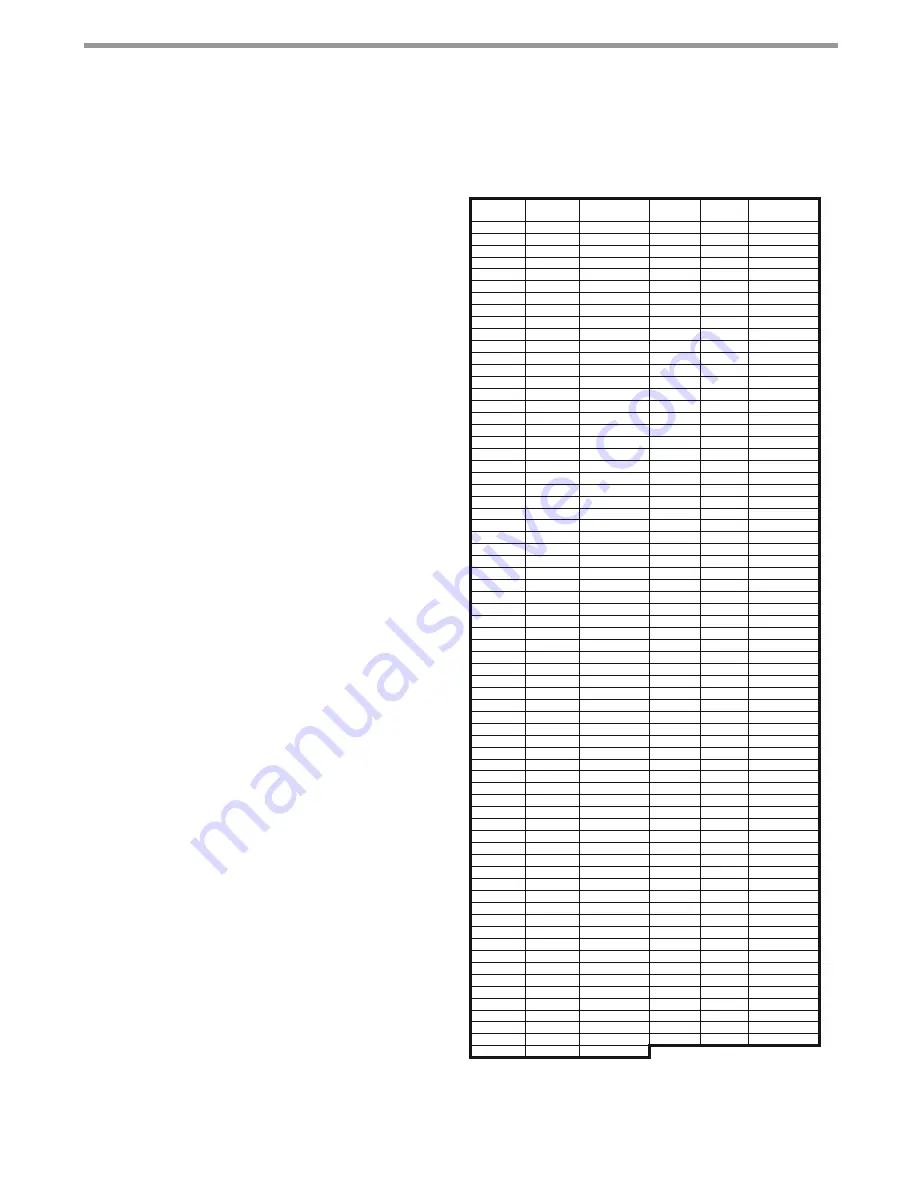
T h e Q u a l i t y L e a d e r i n C o n d i t i o n i n g A i r
R e s i d e n t i a l S p l i t - 6 0 H z R 4 1 0 A
R e v. : 0 3 A u g u s t , 2 0 1 2
www.heatcontroller.com
35
Basic Troubleshooting Information
General Troubleshooting
Basic DXM2 board troubleshooting in general is best
summarized as simply verifying inputs and outputs. After this
process has been veri
fi
ed, con
fi
dence in board operation is
con
fi
rmed and the trouble must be else where. Below are
some general guidelines required for developing training
materials and procedures when applying the DXM2 Control.
DXM2 Field Inputs
All conventional inputs are 24VAC from the thermostat and
can be veri
fi
ed using a voltmeter between C and Y1, Y2, W,
O, and G.
Sensor Inputs
All sensor inputs are ‘paired wires’ connecting each
component with the board. Therefore continuity on pressure
switches can be checked at the board connector.
The thermistor resistance should be measured with the
connector removed so that only the impedance of the
thermistor is measured. If desired, this reading can be
compared to the chart shown in the thermistor section of this
manual based upon the actual temperature of the thermistor
clip. An ice bath can be used to check calibration of a
thermistor if needed.
