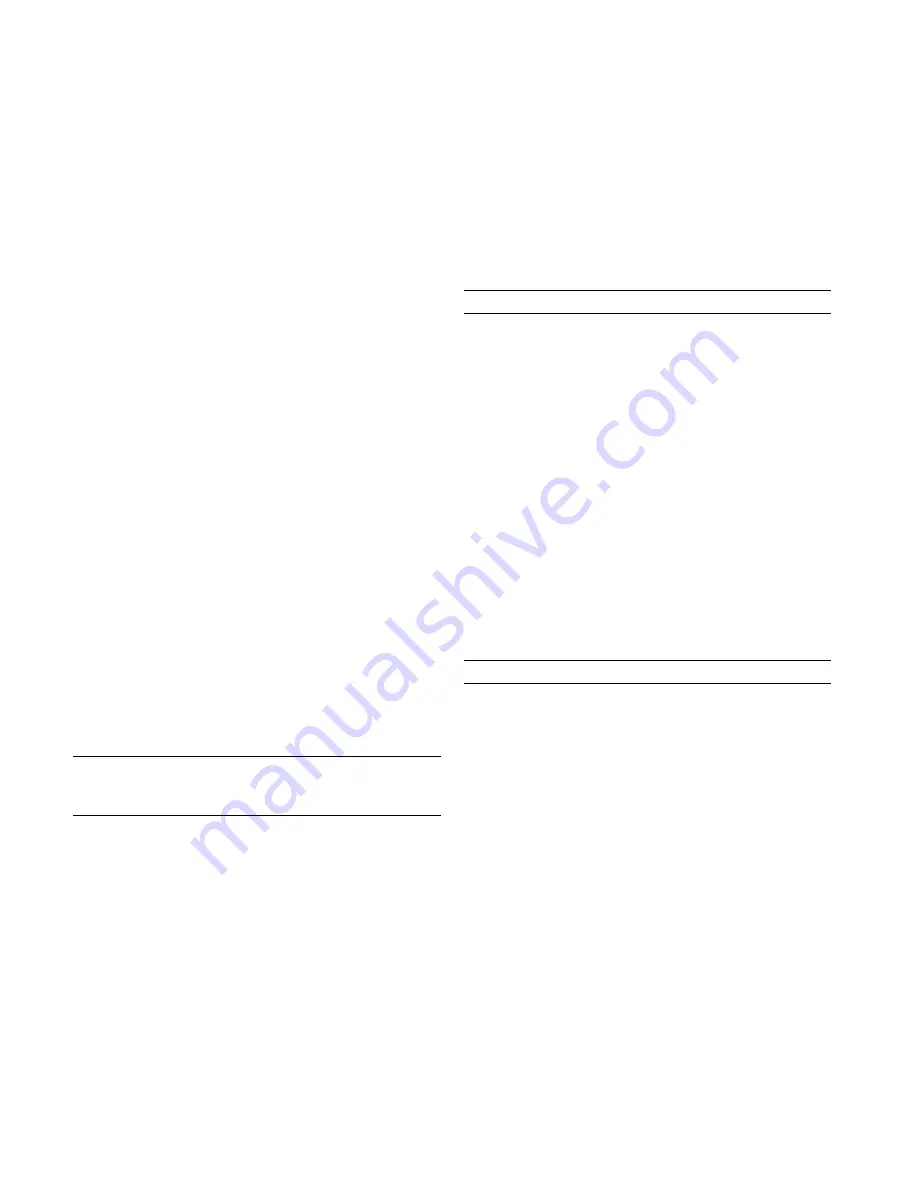
10
CAUTION
䡬
Be careful not to injure your hands.
2. Carbide blade assembly:
CAUTION
䡬
Prior to assembly, thoroughly wipe off all swarf
accumulated on the carbide blade.
(1) As shown in
Fig. 10
, lift set plate (B) and insert
the new carbide blade between cutter block and set
plate (B).
(2) As shown in
Fig. 11
, mount the new carbide blade
by sliding it on the set plate (B) so that the blade
tip projects by 1mm from the end of the cutter block.
(3) As shown in
Fig. 12
, fix the bolts at the blade holder
after blade replacement has been completed.
(4) Turn the cutter block over, and set the other side
in the same manner.
3. Adjustment of carbide blade height:
CAUTION
䡬
If the carbide blade’s heights are inaccurate after
above procedures have been completed, carry out
the procedures described below.
