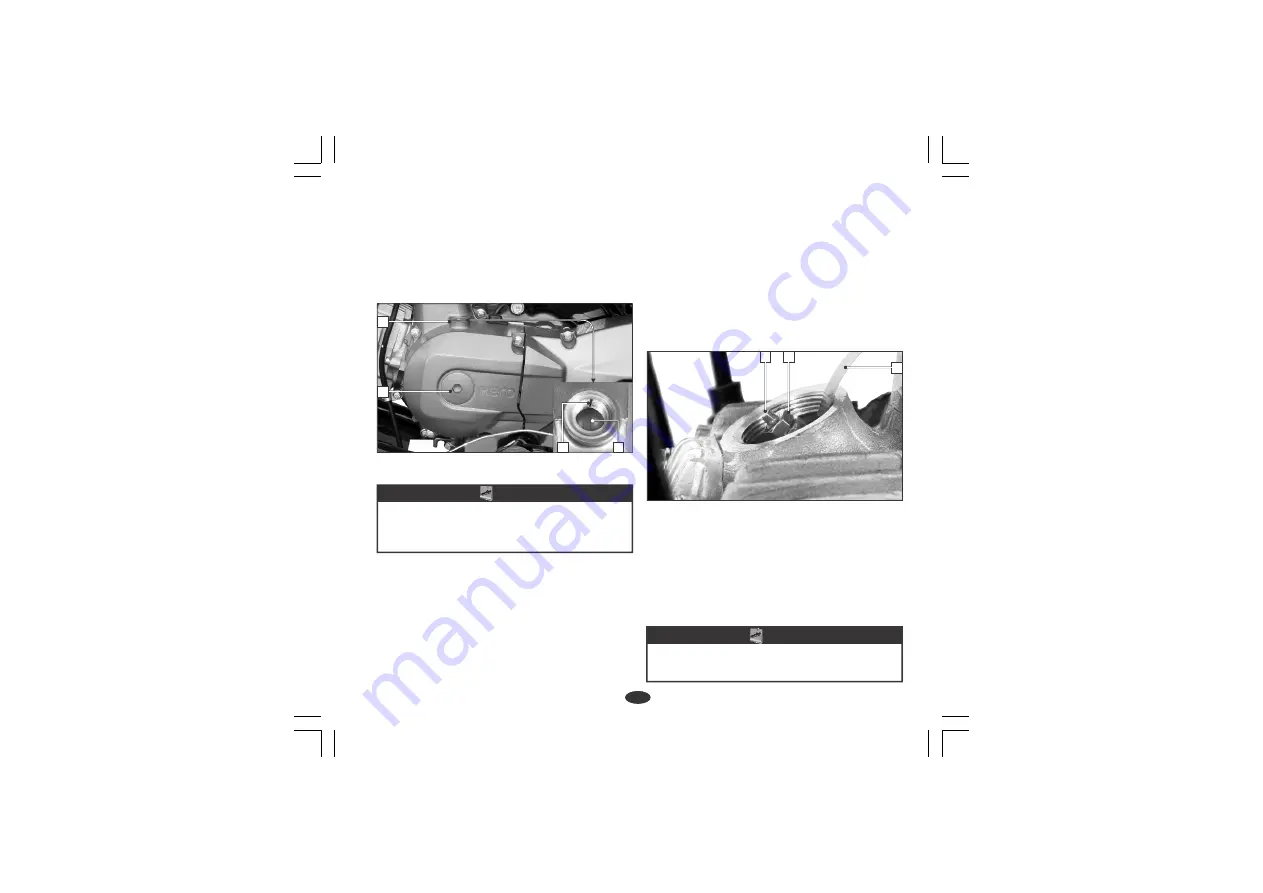
VALVE CLEARANCE
Excessive valve clearance will cause noise, and
little or no clearance will prevent the valve
from closing and cause valve damage and
power loss. Check valve clearance at the
specified intervals
(page 30).
The adjustment must be made when the
piston is at Top Dead Center and both the
inlet and exhaust valves are closed.
î
Rotate the flywheel anticlockwise until the ‘T’
mark (3) on the flywheel coincides with the
index mark (4) on the left crank case cover.
In this position the piston will either be on the
compression or exhaust stroke.
î
Remove the crankshaft hole cap (1),
timing hole cap (2) and tappet covers.
The checking or adjusting of valve clearance
should be performed while the engine is cold.
The clearance will change as the engine
temperature rises.
NOTE
4
3
2
1
(1) Crankshaft hole cap (2) Timing hole cap
(3) 'T' mark (4) Index mark
Adjust by loosening the lock nut (7) and turning
the adjusting screw until there is a slight
drag on the feeler gauge. After tightening the lock
nut, check again the clearance.
Intake : 0.10 mm Exhaust : 0.10 mm
î
Install the parts in the reverse order of
disassembly.
Standard clearance (cold condition)
(5)Feeler gauge(6)Adjusting screw(7)Lock nut
If they are tight, the valves are open, rotate the
O
flywheel 360 anticlockwise and re-align the
'T' mark with the index mark.
î
Check the clearance by inserting the feeler
gauge (5) between the adjusting screw (6)
and valve stem.
This condition can be determined by moving
the rocker arms. If they are free, it is an
indication that the valves are closed and the
piston is in compression stroke.
5
6 7
Before inserting the feeler gauge, smear a bit
of engine oil on the feeler gauge to avoid
damage to the feeler gauge.
NOTE
29