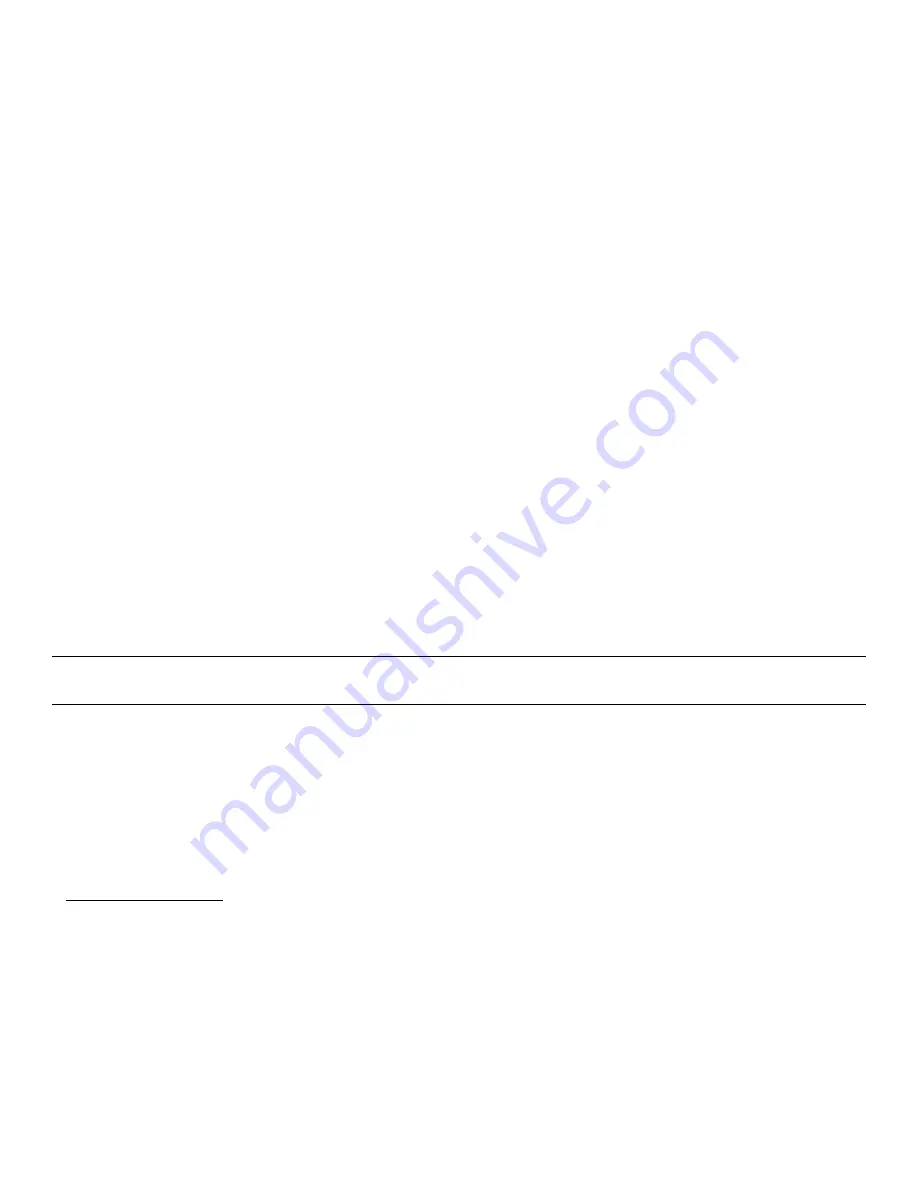
Technical white paper
Page 21
The specialized, air-ride, padded-van carriers usually have the ability to perform site surveys. Among other elements, the site survey should
address the following in general terms:
•
What are the hours the facility is open for deliveries? Can delivery be done during the day during normal business hours?
•
Are appointments required?
•
Does the receiving dock require union labor? Is there a site contact?
•
Are there any security or building access issues? Is there a site contact?
•
Does the facility have a dock? Is the delivery dock a standard raised dock? Can a 53-foot trailer gain access? Are there any restrictions on the
size, length, width, or height of the truck permitted?
•
On what floor in the building will the equipment be installed? This information is in consideration of height and width clearances along the
way: doors, light fixtures, cable trays, sprinkler heads, elevators, and so on.
•
What are the door height clearances (width and height) for freight elevators, doorways, or other obstacles?
•
If equipment is not going on the first floor, is there an elevator? If yes, what is the weight capacity of the elevator?
•
Is the path from the loading dock to the computer room robust enough to support the weight of the configured rack?
•
Is there a delivery, unpacking, or staging area? Does the customer allow cardboard boxes and other packing material in the computer room?
Does the customer have a clean-up requirement—for example, is complete trash removal required within one or two days after installation?
•
Is there a raised floor or are there any thresholds of concern? If there is a raised floor, how deep is it? Is there a ramp? What sort of equipment
maneuvering is required to gain access? Are there special equipment needs? For example, will any stair walkers, lifters, cranes, ramps, steel
plates, or floor covers be required to place the equipment in the computer room? Is the raised floor rated to accommodate the planned point
load weight of the rack?
•
Will the rack be removed from the pallet at a location other than the final installation location?
•
Is movement across rough surfaces likely?
Note
HPE does not advocate tipping loaded racks to navigate height-restricted doorways.
General considerations
Before beginning these procedures on any shipment, understand and follow these precautions.
The following are the minimum requirements for qualifying components for shipment in HPE Infrastructure Racks mounted on a CTO shock
pallet:
•
The shock pallet is a one-way pallet and should not be reused. A reused cushioned pallet may not protect the rack and server components in
transit. If a data center or loaded rack move is being scheduled, it is strongly recommended that the shock pallet spares kit is purchased and all
safety considerations be addressed. For a complete list of HPE rack options and accessories, refer to the main rack page at
hpe.com/info/rackandpower
•
Use a torque wrench to tighten all front panel mounting hardware and rail or slide connections to 2.2594 N-m (20 in-lb.). Use provided
mounting hardware to secure any spring-loaded slide assemblies to the mounting rails.
•
Use the shipping hardware or additional clamping or hold-down brackets provided with each component. This hardware is typically found in
the accessory box. The Server Immobilization Bolt is a large orange thumbscrew and is easily installed from the rear of the rack.
•
Dress and secure all data and power cables. Cables and cable management arms should be tie wrapped to prevent movement of cables that
may place a load on connector assemblies or may cause fraying due to friction. Wire-formed cable management clamps are provided with each
rack for this purpose. Some components provide sheet metal cable management extensions or spring-loaded cable retention reels that should
be utilized in all cases. Ensure that front and rear doors are firmly closed.
•
Reuse any packaging materials that were initially provided with the rack.