(1) As shown in
Fig. 13
, use the box wrench to loosen
the three bolts used to retain the carbide blade, and
remove the blade holder.
(2) As shown in
Fig. 14
, after removing the carbide
blade, slide set plate (B) in the direction indicated
by the arrow to disassemble set plate (B).
(3) Loosen the 2 screws holding on the carbide blade
and set plate (A), set plate (B).
(4) As shown in
Fig. 15, 16
, press the turned surface
of set plate (A) to the wall surface b while adjusting
the carbide blade edge to the wall surface a of the
set gauge. Then, tighten them with the 2 screws.
(5) As shown in
Fig. 17, 18
, insert a turned portion of
set plate (A) attached to set plate (B) into a groove
on the flat portion of the cutter block.
(6) As shown in
Fig. 19
, place the blade holder on the
completed assembly and fasten it with the three
bolts. Ensure that the bolts are securely tightened.
Follow the same procedures for the opposite side
carbide blade.
BLADE ASSEMBLY AND DISASSEMBLY AND
ADJUSTMENT OF BLADE HEIGHT (FOR
RESHARPENABLE BLADE TYPE)
1. Blade disassembly:
(1) As shown in
Fig. 13
, use the accessory box wrench
to loosen the three bolts used to retain the blade,
and remove the blade holder.
(2) As shown in
Fig. 14
, slide the blade in the direction
indicated by the arrow to disassemble the blade.
CAUTION
䡬
Be careful not to injure your hands.
2. Blade assembly:
CAUTION
䡬
Prior to assembly, thoroughly wipe off all swarf
accumulated on the blade.
(1) Insert a turned portion of set plate (A) attached to
the blade into a groove on the flat portion of the
cutter block. (
Fig. 17, 20
)
Set the blade so that both sides of the blade protrude
from the width of the cutter block by about 1 mm
(
Fig. 21
)
(2) Place the blade holder on the completed assembly,
as shown in
Fig. 22
, and fasten it with the three
bolts. Ensure that the bolts are securely tightened.
(3) Turn the cutter block over, and set the opposite side
in the same manner.
3. Adjustment of blade height:
(1) Loosen the 2 screws holding on the blade and set
plate (A).
(2) Press the turned surface of set plate (A) to the wall
surface
b
while adjusting the blade edge to the wall
surface
a
of the set gauge. Then, tighten them with
the 2 screws. (
Fig. 15, 23
)
SHARPENING THE RESHARPENABLE BLADES
Use of the accessory Blade Sharpening Ass'y is recom-
mended for convenience.
1. Use of Blade Sharpening Ass'y
As shown in
Fig. 24
, two blades can be mounted
on the blade sharpening ass'y to ensure that the
blade tips are ground at uniform angles. During
grinding, adjust the position of the blades so that
their edges simultaneously contact the dressing
stone as shown in
Fig. 25
.
2. Blade sharpening intervals
Blade sharpening intervals depend on the type of
wood being cut and the cutting depth. However,
sharpening should generally be effected after each
500 meters of cutting operation.
3. Dressing Stone
When a water dressing stone is available, use it
after dipping it sufficiently in water since such a
dressing stone may be worn during grinding works,
flatten the upper surface of the dressing stone as
often as necessary.
MAINTENANCE AND INSPECTION
1. Inspecting the blades:
Continued use of dull or damaged blades will result
in reduced cutting efficiency and may cause over-
loading of the motor. Sharpen or replace the blades
as often as necessary.
2. Handling
CAUTION
䡬
The front base, rear base, and cutting depth control
knob are precisely machined to obtain specifically
high precision. If these parts are roughly handled
or subjected to heavy mechanical impact, it may
cause deteriorated precision and reduced cutting
performance. These parts must be handled with
particular care.
3. Inspecting the mounting screws:
Regularly inspect all mounting screws and ensure
that they are properly tightened. Should any of the
screws be loose, retighten them immediately. Fail-
ure to do so could result in serious hazard.
4. Inspecting the carbon brushes (Fig. 26)
The motor employs carbon brushes which are con-
sumable parts. Since an excessively worn carbon
brush can result in motor trouble, replace the carbon
brushes with new ones having the same carbon
brush No. shown in the figure when it becomes
worn to or near the “wear limit”. In addition, always