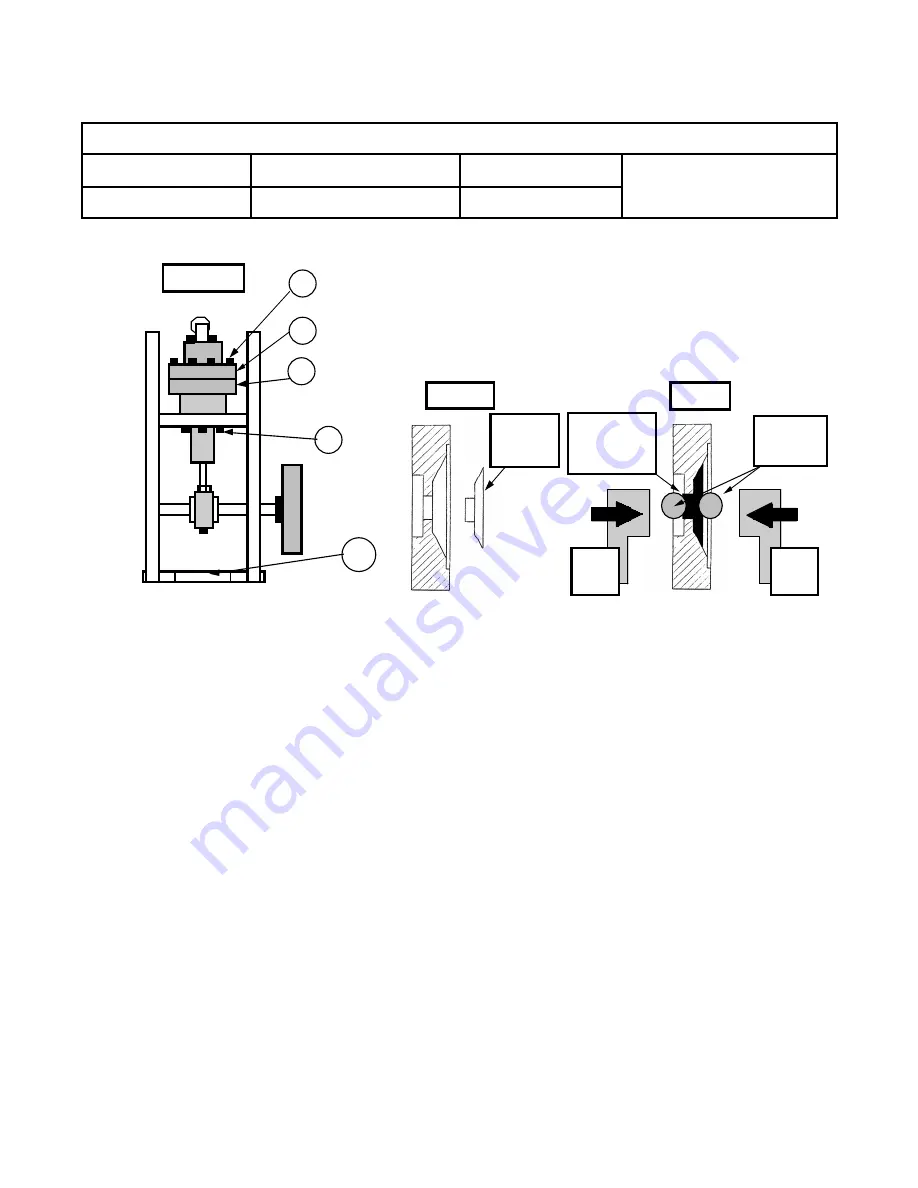
H.E.R.O. INDUSTRIES
300S / 300SL LEGEND Owner’s Manual
27
HYDRAULIC HEAD INSERT REPLACEMENT
1. Tilt unit up onto its’ nose ( resting vertically on handle, ref# 130). See Fig. 1.
2. Remove the eight bolts ( ref# 17) securing the paint head ( ref# 18) to the hydraulic head ( ref# 53).
3. Place rags around the cylinder area to absorb hydraulic oil which will leak while performing step 4.
4. Remove the six bolts ( ref# 59 ) securing the crossblock/cylinder/hydraulic head. Bolts are
accessed from the underside of crossblock.
5. Remove hydraulic head ( ref# 53) to work bench.
6. Remove old, broken or damaged insert ( ref# 55).
NOTE:
Insert should have no movement, when properly installed. If it is spinning or able to
move back and forth, but has not come completely free of the hydraulic head, it may be possible
to re-tighten using the same installation instructions to follow. See steps 8 – 10.
7. Place new insert into the hydraulic head. See fig. 2. Insert will protrude through the hydraulic head
by approximately 1/8”. To affix the insert the extra material of the insert must be flared to secure to
the hydraulic head.
8. Position a steel ball on the front and back of the insert. See figure 3.
9. Position this assembly in the jaws of a vise.
10. Slowly close the vise jaws. The vise acts as a press and the ball will cause the extra insert material
to flair around the head. Continue closing vise until the insert is tight and can no longer be rotated
or spin in the hydraulic head. Over tightening can create cracks or splits in the flange/flare, leading
to repeat failures. Do Not over tighten.
11. Re-assemble pump, in the reverse order of removal. Torque all bolts to 30 foot pounds.
12. Once the repairs are completed , return unit to horizontal position, replenish lost oil and purge per
instructions on page 19.
Fig. 2.
Fig. 3
Steel ball
( 17S )
Vise
jaws
This small lip
will roll over
to secure
Vise
jaws
Insert
23A-1
Tools or Supplies Required
♦
1/4 Allan wrench
♦
4-45-3 Pressure cap
♦
Torque Wrench
♦
Vise
♦
H.E.R.O. hydraulic oil
♦
Rags
♦
17S Balls ( 2 ) Slightly
used. May damage new.
Fig. 1
59
18
53
17
130