DXM2 Outputs
The compressor relay is 24VAC and can be veri
fi
ed using a
voltmeter. The Alarm Relay can either be 24VAC as shipped
or dry contacts (measure continuity during fault) for use with
DDC by clipping the J4 jumper. Electric heat outputs are
24VDC and require a voltmeter set for DC to verify operation.
When troubleshooting, measure from 24VDC terminal to EH1
or EH2 terminals.
Test Mode
Test Mode can be entered for 20 minutes by pressing
the Test button. For Diagnostic ease at a conventional
thermostat, the Alarm Relay will also cycle during test mode.
The Alarm Relay will cycle on and off similar to the Fault
LED to indicate a code representing the last fault, at the
thermostat. Test Mode can also be entered and exited by
cycling the G input, 3 times within a 60 second time period.
Sensor: Nominal resistance at various temperatures
Temp (ºC)
Temp (ºF)
Resistance
(kOhm)
Temp (ºC) Temp (ºF)
Resistance
(kOhm)
-17.8
0.0
85.34
55
131.0
2.99
-17.5
0.5
84.00
56
132.8
2.88
-16.9
1.5
81.38
57
134.6
2.77
-12
10.4
61.70
58
136.4
2.67
-11
12.2
58.40
59
138.2
2.58
-10
14.0
55.30
60
140.0
2.49
-9
15.8
52.38
61
141.8
2.40
-8
17.6
49.64
62
143.6
2.32
-7
19.4
47.05
63
145.4
2.23
-6
21.2
44.61
64
147.2
2.16
-5
23.0
42.32
65
149.0
2.08
-4
24.8
40.15
66
150.8
2.01
-3
26.6
38.11
67
152.6
1.94
-2
28.4
36.18
68
154.4
1.88
-1
30.2
34.37
69
156.2
1.81
0
32.0
32.65
70
158.0
1.75
1
33.8
31.03
71
159.8
1.69
2
35.6
29.50
72
161.6
1.64
3
37.4
28.05
73
163.4
1.58
4
39.2
26.69
74
165.2
1.53
5
41.0
25.39
75
167.0
1.48
6
42.8
24.17
76
168.8
1.43
7
44.6
23.02
77
170.6
1.39
8
46.4
21.92
78
172.4
1.34
9
48.2
20.88
79
174.2
1.30
10
50.0
19.90
80
176.0
1.26
11
51.8
18.97
81
177.8
1.22
12
53.6
18.09
82
179.6
1.18
13
55.4
17.26
83
181.4
1.14
14
57.2
16.46
84
183.2
1.10
15
59.0
15.71
85
185.0
1.07
16
60.8
15.00
86
186.8
1.04
17
62.6
14.32
87
188.6
1.01
18
64.4
13.68
88
190.4
0.97
19
66.2
13.07
89
192.2
0.94
20
68.0
12.49
90
194.0
0.92
21
69.8
11.94
91
195.8
0.89
22
71.6
11.42
92
197.6
0.86
23
73.4
10.92
93
199.4
0.84
24
75.2
10.45
94
201.2
0.81
25
77.0
10.00
95
203.0
0.79
26
78.8
9.57
96
204.8
0.76
27
80.6
9.16
97
206.6
0.74
28
82.4
8.78
98
208.4
0.72
29
84.2
8.41
99
210.2
0.70
30
86.0
8.06
100
212.0
0.68
31
87.8
7.72
101
213.8
0.66
32
89.6
7.40
102
215.6
0.64
33
91.4
7.10
103
217.4
0.62
34
93.2
6.81
104
219.2
0.60
35
95.0
6.53
105
221.0
0.59
36
96.8
6.27
106
222.8
0.57
37
98.6
6.01
107
224.6
0.55
38
100.4
5.77
108
226.4
0.54
39
102.2
5.54
109
228.2
0.52
40
104.0
5.33
110
230.0
0.51
41
105.8
5.12
111
231.8
0.50
42
107.6
4.92
112
233.6
0.48
43
109.4
4.72
113
235.4
0.47
44
111.2
4.54
114
237.2
0.46
45
113.0
4.37
115
239.0
0.44
46
114.8
4.20
116
240.8
0.43
47
116.6
4.04
117
242.6
0.42
48
118.4
3.89
118
244.4
0.41
49
120.2
3.74
119
246.2
0.40
50
122.0
3.60
120
248.0
0.39
51
123.8
3.47
121
249.8
0.38
52
125.6
3.34
122
251.6
0.37
53
127.4
3.22
123
253.4
0.36
54
129.2
3.10